Robot Bases
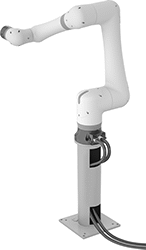
Elevate robot arms with these bases so they can reach onto raised surfaces, such as conveyor belts or workstations. Made from steel, these bases are strong and built to last—they’re also machinable and weldable, so you can modify the mounting plates to suit your application. Secure them to the ground or other flat surface using the holes in the bottom plate. Additional holes are designed to level the bases—thread fasteners (not included) through each hole and adjust their depth to compensate for uneven floors. These bases are only for use at collaborative speeds. They are not designed for robots moving at high speeds.
If you do not see your robot model arm listed, you will need to confirm compatibility yourself. In addition to mounting hole pattern, you will also need to ensure that the maximum potential forces of your robot arm and application are within safe limits for the base's footprint, center of gravity, and any additional anchoring systems. Taller bases have a higher center of gravity and thus require heavier anchoring systems to maintain stability at higher forces compared to shorter bases.
For technical drawings and 3-D models, click on a part number.
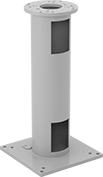
Bolt-on bases come with mounting holes that match the patterns on commonly used robot arms.
Bases with cable routing hole are hollow, so you can feed cables, wires, and tubes through the center column. These bases help keep your cables organized and out of the way.
Overall | Robot Mount. Location | Floor Mount. Location | |||||||||||
---|---|---|---|---|---|---|---|---|---|---|---|---|---|
For Robot Arm Manufacturer (Series/Model No.) | Ht. | Lg. | Wd. | Static Load Cap., lbs. | Mount. Fasteners Included | Mount. Hole Dia. (No. of Holes) | Mount. Plate Dia. | Mount. Hole Dia. (No. of Holes) | Mount. Plate Lg. | Mount. Plate Wd. | Features | Each | |
Gray Powder-Coated Steel | |||||||||||||
FANUC (CRX 5iA, 10iA, 10iA/L, 20iA/L) Universal Robots (UR3, UR3e, UR5, UR5e, UR10, UR10e, UR16, UR16e) Omron (TM 5, TM 12, TM 14) | 24" | 11 7/8" | 11 7/8" | 200 | No | 0.236" (4) 0.315" (2) | 8" | 9/16" (4) | 11 7/8" | 11 7/8" | 1/2"-13 Holes for Leveling, Cable Routing Hole | 0000000 | 0000000 |
FANUC (CRX 5iA, 10iA, 10iA/L) Universal Robots (UR3, UR3e, UR5, UR5e, UR10, UR10e, UR16, UR16e) Omron (TM 5, TM 12, TM 14) | 30" | 11 7/8" | 11 7/8" | 200 | No | 0.236" (4) 0.315" (2) | 8" | 9/16" (4) | 11 7/8" | 11 7/8" | 1/2"-13 Holes for Leveling, Cable Routing Hole | 0000000 | 000000 |
FANUC (CRX 5iA, 10iA, 10iA/L) Universal Robots (UR3, UR3e, UR5, UR5e, UR10, UR10e, UR16, UR16e) Omron (TM 5, TM 12, TM 14) | 36" | 11 7/8" | 11 7/8" | 200 | No | 0.236" (4) 0.315" (2) | 8" | 9/16" (4) | 11 7/8" | 11 7/8" | 1/2"-13 Holes for Leveling, Cable Routing Hole | 0000000 | 000000 |
FANUC (CRX 5iA, 10iA, 10iA/L) Universal Robots (UR3, UR3e, UR5, UR5e, UR10, UR10e, UR16, UR16e) Omron (TM 5, TM 12, TM 14) | 42" | 11 7/8" | 11 7/8" | 200 | No | 0.236" (4) 0.315" (2) | 8" | 9/16" (4) | 11 7/8" | 11 7/8" | 1/2"-13 Holes for Leveling, Cable Routing Hole | 0000000 | 000000 |
FANUC (CRX 5iA, 10iA, 10iA/L) Universal Robots (UR3, UR3e, UR5, UR5e, UR10, UR10e, UR16, UR16e) Omron (TM 5, TM 12, TM 14) | 48" | 11 7/8" | 11 7/8" | 200 | No | 0.236" (4) 0.315" (2) | 8" | 9/16" (4) | 11 7/8" | 11 7/8" | 1/2"-13 Holes for Leveling, Cable Routing Hole | 0000000 | 000000 |
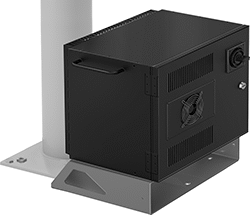
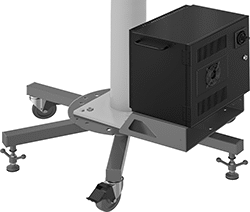
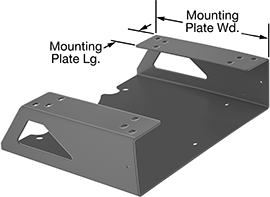
Use these mounts with robot bases to secure your controller near your robot arm for easy access and to cut down on cord lengths. When installed, these mounts elevate your controller off the floor, keeping it out of harm’s way.
Overall | Controller Mount. Location | Base Mount. Location | |||||||||
---|---|---|---|---|---|---|---|---|---|---|---|
For Robot Arm Manufacturer (Series/Model No.) | Ht. | Lg. | Wd. | Mount. Fasteners Included | Mount. Hole Dia. (No. of Holes) | Mount. Plate Lg. | Mount. Plate Wd. | Mount. Fasteners Included | Mount. Hole Dia. (No. of Holes) | Each | |
Gray Powder-Coated Steel | |||||||||||
FANUC (CRX 5iA, 10iA, 10iA/L, 20iA/L, 25iA) Universal Robots (UR3, UR3e, UR5, UR5e, UR10, UR10e, UR16, UR16e) Omron (TM 5, TM 12, TM 14) | 4 1/4" | 16 3/4" | 11" | Yes | 1/4" (12) | 3 1/8" | 9" | Yes | 1/4" (5) | 0000000 | 0000000 |
Mounts for Robot Controllers
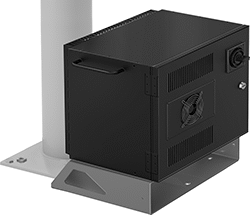
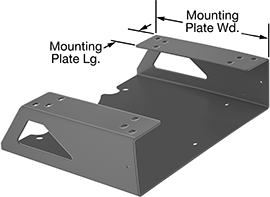
Use these mounts with robot bases to secure your controller near your robot arm for easy access and to cut down on cord lengths. When installed, these mounts elevate your controller off the floor, keeping it out of harm’s way.
For technical drawings and 3-D models, click on a part number.
Overall | Controller Mount. Location | Base Mount. Location | |||||||||
---|---|---|---|---|---|---|---|---|---|---|---|
For Robot Arm Manufacturer (Series/Model No.) | Ht. | Lg. | Wd. | Mount. Fasteners Included | Mount. Hole Dia. (No. of Holes) | Mount. Plate Lg. | Mount. Plate Wd. | Mount. Fasteners Included | Mount. Hole Dia. (No. of Holes) | Each | |
Gray Powder-Coated Steel | |||||||||||
FANUC (CRX 5iA, 10iA, 10iA/L, 20iA/L, 25iA) Universal Robots (UR3, UR3e, UR5, UR5e, UR10, UR10e, UR16, UR16e) Omron (TM 5, TM 12, TM 14) | 4 1/4" | 16 3/4" | 11" | Yes | 1/4" (12) | 3 1/8" | 9" | Yes | 1/4" (5) | 0000000 | 0000000 |
Robot Tool Accessory Mounts
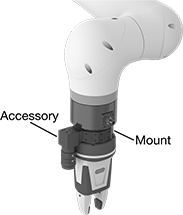
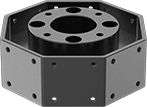
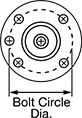
Attach accessories alongside primary tools on robot arms. These mounts are commonly used to connect air nozzles to remove debris, cameras to document work, and sensors to track forces. With eight sides for mounting, they allow you to connect multiple accessories at once. These mounts adhere to ISO mounting standards, and connect robot arms and tools with ISO 50 mounting patterns. Use adapters (sold separately) to pair with arms or tools that have different mounting patterns. If you don't see your robot model number listed, measure the bolt circle diameter to determine mounting compatibility.
