About Composites
More
Flame- and Heat-Resistant Pads
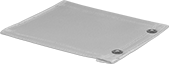
Prevent heat and flame damage in small spaces—these pads are a good alternative to large blankets during localized, high-heat applications. They are for intermittent contact with flames and hot surfaces.
Pads | ||||||||
---|---|---|---|---|---|---|---|---|
Wd. | Lg. | Thick., mil | Weight, oz. | Max. Temp., ° F | Clarity | Color | Each | |
Carbon Fiber | ||||||||
18" | 18" | 200 | 4 | 1800° | Opaque | Black | 0000000 | 000000 |
Ultra-Strength Lightweight Carbon Fiber Sheets and Bars
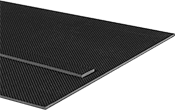
- Color: Black
- Temperature Range: See table
- Tensile Strength: 120,000-175,000 psi (Excellent)
- Fiber Tensile Stiffness: Standard (33-36 msi)
- Impact Strength: Not Rated
- Hardness: Not Rated
- For Use Outdoors: No
Known for its use in the aerospace industry, where a balance of weight and strength is critical, carbon fiber is now often machined into panels for structural framing, machinery components, and robotics. Use it in place of aluminum to reduce your application's weight without sacrificing much rigidity. Because these sheets and bars are lightweight, they reduce wear and stress on motorized parts, increasing the life of machinery.
Plain bars have fibers that are aligned in a single direction, making them strong in the direction of the fibers. They hold up to bending across the fibers but will splinter and separate like string cheese when bent along the length of the fiber.
Sheets and checked bars have layers that alternate fibers in two directions, so they spread out their strength across the entire sheet or bar. They have more structural integrity compared to plain bars.
Checked carbon fiber is easy to machine and will not fray or splinter when cut. It has the classic carbon-fiber look. Glossy carbon fiber can be sanded for a matte finish or to prep it for painting.
For technical drawings and 3-D models, click on a part number.
Thick. | Thick. Tolerance | Appearance | Min. Temp. | Max. Temp., °F | Each | |
6" × 6" | ||||||
---|---|---|---|---|---|---|
1/32" | -0.003" to 0.003" | Checked, Glossy | Not Rated | 180° | 0000000 | 000000 |
1/16" | -0.004" to 0.004" | Checked, Glossy | Not Rated | 180° | 0000000 | 00000 |
1/8" | -0.006" to 0.006" | Checked, Glossy | Not Rated | 180° | 00000000 | 00000 |
3/16" | -0.006" to 0.006" | Checked, Glossy | Not Rated | 180° | 0000000 | 00000 |
1/4" | -0.008" to 0.008" | Checked, Glossy | Not Rated | 180° | 0000000 | 00000 |
3/8" | -0.018" to 0.018" | Checked, Glossy | Not Rated | 180° | 0000000 | 00000 |
1/2" | -0.025" to 0.025" | Checked, Glossy | Not Rated | 180° | 00000000 | 00000 |
3/4" | -0.037" to 0.037" | Checked, Glossy | Not Rated | 180° | 00000000 | 000000 |
1" | -0.05" to 0.05" | Checked, Glossy | Not Rated | 180° | 00000000 | 000000 |
6" × 12" | ||||||
1/32" | -0.003" to 0.003" | Checked, Glossy | Not Rated | 180° | 0000000 | 00000 |
1/16" | -0.004" to 0.004" | Checked, Glossy | Not Rated | 180° | 0000000 | 00000 |
1/8" | -0.006" to 0.006" | Checked, Glossy | Not Rated | 180° | 00000000 | 00000 |
3/16" | -0.006" to 0.006" | Checked, Glossy | Not Rated | 180° | 0000000 | 00000 |
1/4" | -0.008" to 0.008" | Checked, Glossy | Not Rated | 180° | 0000000 | 00000 |
3/8" | -0.018" to 0.018" | Checked, Glossy | Not Rated | 180° | 0000000 | 000000 |
1/2" | -0.025" to 0.025" | Checked, Glossy | Not Rated | 180° | 00000000 | 000000 |
