Tapered Heat-Set Inserts for Plastic
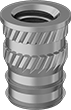
The tapered shape makes it easier to guide these inserts into a hole during installation. Use a drill bit to create a straight hole, then taper the top half. Heat inserts with a soldering tip so that they melt the plastic when installed. As the plastic cools, it solidifies around the knurls and ridges on the insert for excellent resistance to both torque and pull-out.
Made with lead, brass inserts are stronger than aluminum and other brass alloys but not as strong as 18-8 stainless steel inserts. They have good corrosion resistance.
18-8 stainless steel inserts are stronger than brass and aluminum inserts, have excellent corrosion resistance, and are lead-free. Since they’re lead-free, they can be safely recycled.
Inserts that meet ASTM standards comply with specifications for material quality.
Heat-Set Inserts for Plastic
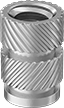
Install these inserts into plastic parts to create a secure base for fasteners. Also known as Chevron and headed inserts, they are often used to strengthen mounting holes on brittle plastics, such as on 3D printed parts. Unlike plastic threads, which wear down with repeated use, these threads hold their shape over a long life. Press inserts into straight holes that have been drilled, printed, or molded into plastic parts, then heat them with a soldering tip to melt the surrounding plastic. As the plastic cools, it fuses to the sharp, diagonal ridges around the inserts, which withstand torque and prevent the inserts from being pulled out. The interior is fully threaded, so you can access the threads from both sides of a through-hole.
Made with lead, brass inserts are stronger than aluminum and other brass alloys but not as strong as 18-8 stainless steel inserts. They have good corrosion resistance.