Made of aluminum, these mounts are lightweight, helping your robot arm stay under its payload limit, or weight limit. They’re machinable, so you can drill your own holes to match uncommon mounting patterns. Plus, they resist corrosion. Mounts come with all the hardware you need to connect them to robot arms, but not all the hardware required to connect robot tools to mounts.
For technical drawings and 3-D models, click on a part number.
End of Robot Arm (Bolt On) | Robot Tool (Bolt On) | Robot Accessory | ||||||||
---|---|---|---|---|---|---|---|---|---|---|
Bolt Circle Dia. (Mount. Hole Pattern Compatibility) | Mounting Fasteners Included | Bolt Circle Dia. (Mount. Hole Pattern Compatibility) | Bolt Hole Thread Size (No. of) | Mounting Fasteners Included | Bolt Hole Thread Size (No. of) | Mounting Fasteners Included | Wt. | For Robot Arm Manufacturer (Series/Model Number) | Each | |
Black Anodized Aluminum | ||||||||||
50 mm (ISO 50) | Yes | 50 mm (ISO 50) | M6 × 1 mm (4) | No | 8-32 (32) | No | 2.1 lbs./ 0.92 kg | ABB (IRB 2400; IRB 2600) FANUC (CRX 5iA, 10iA, 10iA/L, 20iA/L, 25iA) Universal Robots (UR3; UR3e; UR5; UR5e; UR10; UR10e; UR16; UR16e) Omron (TM 5, 12, 14) Staubli (TX2 90) Productive Robotics (OB7) | 0000000 | 0000000 |
Robot Tool Mounts for T-Slotted Framing
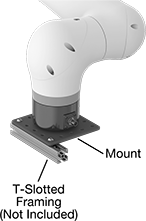
Connect your robot arm to tools or extensions made from T-slotted framing. These mounts are often used to support custom tools for uniquely shaped items, such as a rig to lift chairs off of a line, or as a mounting base for a screwdriver. They use ISO mounting patterns, an industry standard for arm connections. These mounts are made of aluminum, so they’re corrosion resistant, lightweight, and machinable. The lightness helps you keep robot arms under their payload, or weight limit, and the machinability means you can drill your own holes. Mounts come with all the hardware needed to connect them to robot arms, but not the bolts required to connect T-slotted framing to the mounts. If you don't see your robot model number listed, measure the bolt circle diameter to determine mounting compatibility.
Round mounts are compatible with several ISO mounting patterns, so they connect to a wide variety of robot arms. They’re also lighter and smaller than other mounts, so they fit in tight spaces. However, with only two mounting holes for T-slotted framing, they have fewer attachment options than other mounts.
Square mounts have 16 mounting holes for T-slotted framing, giving you more mounting options than round mounts. They’re heavier, however, and take up more space.
L-shaped mounts create a 90° mounting angle, so you can position tools to point down or forward. These mounts are also commonly used to connect tools that don’t have standard ISO mounting patterns and can’t bolt directly to robot arms.
X-shaped mounts have a broad surface area, spreading out T-slotted framing or robot tools for handling large objects.
Use robot tool mounts (sold separately) with square, L-shaped, and X-shaped mounts for compatibility with different ISO mounting patterns.
For technical drawings and 3-D models, click on a part number.
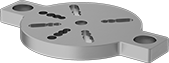
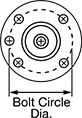
End of Robot Arm (Bolt On) | For Rail Ht. | T-Slotted Framing (Bolt On) | |||||||||
---|---|---|---|---|---|---|---|---|---|---|---|
Bolt Circle Dia. (Mount. Hole Pattern Compatibility) | Mounting Fasteners Included | Single | Double and Quad | Triple | For Bolt Size (No. of) | Mounting Fasteners Included | Max. Load Cap. | Wt. | For Robot Arm Manufacturer (Series/Model Number) | Each | |
Aluminum | |||||||||||
31.5 mm (ISO 31.5) 40 mm (ISO 40) 50 mm (ISO 50) 63 mm (ISO 63) | Yes | 1" | 2" | 3" | M6 (2) | No | 110 lbs./ 50 kg | 0.31 lbs./ 0.14 kg | ABB (IRB 360 6/1600, 8/1130; IRB 120; IRB 140; IRB 1200; IRB 1410; IRB 1520ID; IRB 1600; IRB 2400; IRB 2600) FANUC (CR 4iA, 7iA; CRX 5iA, 10iA, 10iA/L, 20iA/L, 25iA; LR Mate 200iD/7L; M-20 iA) KUKA Robotics (KR 10 R1100-2) Yaskawa/Motoman (GP 7, 8; MH 3BM, 3F, 5LS II, 5S II; MPP 3H, 3S; HC 10T; SIA 10D, 10F) Precise Automation (PAVP6; PF3400; PP100) Universal Robots (UR3; UR3e; UR5; UR5e; UR10; UR10e; UR16; UR16e) Omron (TM 5, 12, 14) Staubli (TX2 90) Productive Robotics (OB7) | 0000000 | 000000 |
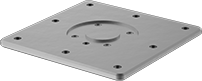
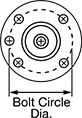
End of Robot Arm (Bolt On) | For Rail Ht. | T-Slotted Framing (Bolt On) | |||||||||
---|---|---|---|---|---|---|---|---|---|---|---|
Bolt Circle Dia. (Mount. Hole Pattern Compatibility) | Mounting Fasteners Included | Single | Double and Quad | Triple | For Bolt Size (No. of) | Mounting Fasteners Included | Max. Load Cap. | Wt. | For Robot Arm Manufacturer (Series/Model Number) | Each | |
Powder-Coated Aluminum | |||||||||||
50 mm (ISO 50) | Yes | 1" | 2" | 3" | 1/4"-20 (8) | No | 35 lbs./ 16 kg | 0.78 lbs./ 0.35 kg | ABB (IRB 2400; IRB 2600) FANUC (CRX 5iA, 10iA, 10iA/L, 20iA/L, 25iA) Universal Robots (UR3; UR3e; UR5; UR5e; UR10; UR10e; UR16; UR16e) Omron (TM 5, 12, 14) Staubli (TX2 90) Productive Robotics (OB7) | 0000000 | 0000000 |
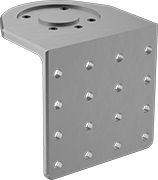
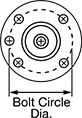
End of Robot Arm (Bolt On) | For Rail Ht. | T-Slotted Framing (Bolt On) | |||||||||
---|---|---|---|---|---|---|---|---|---|---|---|
Bolt Circle Dia. (Mount. Hole Pattern Compatibility) | Mounting Fasteners Included | Single | Double and Quad | Triple | For Bolt Size (No. of) | Mounting Fasteners Included | Max. Load Cap. | Wt. | For Robot Arm Manufacturer (Series/Model Number) | Each | |
