Stepper Motors
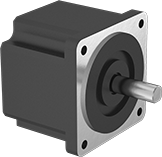
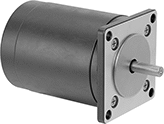
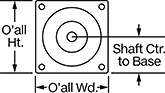
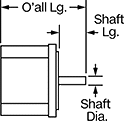
These stepper motors are good for precise, repetitive movements, such as those made by the head of a 3D printer. Similar to the hands of a clock, their shaft turns in small, equal increments. When the shaft stops, it holds its position even when a counteracting force is applied to the load. You can control the position of the load without having to configure encoders or sensors. All are bipolar hybrid stepper motors, so the current can flow in both directions. This helps them deliver higher torque, precision, and efficiency than unipolar stepper motors.
Holding torque is the force needed to move the shaft out of position when it is stationary. When the shaft is in motion, torque generally decreases as speed increases. Use a torque-speed curve to confirm which motor will work for your application. Click on a part number and select “Product Detail” to view the curve for a motor.
Full step increment is the rotation of the shaft from one position to the next. A smaller full step increment means the rotor has more teeth, producing smoother and more precise motion. 1.8° is considered standard.
All motors require a controller and driver (not included).
For technical drawings and 3-D models, click on a part number.
O'all | Shaft | ||||||||||||||
---|---|---|---|---|---|---|---|---|---|---|---|---|---|---|---|
Max. Holding Torque, in.-oz. | Max. Speed, rpm | Max. Current per Phase, A | Full Step Increment | No. of Wire Leads | Lg. | Wd. | Ht. | Dia. | Lg. | Center to Base | Type | No. of Shafts | Temp. Range, °F | Each | |
Square Body | |||||||||||||||
NEMA 14 | |||||||||||||||
7.5 | 3,300 | 0.45 | 1.8° | 4 | 1.6" | 1.4" | 1.4" | 5mm | 13.5mm | 0.7" | Solid | 1 | 0° to 120° | 0000000 | 000000 |
20 | 1,800 | 0.8 | 1.8° | 4 | 1.9" | 1.4" | 1.4" | 5mm | 13.5mm | 0.7" | Solid | 1 | 0° to 120° | 0000000 | 00000 |
56.6 | 3,000 | 2 | 1.8° | 4 | 3.1" | 1.4" | 1.4" | 5mm | 22mm | 0.7" | D-Profile | 1 | 0° to 120° | 00000000 | 000000 |
Round Body | |||||||||||||||
NEMA 14 | |||||||||||||||
15.5 | 825 | 0.6 | 0.9° | 4 | 1.6" | 1.4" | 1.4" | 5mm | 18.2mm | 0.7" | D-Profile | 1 | 0° to 120° | 00000000 | 00000 |
15.5 | 1,475 | 1.2 | 0.9° | 4 | 1.6" | 1.4" | 1.4" | 5mm | 18.2mm | 0.7" | D-Profile | 1 | 0° to 120° | 00000000 | 00000 |
Stepper Motors with Linear Actuation
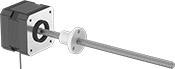
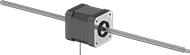
Instead of a shaft, these stepper motors have a lead screw that converts rotational motion to linear motion. Moving in increments smaller than the thickness of a sheet of paper, they're ideal for applications that require fine motion control, such as positioning electrical components on a circuit board. They move in equal steps and hold their position when stationary, so they do not require encoders, sensors, or other position feedback devices. The lead screw is built into the motor, so there are fewer points of failure than systems that use a shaft coupling to connect the lead screw. All are bipolar hybrid stepper motors, which deliver greater torque, precision, and efficiency than other types of stepper motors.
External lead screw stepper motors work similar to a traditional linear motion system; attach the load to the flanged nut, which travels back and forth along the lead screw.
Pass-through lead screw stepper motors give you the most design versatility because there are two ways to move your load: on the motor body or on the ends of the lead screw. The motor moves when the lead screw is fixed or the lead screw moves when the motor body is fixed.
Travel distance per full step determines the control you have over the motor’s positioning. The smaller the measurement, the finer positioning control you have, but the more steps it will take to go the same distance.
Dynamic load capacity is the maximum load a motor can move. If you increase the speed, the dynamic load capacity decreases. Click on a part number and select "Product Detail" to view the load-speed chart and confirm the motor will work for your application.
All motors require a driver and controller (not included).
For technical drawings and 3-D models, click on a part number.
