Choosing an Electrical Switch
More
Miniature Rotary Motion Position-Measuring Transmitters
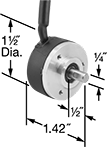
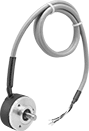
Often used with servomotors, these transmitters have a mounting hole pattern that fits a three-hole 28 mm BC servomotor face. Also known as encoders, these miniature transmitters convert rotary motion to an electrical signal that indicates distance, direction, and speed of travel. They're commonly used in control systems to automate servomotors, robotics, and assembly machines.
Transmitters have NPN Open Collector output that requires a pull-up resistor (not included) for operation. Output channel Z is also known as an index channel. You must use transmitters with a controller that has quadrature detection to get a 4X resolution increase. All meet IP64 for protection from dust and water spray.
Use a flexible shaft coupling (not included) to connect the transmitter shaft to a drive shaft.
Mount. Holes | |||||||||||||||
---|---|---|---|---|---|---|---|---|---|---|---|---|---|---|---|
Output Channels | Resolution Increase | For Max. Shaft Speed, rpm | Input Voltage | Max. Input Current, mA | Output Current, mA | Shaft Coupling Required | Body Material | Housing Material | Shaft Material | Thread Size | Thread Pitch, mm | Fasteners Included | Choose a Resolution | Each | |
Quadrature with Index Output Channel | |||||||||||||||
A, B, Z | 2X, 4X | 8,000 | 5V DC-28V DC | 65 | 20 | Yes | Aluminum | Plastic | Stainless Steel | M3 | 0.5 | No | 000000 | 0000000 |
Miniature Rotary Motion Position-Measuring Transmitters with Mounting Plate
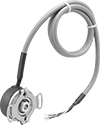
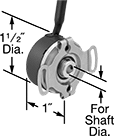
Slide one of these transmitters onto a motor shaft in your application—they have a flexible mounting plate that compensates for shaft misalignment and vibration. Also known as encoders, these miniature transmitters convert rotary motion to an electrical signal that indicates distance, direction, and speed of travel. They're often used to automate servomotors, robotics, and assembly machines.
Transmitters have NPN Open Collector output that requires a pull-up resistor (not included) for operation. Output channel Z is also known as an index channel. You must use transmitters with a controller that has quadrature detection to get a 4X resolution increase. All meet IP64 for protection from dust and water spray.
Mount. Holes | |||||||||||||||
---|---|---|---|---|---|---|---|---|---|---|---|---|---|---|---|
For Shaft Diameter | Output Channels | Resolution Increase | For Max. Shaft Speed, rpm | Input Voltage | Max. Input Current, mA | Output Current, mA | Body Material | Housing Material | Mount. Plate Wd. | Ctr.-to-Ctr. | Thread Size | Fasteners Included | Choose a Resolution | Each | |
Quadrature with Index Output Channel | |||||||||||||||
1/4" | A, B, Z | 2X, 4X | 8,000 | 5V DC-28V DC | 65 | 20 | Aluminum | Plastic | 2.16" | 1.81" | 6-32 | No | 000000 | 0000000 | |
3/8" | A, B, Z | 2X, 4X | 8,000 | 5V DC-28V DC | 65 | 20 | Aluminum | Plastic | 2.16" | 1.81" | 6-32 | No | 000000 | 000000 |
Sanitary Rotary Motion Position-Measuring Transmitters
Also known as encoders, these sanitary transmitters convey motion to an electrical signal that conveys distance, direction, and speed. They’re often used in control systems to automate servomotors, robotics, and assembly machines in sanitary environments such as food and pharmaceutical plants. Made of corrosion-resistant stainless steel, they won’t rust from frequent washdowns with harsh cleaners. These transmitters are sealed and have a highly polished surface, leaving no room for bacteria to grow and making them easier to clean. They’re rated IP67 for protection from dust, high-pressure jets of water, and submersion in up to a meter of water for 30 minutes.
To achieve a 4X resolution increase, use these transmitters with a controller that has quadrature detection.
Transmitters with three mounting holes are designed to fit on a three-hole servomotor face.