Powder-Coated Aluminum | |||||||||||
50 mm (ISO 50) | Yes | 1" | 2" | 3" | 1/4"-20 (16) | No | 35 lbs./ 16 kg | 0.75 lbs./ 0.34 kg | ABB (IRB 2400; IRB 2600) FANUC (CRX 5iA, 10iA, 10iA/L, 20iA/L, 25iA) Universal Robots (UR3; UR3e; UR5; UR5e; UR10; UR10e; UR16; UR16e) Omron (TM 5, 12, 14) Staubli (TX2 90) Productive Robotics (OB7) | 0000000 | 0000000 |
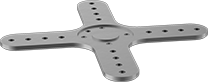
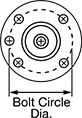
End of Robot Arm (Bolt On) | For Rail Ht. | T-Slotted Framing (Bolt On) | |||||||||
---|---|---|---|---|---|---|---|---|---|---|---|
Bolt Circle Dia. (Mount. Hole Pattern Compatibility) | Mounting Fasteners Included | Single | Double and Quad | Triple | For Bolt Size (No. of) | Mounting Fasteners Included | Max. Load Cap. | Wt. | For Robot Arm Manufacturer (Series/Model Number) | Each | |
Powder-Coated Aluminum | |||||||||||
50 mm (ISO 50) | Yes | 1" | 2" | 3" | 1/4"-20 (16) | No | 35 lbs./ 16 kg | 0.93 lbs./ 0.42 kg | ABB (IRB 2400; IRB 2600) FANUC (CRX 5iA, 10iA, 10iA/L, 20iA/L, 25iA) Universal Robots (UR3; UR3e; UR5; UR5e; UR10; UR10e; UR16; UR16e) Omron (TM 5, 12, 14) Staubli (TX2 90) Productive Robotics (OB7) | 0000000 | 0000000 |
50 mm (ISO 50) | Yes | 1" | 2" | 3" | 1/4"-20 (28) | No | 35 lbs./ 16 kg | 1.2 lbs./ 0.52 kg | ABB (IRB 2400; IRB 2600) FANUC (CRX 5iA, 10iA, 10iA/L, 20iA/L, 25iA) Universal Robots (UR3; UR3e; UR5; UR5e; UR10; UR10e; UR16; UR16e) Omron (TM 5, 12, 14) Staubli (TX2 90) Productive Robotics (OB7) | 0000000 | 000000 |
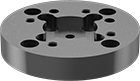
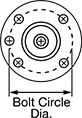
Robot Tool (Bolt On) | End of Robot Arm (Bolt On) | |||||||
---|---|---|---|---|---|---|---|---|
Bolt Circle Dia. (Mount. Hole Pattern Compatibility) | Bolt Hole Thread Size (No. of) | Mounting Fasteners Included | Bolt Circle Dia. (Mount. Hole Pattern Compatibility) | Mounting Fasteners Included | Wt. | Max. Load Cap. | Each | |
Black Anodized Aluminum | ||||||||
50 mm (ISO 50) | M6 × 1 mm (4) | No | 31.5 mm (ISO 31.5) 40 mm (ISO 40) 63 mm (ISO 63) | Yes | 0.36 lbs./ 0.16 kg | 110 lbs./ 50 kg | 0000000 | 0000000 |
Robot Tool Mounts
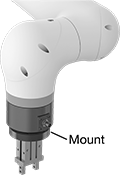
Connect robot tools to robot arms that have different ISO mounting patterns. Compatible with some models of Universal Robots (UR) and FANUC robots, these mounts are commonly used to equip robot arms with pick-and-place grippers, vacuum grippers, and sanders. They use ISO mounting patterns, an industry standard for arm connections. Mounts come with all the hardware you need to connect them to robot arms, but not all the hardware required to connect robot tools to mounts. If you don't see your robot model number listed, measure the bolt circle diameter to determine mounting compatibility.
Bolt-on mounts have ISO mounting patterns on the tool side.
Blank mounts don’t have drilled holes on the tool side. Machine your own holes for compatibility with unusual mounting patterns.
Threaded mounts have a universal female-threaded connection on the tool side for attaching threaded tools, pipe, rods, and other components to robot arms. If you need a male-threaded connection, choose one with an included universal thread adapter. For other thread types and sizes, add a universal thread adapter.
Aluminum mounts are a lightweight metal alternative to stainless steel, helping your robot arm stay under its payload limit, or the total capacity a robot can lift. They’re also more machinable than stainless steel, so you can drill your own holes for robots with unusual mounting patterns. These mounts resist corrosion.
Acetal plastic mounts are lightweight and strong. Often used in food-processing plants, they won’t corrode from frequent washdowns with harsh cleaners.
To extend your robot arm’s reach, use robot tool extensions.
For technical drawings and 3-D models, click on a part number.
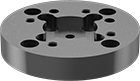
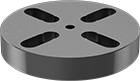
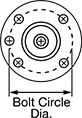
Robot Tool | End of Robot Arm (Bolt On) | ||||||||
---|---|---|---|---|---|---|---|---|---|
Bolt Circle Dia. (Mount. Hole Pattern Compatibility) | Bolt Hole Thread Size (No. of) | Mounting Fasteners Included | Bolt Circle Dia. (Mount. Hole Pattern Compatibility) | Mounting Fasteners Included | Wt. | Max. Load Cap. | For Robot Arm Manufacturer (Series/Model Number) | Each | |
Bolt On | |||||||||
31.5 mm (ISO 31.5) | M5 × 0.8 mm (4) | No | 40 mm (ISO 40) 50 mm (ISO 50) 63 mm (ISO 63) | Yes | 0.36 lbs./ 0.16 kg | 110 lbs./ 50 kg | ABB (IRB 360 6/1600, 8/1130; IRB 140; IRB 1410 IRB 1520ID; IRB 1600; IRB 2400; IRB 2600) FANUC (CRX 5iA, 10iA, 10iA/L, 20iA/L, 25iA; M-20 iA) Omron (TM 5, 12, 14) Precise Automation (PP100) Productive Robotics (OB7) Staubli (TX2 90) Universal Robots (UR3; UR3e; UR5; UR5e; UR10; UR10e; UR16; UR16e) Yaskawa/Motoman (GP 10T, MH 10D, 10F) | 0000000 | 0000000 |
40 mm (ISO 40) | M6 × 1 mm (4) | No | 31.5 mm (ISO 31.5) 50 mm (ISO 50) 63 mm (ISO 63) | Yes | 0.36 lbs./ 0.16 kg | 110 lbs./ 50 kg | ABB (IRB 120; IRB 1200; IRB 1520ID; IRB 2400; IRB 2600) FANUC (CR 4iA, 7iA; CRX 5iA, 10iA, 10iA/L, 20iA/L, 25iA; LR Mate 200iD/7L) KUKA Robotics (KR 10 R1100-2) Omron (TM 5, 12, 14) Precise Automation (PAVP6; PF3400) Productive Robotics (OB7) Staubli (TX2 90) Universal Robots (UR3; UR3e; UR5; UR5e; UR10; UR10e; UR16; UR16e) Yaskawa/Motoman (GP 7, 8; MH 3BM, 3F, 5LS II, 5S II; MPP 3H, 3S; HC 10T; SIA 10D, 10F) | 0000000 | 000000 |