12" × 12" | ||||||
1/32" | -0.003" to 0.003" | Checked, Glossy | Not Rated | 180° | 0000000 | 00000 |
1/16" | -0.004" to 0.004" | Checked, Glossy | Not Rated | 180° | 0000000 | 00000 |
1/8" | -0.006" to 0.006" | Checked, Glossy | Not Rated | 180° | 0000000 | 00000 |
3/16" | -0.006" to 0.006" | Checked, Glossy | Not Rated | 180° | 0000000 | 000000 |
1/4" | -0.008" to 0.008" | Checked, Glossy | Not Rated | 180° | 0000000 | 000000 |
3/8" | -0.018" to 0.018" | Checked, Glossy | Not Rated | 180° | 0000000 | 000000 |
1/2" | -0.025" to 0.025" | Checked, Glossy | Not Rated | 180° | 00000000 | 000000 |
3/4" | -0.037" to 0.037" | Checked, Glossy | Not Rated | 180° | 00000000 | 000000 |
1" | -0.05" to 0.05" | Checked, Glossy | Not Rated | 180° | 00000000 | 000000 |
12" × 24" | ||||||
1/32" | -0.003" to 0.003" | Checked, Glossy | Not Rated | 180° | 0000000 | 00000 |
1/16" | -0.004" to 0.004" | Checked, Glossy | Not Rated | 180° | 0000000 | 000000 |
1/8" | -0.006" to 0.006" | Checked, Glossy | Not Rated | 180° | 0000000 | 000000 |
3/16" | -0.006" to 0.006" | Checked, Glossy | Not Rated | 180° | 0000000 | 000000 |
1/4" | -0.008" to 0.008" | Checked, Glossy | Not Rated | 180° | 0000000 | 000000 |
12" × 36" | ||||||
1/32" | -0.003" to 0.003" | Checked, Glossy | Not Rated | 180° | 0000000 | 000000 |
1/16" | -0.004" to 0.004" | Checked, Glossy | Not Rated | 180° | 0000000 | 000000 |
1/8" | -0.006" to 0.006" | Checked, Glossy | Not Rated | 180° | 00000000 | 000000 |
3/16" | -0.006" to 0.006" | Checked, Glossy | Not Rated | 180° | 0000000 | 000000 |
1/4" | -0.008" to 0.008" | Checked, Glossy | Not Rated | 180° | 0000000 | 000000 |
3/8" | -0.018" to 0.018" | Checked, Glossy | Not Rated | 180° | 0000000 | 000000 |
12" × 48" | ||||||
1/32" | -0.003" to 0.003" | Checked, Glossy | Not Rated | 180° | 0000000 | 000000 |
1/16" | -0.004" to 0.004" | Checked, Glossy | Not Rated | 180° | 0000000 | 000000 |
1/8" | -0.006" to 0.006" | Checked, Glossy | Not Rated | 180° | 00000000 | 000000 |
24" × 24" | ||||||
1/32" | -0.003" to 0.003" | Checked, Glossy | Not Rated | 180° | 0000000 | 000000 |
1/16" | -0.004" to 0.004" | Checked, Glossy | Not Rated | 180° | 0000000 | 000000 |
1/8" | -0.006" to 0.006" | Checked, Glossy | Not Rated | 180° | 0000000 | 000000 |
3/16" | -0.006" to 0.006" | Checked, Glossy | Not Rated | 180° | 0000000 | 000000 |
1/4" | -0.008" to 0.008" | Checked, Glossy | Not Rated | 180° | 0000000 | 000000 |
1/2" | -0.025" to 0.025" | Checked, Glossy | Not Rated | 180° | 00000000 | 00000000 |
3/4" | -0.037" to 0.037" | Checked, Glossy | Not Rated | 180° | 00000000 | 00000000 |
24" × 48" | ||||||
1/32" | -0.003" to 0.003" | Checked, Glossy | Not Rated | 180° | 0000000 | 000000 |
1/16" | -0.004" to 0.004" | Checked, Glossy | Not Rated | 180° | 0000000 | 000000 |
1/8" | -0.006" to 0.006" | Checked, Glossy | Not Rated | 180° | 00000000 | 000000 |
1/4" | -0.008" to 0.008" | Checked, Glossy | Not Rated | 180° | 0000000 | 00000000 |
3/8" | -0.018" to 0.018" | Checked, Glossy | Not Rated | 180° | 0000000 | 00000000 |
36" × 36" | ||||||
1/16" | -0.004" to 0.004" | Checked, Glossy | Not Rated | 180° | 00000000 | 000000 |
1/8" | -0.006" to 0.006" | Checked, Glossy | Not Rated | 180° | 00000000 | 000000 |
1/4" | -0.008" to 0.008" | Checked, Glossy | Not Rated | 180° | 0000000 | 00000000 |
12" Lg. | 24" Lg. | |||||
---|---|---|---|---|---|---|
Wd. | Min. Temp. | Max. Temp., °F | Each | Each | ||