Connect transmitters to counters and controllers with cables (sold separately).
Use a flexible shaft coupling to connect the transmitter shaft to a drive shaft.
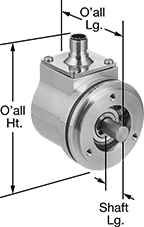
Overall | Shaft | Mounting Holes | ||||||||||||||
---|---|---|---|---|---|---|---|---|---|---|---|---|---|---|---|---|
For Counter Function | Output Channels | Resolution | Resolution Increase | For Max. Shaft Speed, rpm | Input Voltage | Lg. | Ht. | Dia. | Lg. | Mounting Plate Dia. | No. of | Ctr.-to-Ctr. | Thread Size | Specifications Met | Each | |
316 Stainless Steel Body and 303 Stainless Steel Shaft | ||||||||||||||||
Quadrature with Index Output Channel—20mA Output Current | ||||||||||||||||
Up and Down | A, B, Z | 600 | 2X, 4X | 8,000 | 4.75-28V DC | 2.44" | 3.13" | 0.4" | 0.4" | 2.29" | 3 | 1.43" | M4 × 5 mm | CE Marked | 00000000 | 0000000 |
Up and Down | A, B, Z | 3,600 | 2X, 4X | 8,000 | 4.75-28V DC | 2.44" | 3.13" | 0.4" | 0.4" | 2.29" | 3 | 1.43" | M4 × 5 mm | CE Marked | 00000000 | 00000000 |
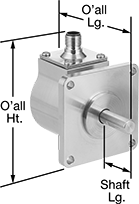
Overall | Shaft | Mounting Plate | Mounting Holes | ||||||||||||||
---|---|---|---|---|---|---|---|---|---|---|---|---|---|---|---|---|---|
For Counter Function | Output Channels | Resolution | Resolution Increase | For Max. Shaft Speed, rpm | Input Voltage | Lg. | Ht. | Dia. | Lg. | Lg. | Wd. | No. of | Ctr.-to-Ctr. | Dia. | Specifications Met | Each | |
316 Stainless Steel Body and 303 Stainless Steel Shaft | |||||||||||||||||
Quadrature with Index Output Channel—20mA Output Current | |||||||||||||||||
Up and Down | A, B, Z | 600 | 2X, 4X | 8,000 | 4.75-28V DC | 3.175" | 3 1/4" | 3/8" | 1 1/16" | 2 1/2" | 2 1/2" | 4 | 2.06" | 7/32" | CE Marked | 00000000 | 000000000 |
Up and Down | A, B, Z | 3,600 | 2X, 4X | 8,000 | 4.75-28V DC | 3.175" | 3 1/4" | 3/8" | 1 1/16" | 2 1/2" | 2 1/2" | 4 | 2.06" | 7/32" | CE Marked | 00000000 | 00000000 |
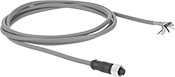
Lg. | Each | |
32 3/4 " | 00000000 | 0000000 |
Rotary Motion Position-Measuring Transmitters
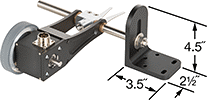
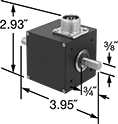
Provide motion feedback to counters, controllers, and motor drives for automated motion control and measurement applications. Also known as encoders, transmitters convert rotary motion to an electrical signal so you can operate your system based on distance, direction, and speed of travel. Transmitters have Pull-Up Resistor output.
Use a flexible shaft coupling (not included) to connect the transmitter shaft to a drive shaft.
Mount a wheel (not included) to use transmitters to measure lengths.
Use cables (not included) to connect transmitters to counters and controllers.
Transmitters with a quadrature output channel must be used with a controller that has quadrature detection to get a 4X resolution increase.
