About Shaft Couplings
More
Stepper Motors
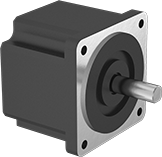
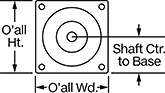
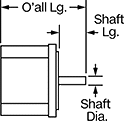
These stepper motors are good for precise, repetitive movements, such as those made by the head of a 3D printer. Similar to the hands of a clock, their shaft turns in small, equal increments. When the shaft stops, it holds its position even when a counteracting force is applied to the load. You can control the position of the load without having to configure encoders or sensors. All are bipolar hybrid stepper motors, so the current can flow in both directions. This helps them deliver higher torque, precision, and efficiency than unipolar stepper motors.
Motors with 8 wire leads can be connected to a driver in two different ways, so you can choose between more speed or more torque. Depending on your application, you could configure the motor for high torque at low speeds or for low torque at high speeds.
Holding torque is the force needed to move the shaft out of position when it is stationary. When the shaft is in motion, torque generally decreases as speed increases. Use a torque-speed curve to confirm which motor will work for your application. Click on a part number and select “Product Detail” to view the curve for a motor.
Full step increment is the rotation of the shaft from one position to the next. A smaller full step increment means the rotor has more teeth, producing smoother and more precise motion. 1.8° is considered standard.
All motors require a controller and driver (not included).
For technical drawings and 3-D models, click on a part number.
O'all | Shaft | ||||||||||||||
---|---|---|---|---|---|---|---|---|---|---|---|---|---|---|---|
Max. Holding Torque, in.-oz. | Max. Speed, rpm | Max. Current per Phase, A | Full Step Increment | No. of Wire Leads | Lg. | Wd. | Ht. | Dia. | Lg. | Center to Base | Type | No. of Shafts | Temp. Range, °F | Each | |
Square Body | |||||||||||||||
NEMA 34 | |||||||||||||||
1,700 | 1,500 | 10 | 1.8° | 8 | 7.4" | 3.4" | 3.4" | 5/8" | 1 1/4" | 1.69" | Keyed | 1 | 0° to 120° | 00000000 | 0000000 |
2,124.1 | 360 | 5 | 1.8° | 4 | 7.4" | 3.4" | 3.4" | 5/8" | 1" | 1.7" | Keyed | 1 | 0° to 120° | 00000000 | 000000 |
Stepper Motors with Integrated Motion Control
With a built-in controller and driver, these stepper motors come ready to program and operate. Connect them to a computer and use the free downloadable software to set them up. After that, the controller can store and run programs on its own. The controller communicates to the driver which directs the motor’s shaft to move in small, equal increments. When the shaft stops, it holds its position even when a counteracting force is applied to the load. All are bipolar hybrid stepper motors, which deliver greater torque, precision, and efficiency than other types of stepper motors.
Holding torque is the force needed to move the shaft out of position when it is stationary. When the shaft is in motion, torque generally decreases as speed increases. Use a torque-speed curve to confirm which motor will work for your application. Click on a part number and select “Product Detail” to view the curve for a motor.
You can adjust the step resolution down to 1/256 of a full step, which translates to 51,200 microsteps per revolution. Increasing the number of steps directs an even more precise position and reduces the step-step-step motion to mimic a smooth, continuous rotation. The higher the number of step resolution settings, the greater the flexibility you have for determining the size of the motor’s step.
For technical drawings and 3-D models, click on a part number.
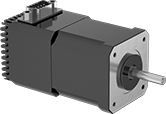
O'all | Shaft | |||||||||||||||
---|---|---|---|---|---|---|---|---|---|---|---|---|---|---|---|---|
Max. Holding Torque, in.-oz. | Max. Speed, rpm | Current per Phase, A | DC Voltage | Full Step Increment | Step Resolution | No. of Inputs/Outputs | Lg. | Wd. | Ht. | Dia. | Lg. | Center to Base | Type | Temp. Range, °F | Each | |
Motors/Controllers/Drivers | ||||||||||||||||
NEMA 34 | ||||||||||||||||
1,700 | 1,800 | 0.5-5 | 20-80 | 1.8° | 1/10 | 2 Digital Inputs, 1 Digital Output | 9.6" | 3.5" | 3.5" | 5/8" | 1 1/4" | 1.76" | Keyed | 0° to 120° | 00000000 | 0000000 |
Stepper Motors with Driver
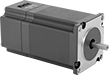
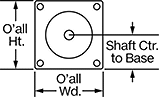
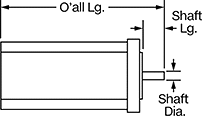
Reduce the size and complexity of your stepper motor setup—these motors have a driver built in, so you don’t need to run cable to a standalone driver. The driver delivers power to the motor based on signals from a PLC, pulse generator, or other controller. These motors are good for precise, repetitive movements, such as those made by the head of a 3D printer. Similar to the hands of a clock, their shaft turns in small, equal increments for smooth motion. When the shaft stops, it holds its position even when a counteracting force is applied to the load. You can control the position of the load without having to configure encoders or sensors. All are bipolar hybrid stepper motors, so the current can flow in both directions. This helps them deliver higher torque, precision, and efficiency than unipolar stepper motors.