O'all | |||||||||||||||
---|---|---|---|---|---|---|---|---|---|---|---|---|---|---|---|
Travel Distance per Full Step | Travel Lg. | Dynamic Load Capacity, lbs. | Max. Speed, in./sec. | Max. Current per Phase | Full Step Increment | Polarity | No. of Wire Leads | Lg. | Wd. | Ht. | Lead Screw Lg. | Thread Size | Temp. Range, °F | Each | |
External Lead Screw | |||||||||||||||
NEMA 14 | |||||||||||||||
0.00024" | 5.2" | 50 | 0.3 | 1.2A | 1.8° | Bipolar | 4 | 7.4" | 1.4" | 1.4" | 6" | 7/32"-48 | 35° to 130° | 0000000 | 0000000 |
0.00024" | 11.2" | 50 | 0.3 | 1.2A | 1.8° | Bipolar | 4 | 13.4" | 1.4" | 1.4" | 12" | 7/32"-48 | 35° to 130° | 0000000 | 000000 |
0.00125" | 3.2" | 28 | 2 | 2A | 1.8° | Bipolar | 4 | 5.7" | 1.4" | 1.4" | 4" | 1/4"-16 | 35° to 130° | 0000000 | 000000 |
0.00125" | 5.2" | 16 | 1.7 | 1.2A | 1.8° | Bipolar | 4 | 7.4" | 1.4" | 1.4" | 6" | 1/4"-16 | 35° to 130° | 0000000 | 000000 |
0.00125" | 7.2" | 28 | 2 | 2A | 1.8° | Bipolar | 4 | 9.7" | 1.4" | 1.4" | 8" | 1/4"-16 | 35° to 130° | 0000000 | 000000 |
0.00125" | 11.2" | 16 | 1.7 | 1.2A | 1.8° | Bipolar | 4 | 13.4" | 1.4" | 1.4" | 12" | 1/4"-16 | 35° to 130° | 0000000 | 000000 |
Pass-Through Lead Screw | |||||||||||||||
NEMA 14 | |||||||||||||||
0.00024" | 4.5" | 50 | 0.3 | 1.2A | 1.8° | Bipolar | 4 | 6.3" | 1.4" | 1.4" | 6" | 7/32"-48 | 35° to 130° | 0000000 | 000000 |
0.00024" | 10.5" | 50 | 0.3 | 1.2A | 1.8° | Bipolar | 4 | 12.3" | 1.4" | 1.4" | 12" | 7/32"-48 | 35° to 130° | 0000000 | 000000 |
0.00125" | 4.5" | 16 | 1.7 | 1.2A | 1.8° | Bipolar | 4 | 6.3" | 1.4" | 1.4" | 6" | 1/4"-16 | 35° to 130° | 0000000 | 000000 |
0.00125" | 10.5" | 16 | 1.7 | 1.2A | 1.8° | Bipolar | 4 | 12.3" | 1.4" | 1.4" | 12" | 1/4"-16 | 35° to 130° | 0000000 | 000000 |
Positioning Slides for Stepper Motors
Add your own stepper motor and controller to precisely move the ball screw and carriage smoothly at high speeds, like a head on an inkjet printer. With a repeatability of ± 0.01 mm—thinner than a strand of hair—the carriage hits the same spot every time. These positioning slides work well for automated assemblies and other applications that require fine, repeatable motion control.
The carriage rides along the inside of the rail, making these slides more compact than traditional carriages and guide rails. Made of steel with a U-shaped rail, these slides resist twisting forces that could affect their positioning. This also means they can be installed with only one end supported or with both ends overhanging. The same load rating applies no matter how the slides are oriented.
Travel distance per turn, also known as screw lead, is how far the carriage moves with one rotation of the ball screw.
For technical drawings and 3-D models, click on a part number.
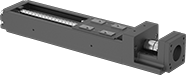
Dynamic Load Capacity, lbs. | Overall | Carriage | |||||||||||||||
---|---|---|---|---|---|---|---|---|---|---|---|---|---|---|---|---|---|
Stroke Lg., mm | Horizontal | Vertical | Max. Speed, mm/s | Travel Distance per Turn, mm | Repeatability, mm | For Shaft Dia. | For Max. Motor Speed, rpm | For Max. Motor Torque, in.-oz. | Lg., mm | Wd., mm | Ht., mm | Lg., mm | Wd., mm | Bearing Type | Base Material | Each | |
For NEMA 14 Motor Frame Size | |||||||||||||||||
30 | 148 | 148 | 100 | 1 | ±0.01 | 5mm | 6,000 | 29.3 | 166 | 40 | 42 | 46 | 23 | Ball | Steel | 00000000 | 0000000 |
80 | 148 | 148 | 100 | 1 | ±0.01 | 5mm | 6,000 | 29.3 | 216 | 40 | 42 | 46 | 23 | Ball | Steel | 00000000 | 00000000 |
110 | 528 | 528 | 200 | 2 | ±0.01 | 5mm | 6,000 | 88.1 | 276 | 50 | 36 | 47.4 | 31 | Ball | Steel | 00000000 | 00000000 |
130 | 148 | 148 | 100 | 1 | ±0.01 | 5mm | 6,000 | 29.3 | 266 | 40 | 42 | 46 | 23 | Ball | Steel | 00000000 | 00000000 |