Mount. Plate | Mount. Holes | ||||||||||||||
---|---|---|---|---|---|---|---|---|---|---|---|---|---|---|---|
For Counter Function | Output Channels | Resolution Increase | For Max. Shaft Speed, rpm | Input Voltage | Output Current, mA | Shaft Coupling Required | Body Material | Shaft Material | Lg. | Wd. | Ctr.-to-Ctr. | Thread Size | Choose a Resolution | Each | |
Single Output Channel | |||||||||||||||
Up | A | 2X | 6,000 | 5V DC-28V DC | 250 | Yes | Aluminum | Stainless Steel | 2 1/4" | 2 1/4" | 1.41" | 6-32 | 00000000 | 0000000 | |
Quadrature Output Channel | |||||||||||||||
Up and Down | A, B | 2X, 4X | 6,000 | 5V DC-28V DC | 250 | Yes | Aluminum | Stainless Steel | 2 1/4" | 2 1/4" | 1.41" | 6-32 | 00000000 | 000000 |
Rotary Motion Position-Measuring Transmitter Kits
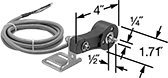
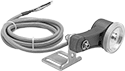
In addition to a transmitter, these kits include a 6 1/2-ft. cable and a mounting bracket. Also known as encoders, transmitters convert motion to an electrical signal to indicate distance, direction, and speed in process control and metering applications. These kits are commonly used to monitor the position or velocity of rotating equipment. You can also mount a wheel (not included) to measure distance in linear applications. Transmitters must be used with a controller that has quadrature detection to get a 4X resolution increase. Output channel Z is also known as an index channel.
Use a flexible shaft coupling (not included) to connect the transmitter shaft to a drive shaft.
For Counter Function | Output Channels | Resolution Increase | For Max. Shaft Speed, rpm | Input Voltage | Output Current, mA | Resistor Included | Body Material | Shaft Material | Fasteners Included | Fasteners Required | For Mounting Screw Size | Choose a Resolution | Each | |
Quadrature with Index Output Channel | ||||||||||||||
---|---|---|---|---|---|---|---|---|---|---|---|---|---|---|
Up and Down | A, B, Z | 2X, 4X | 6,000 | 5V DC-28V DC | 20 | No | Plastic | Stainless Steel | No | Yes | 1/4" | 00000000 | 0000000 |
6" Circumference Polyurethane Wheel (1.91" Dia. × 1/4" Wd.) | 00000000 | Each | 000000 |
Stepper Motors with Integrated Motion Control
With a built-in controller and driver, these stepper motors come ready to program and operate. Connect them to a computer and use the free downloadable software to set them up. After that, the controller can store and run programs on its own. The controller communicates to the driver which directs the motor’s shaft to move in small, equal increments. When the shaft stops, it holds its position even when a counteracting force is applied to the load. All are bipolar hybrid stepper motors, which deliver greater torque, precision, and efficiency than other types of stepper motors.
When relative positioning is critical, such as coordinating motion in a multi-axis system, choose a motor with an encoder. The encoder monitors the position of the shaft and reports back to the controller.
Holding torque is the force needed to move the shaft out of position when it is stationary. When the shaft is in motion, torque generally decreases as speed increases. Use a torque-speed curve to confirm which motor will work for your application. Click on a part number and select “Product Detail” to view the curve for a motor.
You can adjust the step resolution down to 1/256 of a full step, which translates to 51,200 microsteps per revolution. Increasing the number of steps directs an even more precise position and reduces the step-step-step motion to mimic a smooth, continuous rotation. The higher the number of step resolution settings, the greater the flexibility you have for determining the size of the motor’s step.
For technical drawings and 3-D models, click on a part number.