1/32" Thick. (-0.003" to 0.003") | ||||||
1" | Not Rated | 180° | 0000000 | 00000 | 0000000 | 000000 |
2" | Not Rated | 180° | 0000000 | 0000 | 0000000 | 00000 |
3" | Not Rated | 180° | 0000000 | 00000 | 0000000 | 00000 |
1/16" Thick. (-0.004" to 0.004") | ||||||
1" | Not Rated | 180° | 0000000 | 0000 | 0000000 | 00000 |
2" | Not Rated | 180° | 0000000 | 00000 | 0000000 | 00000 |
3" | Not Rated | 180° | 0000000 | 00000 | 0000000 | 00000 |
1/8" Thick. (-0.006" to 0.006") | ||||||
1" | Not Rated | 180° | 0000000 | 00000 | 0000000 | 00000 |
2" | Not Rated | 180° | 0000000 | 00000 | 0000000 | 00000 |
3" | Not Rated | 180° | 0000000 | 00000 | 0000000 | 00000 |
3/16" Thick. (-0.006" to 0.006") | ||||||
1" | Not Rated | 180° | 0000000 | 00000 | 0000000 | 00000 |
2" | Not Rated | 180° | 0000000 | 00000 | 0000000 | 00000 |
3" | Not Rated | 180° | 0000000 | 00000 | 0000000 | 00000 |
1/4" Thick. (-0.008" to 0.008") | ||||||
1" | Not Rated | 180° | 00000000 | 00000 | 00000000 | 00000 |
2" | Not Rated | 180° | 00000000 | 00000 | 00000000 | 00000 |
3" | Not Rated | 180° | 00000000 | 00000 | 00000000 | 00000 |
3/8" Thick. (-0.018" to 0.018") | ||||||
1" | Not Rated | 180° | 00000000 | 00000 | 00000000 | 00000 |
2" | Not Rated | 180° | 00000000 | 00000 | 000000 | 00 |
3" | Not Rated | 180° | 00000000 | 00000 | 000000 | 00 |
1/2" Thick. (-0.025" to 0.025") | ||||||
1" | Not Rated | 180° | 00000000 | 00000 | 00000000 | 00000 |
2" | Not Rated | 180° | 00000000 | 00000 | 00000000 | 000000 |
3" | Not Rated | 180° | 00000000 | 00000 | 00000000 | 000000 |
3/4" Thick. (-0.037" to 0.037") | ||||||
2" | Not Rated | 180° | 00000000 | 00000 | 000000 | 00 |
1" Thick. (-0.05" to 0.05") | ||||||
1" | Not Rated | 180° | 00000000 | 00000 | 000000 | 00 |
2" | Not Rated | 180° | 00000000 | 000000 | 000000 | 00 |
3" | Not Rated | 180° | 00000000 | 000000 | 000000 | 00 |
Ultra-Strength Lightweight Carbon Fiber Sheets with Foam Core
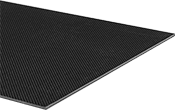
- Color: Black
- Temperature Range: 0° F to 250° F
- Tensile Strength: 120,000-175,000 psi (Excellent)
- Fiber Tensile Stiffness: Standard (33-36 msi)
- Impact Strength: Not Rated
- Hardness: Not Rated
- For Use Outdoors: No
A layer of foam is sandwiched between two pieces of carbon fiber to make these sheets even lighter than standard carbon fiber sheets. Carbon fiber is the strongest composite we offer. It’s comparable in strength to 6061 aluminum and is often used to build frames and structures.
For technical drawings and 3-D models, click on a part number.
12" × 12" | ||||
---|---|---|---|---|
Thickness | Thick. Tolerance | Appearance | Each | |
1/4" | -0.02" to 0.02" | Checked | 0000000 | 0000000 |
Distortion-Resistant Ultra-Strength Lightweight Carbon Fiber Sheets
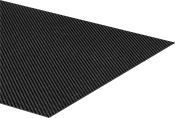
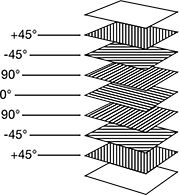
- Color: Black
- Maximum Temperature: 180° F
- Tensile Strength: Not Rated
- Fiber Tensile Stiffness: Standard (33-36 msi)
- Impact Strength: Not Rated
- Hardness: Not Rated
- For Use Outdoors: No
Layers of fibers alternating in four directions makes this carbon fiber stiff at the corners and edges, so it stands up to twisting forces. It also gives you the same stiffness as standard carbon fiber but in a thinner sheet, reducing the overall weight of your application. It's ideal for thin, strong parts—often substituted for aluminum because it's lighter in weight yet almost as rigid.