50 mm (ISO 50) | M6 × 1 mm (4) | No | 31.5 mm (ISO 31.5) 40 mm (ISO 40) 63 mm (ISO 63) | Yes | 0.36 lbs./ 0.16 kg | 110 lbs./ 50 kg | ABB (IRB 360 6/1600, 8/1130; IRB 120; IRB 140; IRB 1200; IRB 1410; IRB 1520ID; IRB 1600) FANUC (CR 4iA, 7iA; 5iA, 10iA, 10iA/L, 20iA/L, 25iA; LR Mate 200iD/7L; M-20 iA) KUKA Robotics (KR 10 R1100-2) Precise Automation (PAVP6; PF3400; PP100) Yaskawa/Motoman (GP 7, 8; MH 3BM, 3F, 5LS II, 5S II; MPP 3H, 3S; HC 10T; SIA 10D, 10F) | 0000000 | 000000 |
63 mm (ISO 63) | M6 × 1 mm (4) | No | 31.5 mm (ISO 31.5) 40 mm (ISO 40) 50 mm (ISO 50) | Yes | 0.36 lbs./ 0.16 kg | 110 lbs./ 50 kg | ABB (IRB 360 6/1600, 8/1130; IRB 120; IRB 140; IRB 1200; IRB 1410; IRB 1600; IRB 2400; IRB 2600) FANUC (CR 4iA, 7iA; CRX 5iA, 10iA, 10iA/L, 20iA/L, 25iA; LR Mate 200iD/7L; M-20 iA) KUKA Robotics (KR 10 R1100-2) Omron (TM 5, 12, 14) Precise Automation (PAVP6; PF3400; PP100) Productive Robotics (OB7) Staubli (TX2 90) Universal Robots (UR3; UR3e; UR5; UR5e; UR10; UR10e; UR16; UR16e) Yaskawa/Motoman (GP 7, 8; MH 3BM, 3F, 5LS II, 5S II; MPP 3H, 3S) | 0000000 | 000000 |
Blank | |||||||||
__ | __ | No | 31.5 mm (ISO 31.5) 40 mm (ISO 40) 50 mm (ISO 50) 63 mm (ISO 63) | Yes | 0.4 lbs./ 0.18 kg | 110 lbs./ 50 kg | ABB (IRB 360 6/1600, 8/1130; IRB 120; IRB 140; IRB 1200; IRB 1410; IRB 1520ID; IRB 1600; IRB 2400; IRB 2600) FANUC (CR 4iA, 7iA; CRX 5iA, 10iA, 10iA/L, 20iA/L, 25iA; LR Mate 200iD/7L; M-20 iA) KUKA Robotics (KR 10 R1100-2) Omron (TM 5, 12, 14) Precise Automation (PAVP6; PF3400; PP100) Productive Robotics (OB7) Staubli (TX2 90) Universal Robots (UR3; UR3e; UR5; UR5e; UR10; UR10e; UR16; UR16e) Yaskawa/Motoman (GP 7, 8; MH 3BM, 3F, 5LS II, 5S II; MPP 3H, 3S; HC 10T; SIA 10D, 10F) | 0000000 | 000000 |
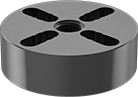
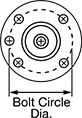
Robot Tool | End of Robot Arm (Bolt On) | ||||||||
---|---|---|---|---|---|---|---|---|---|
Pipe Size | Gender | Mounting Fasteners Included | Bolt Circle Dia. (Mounting Hole Pattern Compatibility) | Mounting Fasteners Included | Max. Load Cap. | Includes | For Robot Arm Manufacturer (Series/Model Number) | Each | |
Threaded | |||||||||
3/8 | Female | No | 31.5 mm (ISO 31.5) 40 mm (ISO 40) 50 mm (ISO 50) 63 mm (ISO 63) | Yes | 110 lbs. / 50 kg | __ | ABB (IRB 360 6/1600, 8/1130; IRB 120; IRB 140; IRB 1200; IRB 1410; IRB 1520ID; IRB 1600; IRB 2400; IRB 2600) FANUC (CR 4iA, 7iA; CRX 5iA, 10iA, 10iA/L, 20iA/L, 25iA; LR Mate 200iD/7L; M-20 iA) KUKA Robotics (KR 10 R1100-2) Omron (TM 5, 12, 14) Precise Automation (PAVP6; PF3400; PP100) Productive Robotics (OB7) Staubli (TX2 90) Universal Robots (UR3; UR3e; UR5; UR5e; UR10; UR10e; UR16; UR16e) Yaskawa/Motoman (GP 7, 8; MH 3BM, 3F, 5LS II, 5S II; MPP 3H, 3S; HC 10T; SIA 10D, 10F) | 00000000 | 0000000 |
3/8 | Female | Yes | 31.5 mm (ISO 31.5) 40 mm (ISO 40) 50 mm (ISO 50) 63 mm (ISO 63) | Yes | 110 lbs. / 50 kg | Universal 1/4 Male Thread Adapter | ABB (IRB 360 6/1600, 8/1130; IRB 120; IRB 140; IRB 1200; IRB 1410; IRB 1520ID; IRB 1600; IRB 2400; IRB 2600) FANUC (CR 4iA, 7iA; CRX 5iA, 10iA, 10iA/L, 20iA/L, 25iA; LR Mate 200iD/7L; M-20 iA) KUKA Robotics (KR 10 R1100-2) Omron (TM 5, 12, 14) Precise Automation (PAVP6; PF3400; PP100) Productive Robotics (OB7) Staubli (TX2 90) Universal Robots (UR3; UR3e; UR5; UR5e; UR10; UR10e; UR16; UR16e) Yaskawa/Motoman (GP 7, 8; MH 3BM, 3F, 5LS II, 5S II; MPP 3H, 3S; HC 10T; SIA 10D, 10F) | 00000000 | 000000 |
3/8 | Female | Yes | 31.5 mm (ISO 31.5) 40 mm (ISO 40) 50 mm (ISO 50) 63 mm (ISO 63) | Yes | 110 lbs. / 50 kg | Universal 1/8 Male Thread Adapter | ABB (IRB 360 6/1600, 8/1130; IRB 120; IRB 140; IRB 1200; IRB 1410; IRB 1520ID; IRB 1600; IRB 2400; IRB 2600) FANUC (CR 4iA, 7iA; CRX 5iA, 10iA, 10iA/L, 20iA/L, 25iA; LR Mate 200iD/7L; M-20 iA) KUKA Robotics (KR 10 R1100-2) Omron (TM 5, 12, 14) Precise Automation (PAVP6; PF3400; PP100) Productive Robotics (OB7) Staubli (TX2 90) Universal Robots (UR3; UR3e; UR5; UR5e; UR10; UR10e; UR16; UR16e) Yaskawa/Motoman (GP 7, 8; MH 3BM, 3F, 5LS II, 5S II; MPP 3H, 3S; HC 10T; SIA 10D, 10F) | 00000000 | 000000 |
Mounts for Two Robot Tools
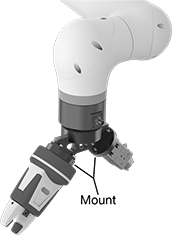
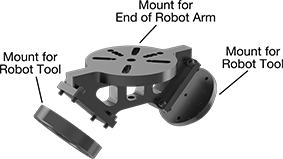
Equip your robot arm with two tools at once—these mounts have two offset, angled mounting surfaces for tools. They’re often used to speed up a robot’s work cycle, such as when two grippers swap workpieces in and out of a CNC machine. Or, use them to mount tools with different functions, such as a pick-and-place gripper that puts a workpiece into a vice and a sander that finishes the workpiece. They’re compatible with the most common robot arms, including some models from Universal Robots (UR) and FANUC.
These mounts are made of aluminum, so they’re corrosion resistant, lightweight, and machinable. The lightness helps you keep robot arms under their payload, or weight limit, and the machinability means you can drill your own holes.
For a complete system, you'll need an end-of-robot-arm mount and two tool-side mounts. These mounts include fasteners to attach mounts to your arm, and fasteners to attach tool-side mounts, but not fasteners for attaching your tools.
Bolt-on mounts have a standard ISO mounting pattern—choose one that matches the mounting pattern of your robot arm and tools. If you don't see your robot model number listed, measure the bolt circle diameter to determine mounting compatibility.
To extend your robot arm’s reach, use robot tool extensions.
For technical drawings and 3-D models, click on a part number.