Holding torque is the force needed to move the shaft out of position when it’s stationary. When the shaft is in motion, torque generally decreases as speed increases. Use a torque-speed curve to confirm which motor will work for your application. Click on a part number and select “Product Detail” to view the curve for a motor.
Full step increment is the rotation of the shaft from one position to the next. A smaller full step increment means the rotor has more teeth, producing smoother and more precise motion. 1.8° is considered standard.
Reduce the step resolution to break a full step into smaller steps for smoother motion. For example, setting a 1/256 step resolution on your driver divides one full step into 256 smaller steps.
For technical drawings and 3-D models, click on a part number.
O'all | Shaft | |||||||||||||||
---|---|---|---|---|---|---|---|---|---|---|---|---|---|---|---|---|
Max. Holding Torque, in.-oz. | Max. Speed, rpm | Current per Phase, A | DC Voltage | Full Step Increment | Step Resolution | Polarity | Lg. | Wd. | Ht. | Dia. | Lg. | Center to Base | Type | Temp. Range, °F | Each | |
NEMA 34 | ||||||||||||||||
1,700 | 1,800 | 0.5-5 | 20-80 | 1.8° | 1 | Bipolar | 9.6" | 3.5" | 3.5" | 5/8" | 1 3/16" | 1.76" | Keyed | 0° to 120° | 00000000 | 0000000 |
Clamping Precision Flexible Shaft Couplings
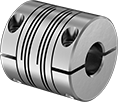
Designed to grip evenly around your shaft, these couplings provide more holding power than set screw couplings without marring the shaft. Tighten the clamping screws to secure.
Spiral couplings have long cuts in their body for flexibility to handle parallel, axial, and angular misalignment better than parallel couplings. However, they’re not as rigid. Often used for light duty encoder and stepper drive applications, they allow zero backlash (no play) and never need lubrication. They’re also known as helical beam couplings.
Aluminum couplings are lightweight with good corrosion resistance. Stainless steel couplings offer excellent corrosion resistance.
For technical drawings and 3-D models, click on a part number.
Misalignment Capability | ||||||||||
---|---|---|---|---|---|---|---|---|---|---|
For Shaft Dia. | Overall Lg. | OD | Max. Speed, rpm | Max. Torque, in.-lbs. | Parallel | Angular | Axial | For Motion Type | Each | |
Spiral Cut | ||||||||||
7075 Aluminum | ||||||||||
5/8" × 1/4" | 2 3/8" | 1 1/2" | 10,000 | 155 | 0.015" | 5° | 0.01" | Forward/Reverse, Start/Stop | 00000000 | 0000000 |
5/8" × 5/16" | 2 3/8" | 1 1/2" | 10,000 | 155 | 0.015" | 5° | 0.01" | Forward/Reverse, Start/Stop | 00000000 | 000000 |
5/8" × 5/16" | 2 1/2" | 1 5/8" | 10,000 | 215 | 0.015" | 5° | 0.01" | Forward/Reverse, Start/Stop | 00000000 | 000000 |
5/8" × 3/8" | 2 3/8" | 1 1/2" | 10,000 | 155 | 0.015" | 5° | 0.01" | Forward/Reverse, Start/Stop | 00000000 | 000000 |