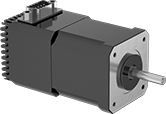
O'all | Shaft | |||||||||||||||
---|---|---|---|---|---|---|---|---|---|---|---|---|---|---|---|---|
Max. Holding Torque, in.-oz. | Max. Speed, rpm | Current per Phase, A | DC Voltage | Full Step Increment | Step Resolution | No. of Inputs/Outputs | Lg. | Wd. | Ht. | Dia. | Lg. | Center to Base | Type | Temp. Range, °F | Each | |
Motors/Controllers/Drivers/Encoders | ||||||||||||||||
NEMA 17 | ||||||||||||||||
31 | 3,000 | 0.1-2.2 | 12-48 | 1.8° | 1 to 1/256 | 1 Analog Input, 3 Digital Inputs, 1 Digital Output | 3.7" | 1.7" | 3" | 5mm | 22mm | 0.84" | D-Profile | 35° to 100° | 00000000 | 0000000 |
54 | 3,000 | 0.1-2.2 | 12-48 | 1.8° | 1 to 1/256 | 1 Analog Input, 3 Digital Inputs, 1 Digital Output | 3.9" | 1.7" | 3" | 5mm | 22mm | 0.84" | D-Profile | 35° to 100° | 00000000 | 000000 |
68 | 3,000 | 0.1-2.2 | 12-48 | 1.8° | 1 to 1/256 | 1 Analog Input, 3 Digital Inputs, 1 Digital Output | 4.2" | 1.7" | 3" | 5mm | 22mm | 0.84" | D-Profile | 35° to 100° | 00000000 | 000000 |
NEMA 23 | ||||||||||||||||
100.5 | 2,475 | 0.3-3 | 12-40 | 1.8° | 1; 1/2; 1/4; 1/8; 1/16; 1/32; 1/64; 1/128; 1/256 | 4 Digital Inputs/Outputs | 3.8" | 2.3" | 2.3" | 1/4" | 3/4" | 1.13" | D-Profile | 0° to 120° | 00000000 | 000000 |
182.5 | 2,000 | 0.3-3 | 12-40 | 1.8° | 1; 1/2; 1/4; 1/8; 1/16; 1/32; 1/64; 1/128; 1/256 | 4 Digital Inputs/Outputs | 4.3" | 2.3" | 2.3" | 1/4" | 3/4" | 1.13" | D-Profile | 0° to 120° | 00000000 | 000000 |
294.5 | 820 | 0.3-3 | 12-40 | 1.8° | 1; 1/2; 1/4; 1/8; 1/16; 1/32; 1/64; 1/128; 1/256 | 4 Digital Inputs/Outputs | 5.1" | 2.3" | 2.3" | 1/4" | 3/4" | 1.13" | D-Profile | 0° to 120° | 00000000 | 000000 |
NEMA 24 | ||||||||||||||||
340 | 2,400 | 3-5 | 12-70 | 1.8° | 1 to 1/256 | 1 Analog Input, 4 Digital Inputs/Outputs | 4.9" | 2.4" | 3.8" | 8mm | 21mm | 1.18" | D-Profile | 35° to 100° | 00000000 | 000000 |
Stepper Motors with Encoder
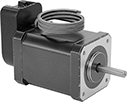
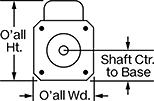
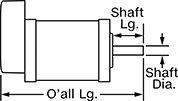
To improve positioning accuracy, these stepper motors have a built-in encoder that monitors the real-time speed and position of the shaft. It sends that data to a controller (not included), which adjusts or stops the shaft if it isn’t in the right place. This makes them useful when relative positioning is critical, such as when coordinating motion between two motors. Stepper motors are good for precise, repetitive movements. Similar to the hands of a clock, their shaft turns in small, equal increments for smooth motion. When the shaft stops, it holds its position even when a counteracting force is applied to the load. All are bipolar hybrid stepper motors, so the current can flow in both directions. This helps them deliver higher torque, precision, and efficiency than unipolar stepper motors.
Holding torque is the force needed to move the shaft out of position when it’s stationary. When the shaft is in motion, torque generally decreases as speed increases. Use a torque-speed curve to confirm which motor will work for your application. Click on a part number and select “Product Detail” to view the curve for a motor.
Full step increment is the rotation of the shaft from one position to the next. A smaller full step increment means the rotor has more teeth, producing smoother and more precise motion. 1.8° is considered standard.
All motors require a controller and driver (not included).
For technical drawings and 3-D models, click on a part number.