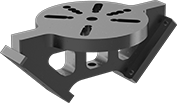
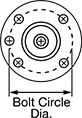
Mounting Plate, mm | |||||||||
---|---|---|---|---|---|---|---|---|---|
Mount Type | Bolt Circle Dia. (Mount. Hole Pattern Compatibility) | Mounting Fasteners Included | Dia. | Wd. | Max. Load Cap. | Wt. | For Robot Arm Manufacturer (Series/Model Number) | Each | |
Black Anodized Aluminum | |||||||||
Bolt On | 31.5 mm (ISO 31.5) 40 mm (ISO 40) 50 mm (ISO 50) 63 mm (ISO 63) | Yes | 80 | 128 | 110 lbs./ 50 kg | 0.56 lbs./ 0.25 kg | ABB (IRB 360 6/1600, 8/1130; IRB 120; IRB 140; IRB 1200; IRB 1410; IRB 1520ID; IRB 1600; IRB 2400; IRB 2600) FANUC (CR 4iA, 7iA; CRX 5iA, 10iA, 10iA/L, 20iA/L, 25iA; LR Mate 200iD/7L; M-20 iA) KUKA Robotics (KR 10 R1100-2) Yaskawa/Motoman (GP 7, 8; MH 3BM, 3F, 5LS II, 5S II; MPP 3H, 3S; HC 10T; SIA 10D, 10F) Precise Automation (PAVP6; PF3400; PP100) Universal Robots (UR3; UR3e; UR5; UR5e; UR10; UR10e; UR16; UR16e) Omron (TM 5, 12, 14) Staubli (TX2 90) Productive Robotics (OB7) | 0000000 | 0000000 |
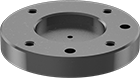
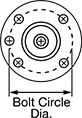
Mount Type | Bolt Circle Dia. (Mount. Hole Pattern Compatibility) | Mounting Fasteners Included | Bolt Hole Thread Size (No. of) | Max. Load Cap. | Wt. | Each | |
Black Anodized Aluminum | |||||||
---|---|---|---|---|---|---|---|
Bolt On | 50 mm (ISO 50) | No | M6 × 1 mm (4) | 110 lbs./ 50 kg | 0.18 lbs./ 0.08 kg | 0000000 | 000000 |
Robot Tool Extensions
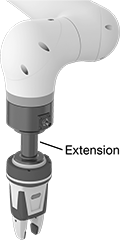
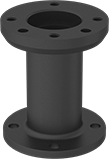
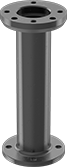
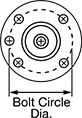
Extend the reach of your robot arm, so it can access the full width of a conveyor or the bottom of deep containers. These extensions use standard ISO mounting patterns, so they’re compatible with most robot arms and tools, such as those made by Universal Robots (UR) and FANUC. Select an extension with an ISO mounting pattern that matches your arm and tool, or use a robot tool mount (sold separately) to adapt to a different pattern. They include mounting hardware to connect them to your robot arm, but don’t have hardware to connect to tools. If you don't see your robot model number listed, measure the bolt circle diameter to determine mounting compatibility.
These extensions are lightweight, corrosion resistant, and strong. They’re also machinable, so you can modify them to mount to custom patterns. Acetal is lighter and less rigid than aluminum, so it’s used for shorter extensions. Aluminum is heavier and more rigid than acetal. It’s used for longer extensions, since it’s stiff enough to keep your tool from wobbling as the arm moves.
For technical drawings and 3-D models, click on a part number.
End of Robot Arm (Bolt On) | Robot Tool (Bolt On) | ||||||||||
---|---|---|---|---|---|---|---|---|---|---|---|
Lg., mm | OD, mm | Max. Load Cap. | Wt. | Bolt Circle Dia. (Mount. Hole Pattern Compatibility) | Mount. Fasteners Included | Bolt Circle Dia. (Mount. Hole Pattern Compatibility) | Mount. Fasteners Included | Bolt Hole Thread Size (No. of) | For Robot Arm Manufacturer (Series/Model Number) | Each | |
Black Acetal Plastic | |||||||||||
25 | 63 | 110 lbs./ 50 kg | 0.25 lbs./ 0.11 kg | 50 mm (ISO 50) | Yes | 50 mm (ISO 50) | No | M6 × 1 mm (4) | ABB (IRB 2400; IRB 2600) FANUC (CRX 5iA, 10iA, 10iA/L, 20iA/L, 25iA) Universal Robots (UR3; UR3e; UR5; UR5e; UR10; UR10e; UR16; UR16e) Omron (TM 5, 12, 14) Staubli (TX2 90) Productive Robotics (OB7) | 0000000 | 0000000 |
35 | 63 | 110 lbs./ 50 kg | 0.18 lbs./ 0.08 kg | 50 mm (ISO 50) | Yes | 50 mm (ISO 50) | No | M6 × 1 mm (4) | ABB (IRB 2400; IRB 2600) FANUC (CRX 5iA, 10iA, 10iA/L, 20iA/L, 25iA) Universal Robots (UR3; UR3e; UR5; UR5e; UR10; UR10e; UR16; UR16e) Omron (TM 5, 12, 14) Staubli (TX2 90) Productive Robotics (OB7) | 0000000 | 000000 |
50 | 63 | 110 lbs./ 50 kg | 0.2 lbs./ 0.09 kg | 50 mm (ISO 50) | Yes | 50 mm (ISO 50) | No | M6 × 1 mm (4) | ABB (IRB 2400; IRB 2600) FANUC (CRX 5iA, 10iA, 10iA/L, 20iA/L, 25iA) Universal Robots (UR3; UR3e; UR5; UR5e; UR10; UR10e; UR16; UR16e) Omron (TM 5, 12, 14) Staubli (TX2 90) Productive Robotics (OB7) | 0000000 | 000000 |
75 | 63 | 110 lbs./ 50 kg | 0.25 lbs./ 0.11 kg | 50 mm (ISO 50) | Yes | 50 mm (ISO 50) | No | M6 × 1 mm (4) | ABB (IRB 2400; IRB 2600) FANUC (CRX 5iA, 10iA, 10iA/L, 20iA/L, 25iA) Universal Robots (UR3; UR3e; UR5; UR5e; UR10; UR10e; UR16; UR16e) Omron (TM 5, 12, 14) Staubli (TX2 90) Productive Robotics (OB7) | 000000 | 000000 |
Black Anodized Aluminum | |||||||||||
100 | 63 | 110 lbs./ 50 kg | 0.27 lbs./ 0.12 kg | 50 mm (ISO 50) | Yes | 50 mm (ISO 50) | No | M6 × 1 mm (4) | ABB (IRB 2400; IRB 2600) FANUC (CRX 5iA, 10iA, 10iA/L, 20iA/L, 25iA) Universal Robots (UR3; UR3e; UR5; UR5e; UR10; UR10e; UR16; UR16e) Omron (TM 5, 12, 14) Staubli (TX2 90) Productive Robotics (OB7) | 0000000 | 000000 |
150 | 63 | 110 lbs./ 50 kg | 0.31 lbs./ 0.14 kg | 50 mm (ISO 50) | Yes | 50 mm (ISO 50) | No | M6 × 1 mm (4) | ABB (IRB 2400; IRB 2600) FANUC (CRX 5iA, 10iA, 10iA/L, 20iA/L, 25iA) Universal Robots (UR3; UR3e; UR5; UR5e; UR10; UR10e; UR16; UR16e) Omron (TM 5, 12, 14) Staubli (TX2 90) Productive Robotics (OB7) | 0000000 | 000000 |
Quick-Connect Robot Tool Changers
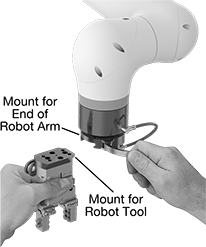
Switch out your end-of-arm tools quickly and easily with these tool changers. Separate mounts for your robot arm and tool join with a quick-connect clamp—simply open the clamp to release your tool. Often used in job shops, these tool changers make it easy to alternate between tasks. They’re also used in sanitary facilities, where tools are cleaned frequently.
A complete assembly includes an end-of-robot-arm mount, which connects to your robot wrist, and a robot-tool mount, which connects to your tool (each sold separately). Some have standard ISO mounting patterns, so they’re compatible with the mounting patterns on most arms and tools. Make sure your power source is disconnected before changing tools.
For applications where space is tight, use low-profile mounts. Together, the two mounts create a tool changer assembly that only adds 21 mm between your robot arm and tool. They’re also lighter than utility mounts that are the same size and material. However, they do not have pass-throughs for air, vacuum, or electrical connections.
Utility mounts have two pneumatic pass-throughs for air and vacuum and a power/signal pass-through for electricity. These pass-throughs let you run connections through the tool changer assembly, rather than wrapping cables and tubes around the outside. This makes it easier to switch tools, especially when changing from pneumatic to electrical tools. The 8-pin electrical connection is compatible with most robot arms and tools.
Aluminum tool changers are lightweight, so they won’t weigh down your robot arm.
For technical drawings and 3-D models, click on a part number.

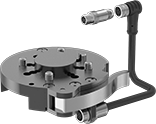
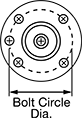
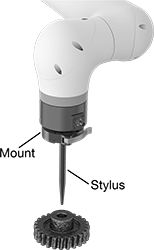
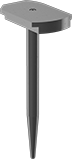
Bolt these mounts to your robot’s wrist with the included fasteners—make sure that the ISO pattern for the mount matches your robot. Mounts with multiple ISO patterns listed are more versatile and fit a variety of robot arms. If you don't see your robot model number listed, measure the bolt circle diameter to determine mounting compatibility. Mounts with only one ISO pattern listed are easy to clean and have fewer spaces where bacteria can grow.