A checked pattern keeps the fibers from splintering when cut and gives these sheets the classic carbon fiber look. They're glossy but can be sanded for a matte finish.
For technical drawings and 3-D models, click on a part number.
Thickness | Thickness Tolerance | Appearance | Each | |
12" × 12" | ||||
---|---|---|---|---|
1/16" | -0.003" to 0.003" | Checked, Glossy | 0000000 | 000000 |
1/8" | -0.006" to 0.006" | Checked, Glossy | 0000000 | 000000 |
24" × 12" | ||||
1/16" | -0.003" to 0.003" | Checked, Glossy | 0000000 | 000000 |
1/8" | -0.006" to 0.006" | Checked, Glossy | 0000000 | 000000 |
24" × 24" | ||||
1/16" | -0.003" to 0.003" | Checked, Glossy | 0000000 | 000000 |
1/8" | -0.006" to 0.006" | Checked, Glossy | 0000000 | 000000 |
Rigid Ultra-Strength Lightweight Carbon Fiber Sheets
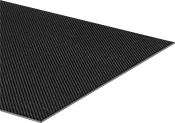
- Color: Black
- Maximum Temperature: 180° F
- Tensile Strength: 125,000-150,000 psi (Excellent)
- Impact Strength: Not Rated
- Hardness Rating: Not Rated
- For Use Outdoors: No
Almost as stiff as steel and a fraction of the weight, these carbon fiber sheets are often used for structural framing, machinery components, and robotics. Known for its use in the aerospace industry—where a balance of weight and strength is critical—carbon fiber is lightweight, so it reduces the stress and wear on motorized parts and extends the life of machinery. These sheets have layers that alternate fibers in two directions, so they resist bending at the edges.
The checked pattern on these sheets gives them a classic carbon-fiber look and makes them easy to machine because the pattern keeps fibers from splintering when the sheets are cut. They are matte, so they do not reflect light and are ready to paint.
For technical drawings and 3-D models, click on a part number.
Impact-Resistant Ultra-Strength Carbon Fiber Sheets with Kevlar Core
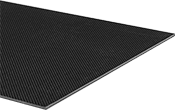
- Color: Black
- Temperature Range: -100° to 190° F
- Tensile Strength: 177,000 psi (Excellent)
- Impact Strength: Not Rated
- Hardness: Not Rated
- For Use Outdoors: No
Often used to build frames and structures, these lightweight sheets combine the strength and stiffness of carbon fiber with the impact resistance of Kevlar. With carbon fiber on the outer layers, these sheets are extremely difficult to bend—they’re nearly as stiff as pure carbon fiber. The carbon fiber layers also provide good strength under tension, comparable to 6061 aluminum. Sandwiched between the carbon fiber layers of these sheets is a Kevlar core. Known for its toughness, the Kevlar core helps prevent sheets from failing under a variety of stresses, such as punctures, cuts, impact, and wear. The Kevlar core also has a lower density than carbon fiber, making these sheets even lighter than sheets made from carbon fiber alone.
Sheets with 0.09 in. thickness have thicker layers of carbon fiber, making them stiffer than those with 0.06 in. thickness.
For technical drawings and 3-D models, click on a part number.
Easy-To-Form Ultra-Strength Chemical-Resistant
PAEK and Carbon Fiber Sheets
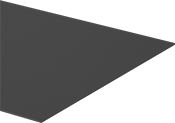
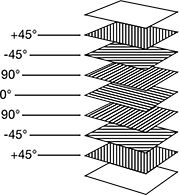
- Color: Black
- Maximum Temperature: 500° F
- Tensile Strength:
Bidirectional: 275,550 psi
Quasi-Isotropic: 94,850 psi - Impact Strength: Not Rated
- For Use Outdoors: No
Originally designed for the automotive and aerospace industries, these PAEK and carbon fiber sheets are a substitute for metal because they’re as light as aluminum and as strong as a nickel alloy. Their combination of high strength, light weight, chemical resistance, and thermal properties is unusual for a composite. High tension won’t break them apart and extreme compression won’t shrink or crack them. They’re also stiff and withstand abrasions and dents from heavy loads. Cleaning and degreasing chemicals, such as acetone and isopropyl alcohol, won’t damage them. Unlike most composites, they’re recyclable too.