O'all | Shaft | ||||||||||||||||
---|---|---|---|---|---|---|---|---|---|---|---|---|---|---|---|---|---|
Max. Holding Torque, in.-oz. | Max. Speed, rpm | Max. Current per Phase, A | Full Step Increment | Encoder Positioning Type | No. of Counts per Revolution | No. of Wire Leads | Lg. | Wd. | Ht. | Dia. | Lg. | Center to Base | Type | No. of Shafts | Temp. Range, °F | Each | |
NEMA 17 | |||||||||||||||||
26.9 | 1,500 | 0.67 | 1.8° | Incremental | 1,000 | 4 | 2.6" | 2.3" | 1.7" | 5mm | 22mm | 0.84" | D-Profile | 2 | 0° to 120° | 00000000 | 0000000 |
39 | 900 | 0.62 | 1.8° | Incremental | 1,000 | 4 | 2.8" | 2.3" | 1.7" | 5mm | 22mm | 0.84" | Solid | 2 | 0° to 120° | 00000000 | 000000 |
64 | 750 | 0.7 | 1.8° | Incremental | 1,000 | 4 | 3" | 2.3" | 1.7" | 5mm | 22mm | 0.84" | Solid | 2 | 0° to 120° | 00000000 | 000000 |
70.8 | 3,000 | 2 | 1.8° | Incremental | 1,000 | 4 | 3.2" | 2.3" | 1.7" | 5mm | 22mm | 0.84" | D-Profile | 2 | 0° to 120° | 00000000 | 000000 |
83.5 | 825 | 1.05 | 1.8° | Incremental | 1,000 | 4 | 3.5" | 2.3" | 1.7" | 5mm | 22mm | 0.84" | D-Profile | 2 | 0° to 120° | 00000000 | 000000 |
124.6 | 1,400 | 2 | 1.8° | Incremental | 1,000 | 4 | 3.9" | 2.3" | 1.7" | 5mm | 22mm | 0.84" | D-Profile | 2 | 0° to 120° | 00000000 | 000000 |
130.2 | 950 | 2 | 1.8° | Incremental | 1,000 | 4 | 3.9" | 2.3" | 1.7" | 5mm | 22mm | 0.84" | Solid | 2 | 0° to 120° | 00000000 | 000000 |
NEMA 23 | |||||||||||||||||
181 | 600 | 2.8 | 1.8° | Incremental | 1,000 | 4 | 3.7" | 2.6" | 2.3" | 1/4" | 3/4" | 1.13" | D-Profile | 2 | 0° to 120° | 00000000 | 000000 |
237 | 525 | 4 | 1.8° | Incremental | 1,000 | 4 | 4.6" | 2.6" | 2.3" | 1/4" | 3/4" | 1.13" | D-Profile | 2 | 0° to 120° | 00000000 | 000000 |
355 | 900 | 6 | 1.8° | Incremental | 1,000 | 4 | 4.9" | 2.6" | 2.3" | 1/4" | 3/4" | 1.13" | D-Profile | 2 | 0° to 120° | 00000000 | 000000 |
467.3 | 300 | 2 | 1.8° | Incremental | 1,000 | 4 | 4.5" | 2.5" | 2.3" | 1/4" | 3/4" | 1.11" | D-Profile | 2 | 0° to 120° | 00000000 | 000000 |
600.4 | 1,300 | 6.5 | 1.8° | Incremental | 1,000 | 4 | 4.9" | 2.6" | 2.3" | 1/4" | 3/4" | 1.13" | D-Profile | 2 | 0° to 120° | 00000000 | 000000 |
Potentiometers



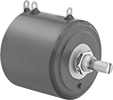

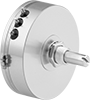

Vary electrical flow to control speed, volume, and light intensity. The number of turns affects the resolution—the higher the number, the better the control. Also known as variable output switches. A knob is required (not included).
Style A potentiometers are also known as gangable potentiometers. They can be linked to each other, so you can control multiple potentiometers from a single source.
IP65 rated switches are protected against washdowns.
Switches with ball bearings have a smoother rotation and a longer service life than other potentiometers.