If you are mounting to an arm without an 8-pin connection, select a mount with power/signal connector. This connector has an 8-pin connection on one side and wire leads on the other, so you can adapt to any electrical connection.
Connect a calibration stylus to your mount to line up robots with a work area. They’re often used to direct robots to hole centers when attaching fasteners, or to help them find objects in pick-and-place applications. You can also use them to help your machine-vision camera recognize patterns and locations.
Mounts | ||||||||||
---|---|---|---|---|---|---|---|---|---|---|
Mounting Plate | Calibration Styli | |||||||||
Bolt Circle Dia. (Mount. Hole Pattern Compatibility) | Dia., mm | Max. Load Cap. | Wt. | Lg., mm | Includes | For Robot Arm Manufacturer (Series/Model Number) | Each | Each | ||
Low Profile (Bolt On) | ||||||||||
Black PTFE-Coated Aluminum | ||||||||||
31.5 mm (ISO 31.5) 40 mm (ISO 40) 50 mm (ISO 50) | 83 | 110 lbs. / 50 kg | 0.53 lbs. / 0.24 kg | 19 | __ | ABB (IRB 360 6/1600, 8/1130; IRB 120; IRB 140; IRB 1200; IRB 1410; IRB 1600; IRB 2400; IRB 2600) FANUC (CR 4iA, 7iA; CRX 5iA, 10iA, 10iA/L, 20iA/L, 25iA; LR Mate 200iD/7L; M-20 iA) KUKA Robotics (KR 10 R1100-2) Omron (TM 5, 12, 14) Precise Automation (PAVP6; PF3400; PP100) Productive Robotics (OB7) Staubli (TX2 90) Universal Robots (UR3; UR3e; UR5; UR5e; UR10; UR10e; UR16; UR16e) Yaskawa/Motoman (GP 7, 8; MH 3BM, 3F, 5LS II, 5S II; MPP 3H, 3S) | 00000000 | 0000000 | 00000000 | 0000000 |
Utility (Bolt On) | ||||||||||
Black PTFE-Coated Aluminum | ||||||||||
31.5 mm (ISO 31.5) 40 mm (ISO 40) 50 mm (ISO 50) | 83 | 110 lbs. / 50 kg | 0.71 lbs. / 0.32 kg | 74 | Power/Signal Connector with 5-ft. Wire Leads | ABB (IRB 360 6/1600, 8/1130; IRB 120; IRB 140; IRB 1200; IRB 1410; IRB 1600; IRB 2400; IRB 2600) FANUC (CR 4iA, 7iA; CRX 5iA, 10iA, 10iA/L, 20iA/L, 25iA; LR Mate 200iD/7L; M-20 iA) KUKA Robotics (KR 10 R1100-2) Omron (TM 5, 12, 14) Precise Automation (PAVP6; PF3400; PP100) Productive Robotics (OB7) Staubli (TX2 90) Universal Robots (UR3; UR3e; UR5; UR5e; UR10; UR10e; UR16; UR16e) Yaskawa/Motoman (GP 7, 8; MH 3BM, 3F, 5LS II, 5S II; MPP 3H, 3S) | 00000000 | 00000000 | 00000000 | 000000 |
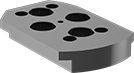
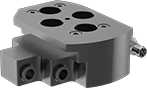
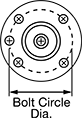
Connect these mounts to your end-of-arm tool with fasteners (not included). Attach the robot-tool mount to the mount on your robot arm with the quick-connect clamp.
Bolt-on tool mounts have mounting holes that match the patterns on commonly used robot tools. The thread sizes also match up with the holes on t-slotted framing and fittings, so you can easily join them to tools made from framing (fasteners are not included). For a custom mounting pattern, drill your own holes into blank tool mounts.
Mounting Plate | ||||||||
---|---|---|---|---|---|---|---|---|
Bolt Circle Dia. (Mounting Hole Pattern Compatibility) | Bolt Hole Thread Size (No. of Holes) | Dia., mm | Lg., mm | Wd., mm | Wt. | Lg., mm | Each | |
Low Profile (Bolt On) | ||||||||
Black PTFE-Coated Aluminum | ||||||||
__ | M6 (4) | __ | 62 | 38 | 0.16 lbs. / 0.07 kg | 12 | 00000000 | 000000 |
__ | M8 (4) | __ | 62 | 38 | 0.17 lbs. / 0.08 kg | 12 | 00000000 | 00000 |
31.5 mm (ISO 31.5) | M5 × 0.8 mm (4) | 40 | __ | __ | 0.34 lbs. / 0.15 kg | 24 | 00000000 | 000000 |
40 mm (ISO 40) | M6 × 1 mm (4) | 50 | __ | __ | 0.35 lbs. / 0.16 kg | 24 | 00000000 | 000000 |
50 mm (ISO 50) | M6 × 1 mm (4) | 63 | __ | __ | 0.38 lbs. / 0.18 kg | 24 | 00000000 | 000000 |
Low Profile (Blank) | ||||||||
Black PTFE-Coated Aluminum | ||||||||
__ | __ | __ | 62 | 38 | 0.20 lbs. / 0.09 kg | 12 | 00000000 | 00000 |
Utility (Bolt On) | ||||||||
Black PTFE-Coated Aluminum | ||||||||
__ | M6 (4) | __ | __ | __ | 0.50 lbs. / 0.23 kg | 28 | 00000000 | 000000 |
__ | M8 (4) | __ | __ | __ | 0.47 lbs. / 0.22 kg | 28 | 00000000 | 000000 |
31.5 mm (ISO 31.5) | M5 × 0.8 mm (4) | 40 | __ | __ | 0.66 lbs. / 0.30 kg | 40 | 00000000 | 000000 |
40 mm (ISO 40) | M6 × 1 mm (4) | 50 | __ | __ | 0.67 lbs. / 0.31 kg | 40 | 00000000 | 000000 |
50 mm (ISO 50) | M6 × 1 mm (4) | 63 | __ | __ | 0.71 lbs. / 0.32 kg | 40 | 00000000 | 000000 |
Utility (Blank) | ||||||||
Black PTFE-Coated Aluminum | ||||||||
__ | __ | __ | __ | __ | 0.53 lbs. / 0.24 kg | 28 | 00000000 | 000000 |
Robot Vacuum Cup Mounts
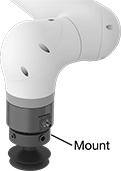
Attach threaded vacuum cups to robot arms with different ISO mounting patterns. These mounts have a universal thread for attaching your vacuum cups as well as inlet ports to connect air-powered vacuum pumps, so you can perform a variety of pick-and-place tasks. Use the 6-mm inlet port to move light objects or when working in tight spaces. Use the 10-mm inlet port to move heavy or porous objects, such as corrugated cartons. Made of acetal plastic, these mounts are strong, but lightweight, and stand up to moisture and chemicals. They include the hardware you need to connect them to robot arms. If you don't see your robot model number listed, measure the bolt circle diameter to determine mounting compatibility.
To preserve vacuum pressure, insert a 6-mm or 10-mm plug into the end of whichever inlet port you are not using.
Universal thread adapters let you join mounts and vacuum cups with different thread types.
Warning: Never use to lift people or items over people.
For technical drawings and 3-D models, click on a part number.