5/8" × 3/8" | 2 1/2" | 1 5/8" | 10,000 | 215 | 0.015" | 5° | 0.01" | Forward/Reverse, Start/Stop | 00000000 | 000000 |
5/8" × 3/8" | 2 3/4" | 1 3/4" | 10,000 | 250 | 0.015" | 5° | 0.01" | Forward/Reverse, Start/Stop | 00000000 | 000000 |
5/8" × 1/2" | 2 3/8" | 1 1/2" | 10,000 | 155 | 0.015" | 5° | 0.01" | Forward/Reverse, Start/Stop | 00000000 | 000000 |
5/8" × 1/2" | 2 1/2" | 1 5/8" | 10,000 | 215 | 0.015" | 5° | 0.01" | Forward/Reverse, Start/Stop | 00000000 | 000000 |
5/8" × 1/2" | 2 3/4" | 1 3/4" | 10,000 | 250 | 0.015" | 5° | 0.01" | Forward/Reverse, Start/Stop | 00000000 | 000000 |
5/8" × 5/8" | 2 3/8" | 1 1/2" | 10,000 | 155 | 0.015" | 5° | 0.01" | Forward/Reverse, Start/Stop | 00000000 | 000000 |
5/8" × 5/8" | 2 1/2" | 1 5/8" | 10,000 | 215 | 0.015" | 5° | 0.01" | Forward/Reverse, Start/Stop | 00000000 | 000000 |
5/8" × 5/8" | 2 3/4" | 1 3/4" | 10,000 | 250 | 0.015" | 5° | 0.01" | Forward/Reverse, Start/Stop | 00000000 | 000000 |
5/8" × 3/4" | 2 3/4" | 1 3/4" | 10,000 | 250 | 0.015" | 5° | 0.01" | Forward/Reverse, Start/Stop | 00000000 | 000000 |
8mm × 5/8" | 38mm | 30mm | 6,000 | 58 | 0.38mm | 3° | 0.25mm | Forward/Reverse, Start/Stop | 0000000 | 000000 |
9mm × 5/8" | 38mm | 30mm | 6,000 | 58 | 0.38mm | 3° | 0.25mm | Forward/Reverse, Start/Stop | 0000000 | 000000 |
10mm × 5/8" | 38mm | 30mm | 6,000 | 58 | 0.38mm | 3° | 0.25mm | Forward/Reverse, Start/Stop | 0000000 | 000000 |
10mm × 5/8" | 57mm | 38mm | 6,000 | 80 | 0.762mm | 3° | 0.38mm | Forward/Reverse, Start/Stop | 0000000 | 000000 |
11mm × 5/8" | 38mm | 30mm | 6,000 | 58 | 0.38mm | 3° | 0.25mm | Forward/Reverse, Start/Stop | 0000000 | 000000 |
12mm × 5/8" | 38mm | 30mm | 6,000 | 58 | 0.38mm | 3° | 0.25mm | Forward/Reverse, Start/Stop | 0000000 | 000000 |
12mm × 5/8" | 57mm | 38mm | 6,000 | 80 | 0.762mm | 3° | 0.38mm | Forward/Reverse, Start/Stop | 0000000 | 000000 |
14mm × 5/8" | 57mm | 38mm | 6,000 | 80 | 0.762mm | 3° | 0.38mm | Forward/Reverse, Start/Stop | 0000000 | 000000 |
15mm × 5/8" | 57mm | 38mm | 6,000 | 80 | 0.762mm | 3° | 0.38mm | Forward/Reverse, Start/Stop | 0000000 | 000000 |
16mm × 5/8" | 57mm | 38mm | 6,000 | 80 | 0.762mm | 3° | 0.38mm | Forward/Reverse, Start/Stop | 0000000 | 000000 |
20mm × 5/8" | 57mm | 38mm | 6,000 | 80 | 0.762mm | 3° | 0.38mm | Forward/Reverse, Start/Stop | 0000000 | 000000 |
303 Stainless Steel | ||||||||||
5/8" × 3/8" | 2 1/4" | 1 1/2" | 6,000 | 145 | 0.03" | 3° | 0.015" | Forward/Reverse, Start/Stop | 0000000 | 000000 |
5/8" × 1/2" | 2 1/4" | 1 1/2" | 6,000 | 145 | 0.03" | 3° | 0.015" | Forward/Reverse, Start/Stop | 0000000 | 000000 |
5/8" × 5/8" | 2 1/4" | 1 1/2" | 6,000 | 145 | 0.03" | 3° | 0.015" | Forward/Reverse, Start/Stop | 0000000 | 000000 |
3/4" × 5/8" | 2 1/4" | 1 1/2" | 6,000 | 145 | 0.03" | 3° | 0.015" | Forward/Reverse, Start/Stop | 0000000 | 000000 |