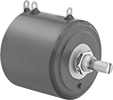
Shaft | ||||||||||||||
---|---|---|---|---|---|---|---|---|---|---|---|---|---|---|
No. of Turns | Wattage | For Panel Cutout Dia. | Dp. Behind Panel | Dia. | Dia. | Lg. | Housing Material | Wire Connection Type | No. of Terminals | Environmental Rating | Choose a Max. Resistance, kilohms | Each | ||
A | 3 | 1 W @ 224 V AC | 7/16" | 3/4" | 7/8" | 1/4" | 1/2" | Plastic | Tab Terminals | 3 | IP40 | 0000000 | 000000 | |
B | 10 | 2 W @ 325 V AC | 7/16" | 1" | 7/8" | 1/4" | 1/2" | Plastic | Tab Terminals | 3 | IP65 | 0000000 | 00000 | |
B | 10 | 2 W @ 447 V AC | 7/16" | 3/4" | 7/8" | 1/4" | 1/2" | Plastic | Tab Terminals | 3 | IP40 | 0000000 | 00000 | |
B | 10 | 2 W @ 450 V AC | 7/16" | 3/4" | 7/8" | 1/4" | 1/2" | Plastic | Tab Terminals | 3 | IP40 | 0000000 | 00000 | |
B | 5 | 1.5 W @ 273 V AC | 7/16" | 3/4" | 7/8" | 1/4" | 1/2" | Plastic | Tab Terminals | 3 | IP40 | 0000000 | 00000 | |
C | 1 | 1 W @ 300 V AC | 7/16" | 7/16" | 7/8" | 1/4" | 1/2" | Plastic | Tab Terminals | 3 | IP40 | 0000000 | 00000 | |
D | 10 | 5 W @ 1,000 V AC | 7/16" | 1 3/4" | 1 13/16" | 1/4" | 1/2" | Plastic | Tab Terminals | 3 | IP40 | 0000000 | 000000 |

Digital Potentiometers
More precise than analog potentiometers, these have a three-digit display that is easy to read. Also known as variable output switches, they vary electrical flow to control speed, volume, and light intensity.
Linear Motion Potentiometers
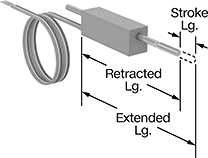
Pair these potentiometers with a controller to monitor the position of moving parts or send instructions to an electrical system. They have a rod that slides back and forth against an internal resistor, which increases or decreases the voltage flowing out to your controller. To monitor the position of a moving part, such as a robotic component, connect it to the rod. As the part moves, it pushes the rod back and forth, which allows the controller to observe and report the part’s exact position. To use these potentiometers as part of a controls system, connect them to a volume slider or other manual control. When you move the slider, the controller converts its position into instructions for electrical equipment, such as adjusting volume levels. These potentiometers are also called variable output switches.
For technical drawings and 3-D models, click on a part number.
Lg. | Rod | ||||||||||||
---|---|---|---|---|---|---|---|---|---|---|---|---|---|
Stroke | Retracted | Extended | Wattage | Wd. | Ht. | Dia. | Thread Size | Material | Housing Material | Wire Connection Type | Environmental Rating | Each | |
5 kilohms Max. Resistance | |||||||||||||
5/32" | 1.59" | 1.74" | 0.125 W @ 200 V DC | 1/4" | 9/32" | 1/16" | 0-80 | 303 Stainless Steel | Plastic | Wire Leads | IP45 | 0000000 | 000000 |
1/4" | 1.59" | 1.84" | 0.125 W @ 200 V DC | 1/4" | 9/32" | 1/16" | 0-80 | 303 Stainless Steel | Plastic | Wire Leads | IP45 | 0000000 | 00000 |
1/2" | 2.22" | 2.72" | 0.25 W @ 300 V DC | 9/32" | 11/32" | 3/32" | 2-56 | 303 Stainless Steel | Plastic | Wire Leads | IP45 | 0000000 | 00000 |
10 kilohms Max. Resistance | |||||||||||||
5/32" | 1.59" | 1.74" | 0.125 W @ 200 V DC | 1/4" | 9/32" | 1/16" | 0-80 | 303 Stainless Steel | Plastic | Wire Leads | IP45 | 0000000 | 00000 |
1/4" | 1.59" | 1.84" | 0.125 W @ 200 V DC | 1/4" | 9/32" | 1/16" | 0-80 | 303 Stainless Steel | Plastic | Wire Leads | IP45 | 0000000 | 00000 |
1/2" | 2.22" | 2.72" | 0.25 W @ 300 V DC | 9/32" | 11/32" | 3/32" | 2-56 | 303 Stainless Steel | Plastic | Wire Leads | IP45 | 0000000 | 00000 |
Harsh Environment Potentiometers
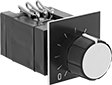

Rated NEMA 13, these potentiometers protect against debris and splashing oil and coolant. Also known as variable output switches, they vary electrical flow to control speed, volume, and light intensity.