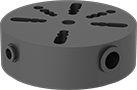
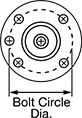
Robert Tool (Threaded) | End of Robot Arm (Bolt On) | |||||||||
---|---|---|---|---|---|---|---|---|---|---|
Pipe Size | Thread Lg. | No. of Threaded Holes | Bolt Circle Dia. (Mounting Hole Pattern Compatibility) | Mounting Fasteners Included | Wt. | Max. Load Cap. | Specifications Met | For Robot Arm Manufacturer (Series/Model Number) | Each | |
Black Acetal Plastic | ||||||||||
3/8 | 7/16" | 1 | 31.5 mm (ISO 31.5) 40 mm (ISO 40) 50 mm (ISO 50) 63 mm (ISO 63) | Yes | 0.4 lbs. / 0.18 kg | 55 lbs. / 25 kg | FDA Compliant 21 CFR 177.2470, FDA Compliant 21 CFR 177.2600 | ABB (IRB 120; IRB 1200; IRB 140; IRB 14000; IRB 14050; IRB 1410; IRB 1520ID; IRB 1600; IRB 1660ID; IRB 2400; IRB 2600; IRB 2600ID; IRB 360) FANUC (CR 4iA, 7iA; CRX 5iA, 10iA, 10iA/L, 20iA/L, 25iA; LR Mate 7L; M-10iD; M-20 iA) KUKA Robotics (KR 10 R1100-2) Omron (TM 5, 12, 14) Precise Automation (PAVP6; PF3400; PF 400; PP100) Productive Robotics (OB7) Staubli (TX2 90) Universal Robots (UR3; UR3e; UR5; UR5e; UR10; UR10e; UR16; UR16e) Yaskawa/Motoman (GP 7, 8, 12, 25; MH 3BM, 3F, 5LS II, 5S II, JF; MPP 3H, 3S; HC 10T; SIA 10D, 10F, 20D, 20F; MotoMini) | 0000000 | 0000000 |
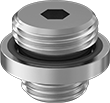
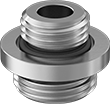
Pipe Size | Thread Type | Thread Length | |||||||||||
---|---|---|---|---|---|---|---|---|---|---|---|---|---|
(A) | (B) | Thread Size (B) | (A) | (B) | (A) | (B) | Hex Size | OD | Tensile Strength, psi | Hardness | O-Ring Material | Each | |
304 Stainless Steel | |||||||||||||
3/8 | __ | 10-32, M5 | BSPP, BSPT, NPT, NPTF, Universal | BSPP, BSPT, NPT, NPTF, Metric, UNF, Universal | 0.25" | 13/64" | 13/64" | 27/32" | 73,000 | Rockwell B70 | Buna-N Rubber | 00000000 | 000000 |
3/8 | 1/4 | __ | BSPP, BSPT, NPT, NPTF, Universal | BSPP, BSPT, NPT, NPTF, Universal | 0.25" | 1/4" | 13/64" | 27/32" | 73,000 | Rockwell B70 | Buna-N Rubber | 00000000 | 00000 |
3/8 | 1/8 | __ | BSPP, BSPT, NPT, NPTF, Universal | BSPP, BSPT, NPT, NPTF, Universal | 0.25" | 1/4" | 13/64" | 27/32" | 73,000 | Rockwell B70 | Buna-N Rubber | 00000000 | 00000 |
3/8 | 3/8 | __ | BSPP, BSPT, NPT, NPTF, Universal | BSPP, BSPT, NPT, NPTF, Universal | 0.25" | 1/4" | 13/64" | 27/32" | 73,000 | Rockwell B70 | Buna-N Rubber | 00000000 | 00000 |
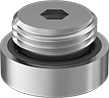
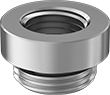
Pipe Size | Thread Type | Thread Length | |||||||||||
---|---|---|---|---|---|---|---|---|---|---|---|---|---|
(A) | (B) | Thread Size (B) | (A) | (B) | (A) | (B) | Hex Size | OD | Tensile Strength, psi | Hardness | O-Ring Material | Each | |
304 Stainless Steel | |||||||||||||
3/8 | __ | 10-32, M5 | BSPP, BSPT, NPT, NPTF, Universal | BSPP, BSPT, NPT, NPTF, Metric, UNF, Universal | 0.25" | 9/64" | 13/64" | 27/32" | 73,000 | Rockwell B70 | Buna-N Rubber | 00000000 | 000000 |
3/8 | 1/4 | __ | BSPP, BSPT, NPT, NPTF, Universal | BSPP, BSPT, NPT, NPTF, Universal | 0.25" | 1/4" | 13/64" | 27/32" | 73,000 | Rockwell B70 | Buna-N Rubber | 00000000 | 00000 |
3/8 | 1/8 | __ | BSPP, BSPT, NPT, NPTF, Universal | BSPP, BSPT, NPT, NPTF, Universal | 0.25" | 1/4" | 13/64" | 27/32" | 73,000 | Rockwell B70 | Buna-N Rubber | 00000000 | 00000 |
Automatic Robot Tool Changers
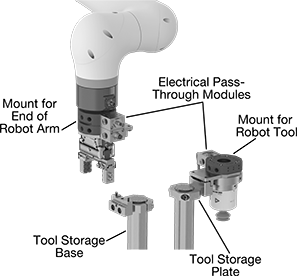
No need to manually latch and unlatch end-of-arm tools, these tool changers will quickly and seamlessly swap them out for you. While manual tool changers are good for switching tools in between two different work cycles, these automatic tool changers are best for making multiple changes in a single work cycle.
A complete assembly consists of an end-of-robot-arm mount and a robot-tool mount (each sold separately) that lock together with air-powered latching cams. While you’ll only need one end-of-robot-arm mount for your robot arm, make sure you have a robot-tool mount for each of your tools. All of these mounts have standard ISO mounting hole patterns, so they’re compatible with the mounting hole patterns on most robot arms and tools. If you don't see your robot model number listed, measure the bolt circle diameter to determine mounting compatibility.
All of these mounts have air connections, so you can use compressed air to operate air-powered tools, such as grippers. They also have connections for adding electrical pass-through modules (sold separately) to power electrically controlled tools.
To create a tool docking system, use tool storage plates with tool storage bases and tool presence detectors, so tool changers can pick tools up or drop them off as they are needed.
For technical drawings and 3-D models, click on a part number.
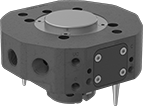
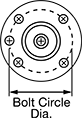
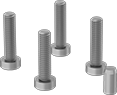
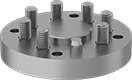
End-of-robot-arm mounts with a coupling indicator use electrical signals to send information about the position of the latching cams to your controller, letting you know if your robot-tool mount and end-of-robot-arm mount are locked in place. It does not, however, let you know if the robot-tool mount is present.
Adapter plates let you join arms and tools with different mounting hole patterns. If you have a robot arm with ISO 40 mounting hole patterns, choose the ISO 50 mount with the adapter plate for mounting hole compatibility.
Mounts | Adapter Plates for ISO 40 Robot Arms | Hardware Kits | ||||||||||
---|---|---|---|---|---|---|---|---|---|---|---|---|
Bolt Circle Dia. (Mounting Hole Pattern Compatibility) | Bolt Hole Thread Size (No. of) | Mounting Hardware Included | Lg., mm | Max. Load Cap. | Wt. | For Robot Arm Manufacturer (Series/Model Number) | Each | Each | Each | |||
Anodized Aluminum | ||||||||||||
50 mm (ISO 50) | M6 × 1.0 mm (4) | No | 27.5 | 55 lbs. / 25 kg | 0.84 lbs. / 0.38 kg | ABB (IRB 2400; IRB 2600) FANUC (CRX 5iA, 10iA, 10iA/L, 20iA/L, 25iA) Omron (TM 5, 12, 14) Productive Robotics (OB7) Staubli (TX2 90) Universal Robots (UR3; UR3e; UR5; UR5e; UR10; UR10e; UR16; UR16e) | 0000000 | 000000000 | 0000000 | 0000000 | 0000000 | 000000 |
Anodized Aluminum—With Coupling Indicator | ||||||||||||
50 mm (ISO 50) | M6 × 1.0 mm (4) | No | 27.5 | 55 lbs. / 25 kg | 0.84 lbs. / 0.38 kg | ABB (IRB 2400; IRB 2600) FANUC (CRX 5iA, 10iA, 10iA/L, 20iA/L, 25iA) Omron (TM 5, 12, 14) Productive Robotics (OB7) Staubli (TX2 90) Universal Robots (UR3; UR3e; UR5; UR5e; UR10; UR10e; UR16; UR16e) | 0000000 | 00000000 | 0000000 | 000000 | 0000000 | 00000 |
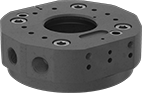
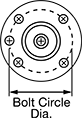
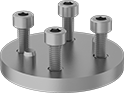
Robot-tool mounts that have ISO 50 and ISO 63 mounting hole patterns match a variety of tools without having to buy a separate adapter. Those with a tool storage plate come with a built-in plate, so tool changers can pick tools up or drop them off as they are needed.