NEMA 4X rated potentiometers withstand weather, washdowns, and corrosion.
NEMA 6 potentiometers seal out water from temporary submersion as well as weather and washdowns.
Actuator | ||||||||||||
---|---|---|---|---|---|---|---|---|---|---|---|---|
Wattage @ Voltage | Max. Voltage | For Panel Cutout Dia. | Dp. Behind Panel | No. of Turns | Dia. | Material | Wire Connection Type | Environmental Rating | Specifications Met | Choose a Max. Resistance | Each | |
Plastic | ||||||||||||
2 W @ 120 V AC/ 2 W @ 24 V DC | 500V AC/500V DC | 7/8" (22 mm) | 2 1/4" | 1 | 1 1/8" | Plastic | Screw Terminals | NEMA 4X, NEMA 13, IP65 | UL Listed, C-UL Listed, CE Marked | 000000 | 000000 | |
2 W @ 120 V AC/ 2 W @ 24 V DC | 500V AC/500V DC | 1 3/16" (30 mm) | 2 1/8" | 1 | 1 1/8" | Plastic | Screw Terminals | NEMA 4X, NEMA 13, IP65 | UL Listed, C-UL Listed, CE Marked | 0000000 | 00000 | |
Metal | ||||||||||||
2 W @ 300 V DC 2 W @ 300 V AC | 300V AC/300V DC | 1 3/16" (30 mm) | 1 15/16" | 1 | 1 1/8" | Plastic | Screw Terminals | NEMA 6, NEMA 13, IP65 | UL Listed, C-UL Listed, CSA Certified, CE Marked | 0000000 | 000000 |
Variable-Speed Foot Switches
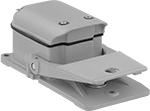
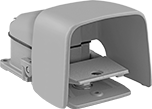
When the pedal is pressed, the built-in potentiometer adjusts the resistance to vary the speed for motor drives. These switches can be wired to either increase or decrease the current when actuated. All are rated NEMA 4 and 13 for protection from washdowns and oil/coolant spraying.
For technical drawings and 3-D models, click on a part number.
Mounting | ||||||||||||||
---|---|---|---|---|---|---|---|---|---|---|---|---|---|---|
No. of Circuits Controlled | Switch Starting Position | Switch Action | Industry Designation | Switching Current @ Voltage | No. of Terminals | Quick-Disconnect Tab Wd. | Conduit Trade Size | Environmental Rating | Fasteners Included | No. of Holes | Hole Dia. | Choose a Max. Resistance | Each | |
With Quick-Disconnect Terminals | ||||||||||||||
Iron Housing | ||||||||||||||
1 | 1 Off (Normally Open) or 1 On (Normally Closed) | Springs Back (Momentary) | SPDT | 15 A @ 125 V AC/250 V AC | 3 | 0.187" | 3/4 | IP56 NEMA 4 NEMA 13 | No | 3 | 0.31" | 0000000 | 0000000 | |
Iron Housing with Aluminum Guard | ||||||||||||||
1 | 1 Off (Normally Open) or 1 On (Normally Closed) | Springs Back (Momentary) | SPDT | 15 A @ 125 V AC/250 V AC | 3 | 0.187" | 3/4 | IP56 NEMA 4 NEMA 13 | No | 3 | 0.31" | 0000000 | 000000 |