Use blank adapter plates to machine custom mounting hole patterns.
Mounts | Blank Adapter Plates | ||||||||
---|---|---|---|---|---|---|---|---|---|
Bolt Circle Dia. (Mounting Hole Pattern Compatibility) | Bolt Hole Thread Size (No. of) | Mounting Hardware Included | Lg., mm | Max. Load Cap. | Wt. | Each | Each | ||
Anodized Aluminum | |||||||||
50 mm (ISO 50) 63 mm (ISO 63) | M6 × 1.0 mm (4) M6 × 1.0 mm (4) | No | 28.5 | 55 lbs. / 25 kg | 0.46 lbs. / 0.21 kg | 0000000 | 0000000 | 000000 | 00 |
Anodized Aluminum—With Tool Storage Plate | |||||||||
50 mm (ISO 50) 63 mm (ISO 63) | M6 × 1.0 mm (4) M6 × 1.0 mm (4) | No | 63.5 | 55 lbs. / 25 kg | 0.46 lbs. / 0.21 kg | 0000000 | 00000000 | 0000000 | 0000000 |
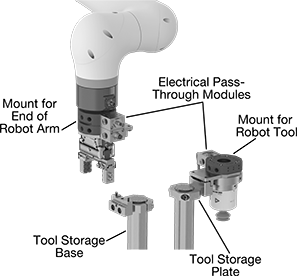

Pass-Through Module for
End-of-Robot-Arm Mounts
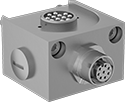
Pass-Through Module
for Robot-Tool Mounts

Electrical pass-through modules pass electrical signals from your robot, through the tool changer, to your tools. You'll need one module for each tool. All have electrical connectors, wire leads, or terminals, so you can wire your own connectors. Modules with wire leads or terminals that feature strain relief do not come with a cable, but let you securely connect your own cable. Modules for FANUC (CRX) and Universal Robots are specifically wired to connect to those models.
Lg., mm | Wd., mm | Dp., mm | Mount Type | Mounting Fasteners Included | Wt. | Voltage | For Robot Arm Manufacturer (Series) | Material | Each | |
For End of Robot Arm Mounts with ISO 50/63 Mounting Pattern | ||||||||||
---|---|---|---|---|---|---|---|---|---|---|
8-Pole Micro M12 Plug | ||||||||||
30.9 | 46 | 51 | Bolt On | Yes | 0.21 lbs. / 0.1 kg | 250V AC / 250V DC | __ | Anodized Aluminum | 0000000 | 0000000 |
8-Pole M8 Socket | ||||||||||
30.9 | 46 | 49.9 | Bolt On | Yes | 0.25 lbs. / 0.11 kg | 250V AC / 250V DC | __ | Anodized Aluminum | 0000000 | 000000 |
30.9 | 46 | 60.6 | Bolt On | Yes | 0.21 lbs. / 0.1 kg | 250V AC / 250V DC | FANUC (CRX), Universal Robots | Anodized Aluminum | 0000000 | 000000 |
Tab Terminals with Strain Relief | ||||||||||
30.9 | 65.3 | 41 | Bolt On | Yes | 0.21 lbs. / 0.1 kg | 1,000V AC / 1,000V DC | __ | Anodized Aluminum | 0000000 | 000000 |
For Robot Tool Mounts with ISO 50/63 Mounting Pattern | ||||||||||
8-Pole M8 Plug | ||||||||||
28 | 46 | 49.9 | Bolt On | Yes | 0.21 lbs. / 0.1 kg | 250V AC / 250V DC | __ | Anodized Aluminum | 0000000 | 000000 |
8-Pole M12 Socket | ||||||||||
28 | 46 | 49.6 | Bolt On | Yes | 0.21 lbs. / 0.1 kg | 250V AC / 250V DC | __ | Anodized Aluminum | 0000000 | 000000 |
Tab Terminals with Strain Relief | ||||||||||
28 | 65.3 | 41 | Bolt On | Yes | 0.21 lbs. / 0.1 kg | 1,000V AC / 1,000V DC | __ | Anodized Aluminum | 0000000 | 000000 |
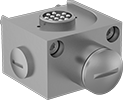
Tool identification modules let electrical pass-through modules (sold separately) know whether or not a tool is present. You’ll need one tool identification module for each tool—program your controller to recognize up to 15 different tools. These modules don't have a connection point for passing electrical signals to the robot tool.
Lg., mm | Wd., mm | Dp., mm | Mount Type | Mounting Fasteners Included | Wt. | Voltage | Material | Each | |
For Robot Tool Mounts with ISO 50/63 Mounting Pattern | |||||||||
---|---|---|---|---|---|---|---|---|---|
28 | 46 | 53 | Bolt On | Yes | 0.21 lbs. / 0.1 kg | 250V AC / 250V DC | Anodized Aluminum | 0000000 | 0000000 |
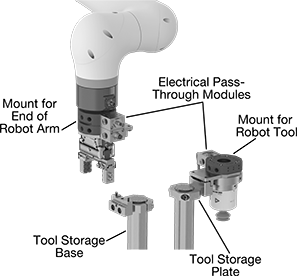
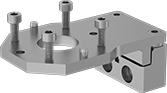
Tool storage plates consist of two pieces: the top piece mounts to your tool, which then rests on the bottom piece that mounts to the tool storage base. The top piece doubles as a blank plate, so you can machine custom mounting hole patterns.
Robot Tool | Tool Storage Base | ||||||||||||||
---|---|---|---|---|---|---|---|---|---|---|---|---|---|---|---|
Lg., mm | Wd., mm | Dp., mm | Mount Type | Bolt Circle Dia., mm | Bolt Hole Thread Size | No. of Bolt Holes | Mount Type | Bolt Hole Thread Size | No. of Bolt Holes | Mounting Fasteners Included | Max. Load Cap. | Wt. | Material | Each | |
For Robot Tool Mounts with ISO 50/63 Mounting Pattern | |||||||||||||||
53.5 | 73 | 115 | Bolt On | 63 | M6 × 1 mm | 4 | Bolt On | M8 × 1.25 mm | 2 | Yes | 110 lbs. / 50 kg | 0.69 lbs. / 0.31 kg | Anodized Aluminum | 0000000 | 0000000 |
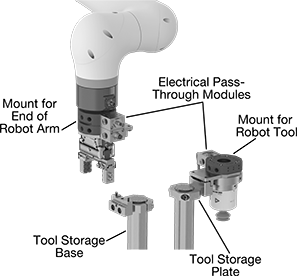

Tool storage bases keep your tools positioned for the tool changers to access them. Use them with a tool storage plate.
Base | Tool Storage Plate | Floor | |||||||||||
---|---|---|---|---|---|---|---|---|---|---|---|---|---|
Wd., mm | Dp., mm | Riser Ht., m | Mount Type | Bolt Hole Thread Size | No. of Bolt Holes | Mount Type | Bolt Hole Thread Size | No. of Bolt Holes | Mounting Fasteners Included | Wt. | Material | Each | |
70 | 73.5 | 1 | Bolt On | M8 × 1.25 mm | 2 | Bolt On | M8 × 1.25 mm | 4 | Yes | 5.1 lbs. / 2.3 kg | Anodized Aluminum | 0000000 | 0000000 |
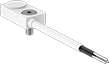
Often used in complex robotic applications, tool presence detectors have a proximity sensor that sends information to your controller. Detectors for end of robot arm mounts signal when a tool changer is in position for the cams to latch.
Voltage Range | Wire Connection Type | Wire Lead Lg., m | Signal Output Type | Mounting Fasteners Included | Wt. | Each | |
For End of Robot Arm Mounts | |||||||
---|---|---|---|---|---|---|---|
10-30V DC | Wire Leads | 2 | PNP | Yes | 0.04 lbs. / 0.02 kg | 0000000 | 0000000 |