Form these sheets into the shapes you need using heat and pressure. Compared to PEEK composites, they don’t need as high of a curing temperature to thermoform them, so they save you time and energy. Different from composites made with adhesives and epoxies, which you must machine, layer, and cure, you can repeatedly and quickly heat and form these sheets without hurting their strength or chemical resistance. However, they will soften if the operating temperature exceeds 500° F—a higher maximum temperature than other thermoformable composites.
Quasi-isotropic sheets have extra rigid corners to resist bending and pulling in any direction. Though, they’re not as good at resisting force in one direction as bidirectional sheets.
For technical drawings and 3-D models, click on a part number.
Thickness | Thickness Tolerance | Appearance | Each | |
12" × 12" | ||||
---|---|---|---|---|
Quasi-Isotropic | ||||
0.044" | -0.004" to 0.004" | Plain | 0000000 | 0000000 |
0.088" | -0.009" to 0.009" | Plain | 0000000 | 000000 |
16" × 16" | ||||
Bidirectional | ||||
0.066" | -0.007" to 0.007" | Plain | 0000000 | 000000 |
24" × 24" | ||||
Quasi-Isotropic | ||||
0.044" | -0.004" to 0.004" | Plain | 0000000 | 00000000 |
0.088" | -0.009" to 0.009" | Plain | 0000000 | 00000000 |
32" × 32" | ||||
Bidirectional | ||||
0.066" | -0.007" to 0.007" | Plain | 0000000 | 00000000 |
Composite Fabrics
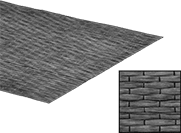
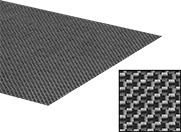
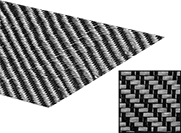
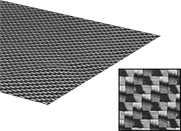
Use these resin-free fabrics to reinforce or repair existing composites as well as create new composites. Mold custom-shaped composite parts by layering your choice of fabric with an epoxy. The epoxy (sold separately) is a two-part resin that begins to harden in 15 hours and reaches full strength in 4 days. Finished composite pieces withstand temperatures up to 250° or 350° F.
Fabrics with a unidirectional weave have most of their fibers running in one direction. This weave is preferred when making tubular parts, such as vehicle frames, where linear strength and rigidity are required. Often referred to as nonwoven fabrics, these fabrics are best for reinforcing applications. However, they’re hard to machine because they may splinter.
Fabrics with a plain, twill, or triaxial weave have fibers that are woven in alternating directions for uniform strength and rigidity in all directions. Easier to machine than fabrics with a unidirectional weave, their woven pattern holds the fibers together to limit splintering. Plain-weave fabrics are more rigid and maintain their shape better than twill-weave fabrics. However, they are not as strong and easy to manipulate as twill- and triaxial-weave fabrics. Twill-weave fabrics are stronger than plain-weave fabrics. They’re also more flexible, making them easier to manipulate into complex shapes. They will not, however, retain their shape as well as plain-weave fabrics. Triaxial-weave fabrics are stronger and more rigid than plain- and twill-weave fabrics. They’re often used to reinforce or create thin composites since you won’t have to use as many layers to achieve high strength. Although they are easier to manipulate than plain-weave fabrics, they are not as flexible as twill-weave fabrics for making complex shapes.
Carbon-fiber fabrics have the highest strength of all our composite fabrics.
48" × 36" | 50" × 36" | |||||||
---|---|---|---|---|---|---|---|---|
Material | Color | Thick. | Fiber Tensile Stiffness | For Use Outdoors | Each | Each | ||
Unidirectional Weave | ||||||||
Carbon Fiber | Black | 0.014" | Standard (33-36 msi) | No | 000000 | 00 | 0000000 | 0000000 |
Plain Weave | ||||||||
Carbon Fiber | Black | 0.012" | Standard (33-36 msi) | No | 000000 | 00 | 0000000 | 000000 |
Twill Weave | ||||||||
Carbon Fiber | Black | 0.012" | Standard (33-36 msi) | No | 000000 | 00 | 0000000 | 000000 |
Carbon Fiber | Black | 0.025" | Standard (33-36 msi) | No | 000000 | 00 | 0000000 | 000000 |
Triaxial Weave | ||||||||
Carbon Fiber | Black | 0.027" | Standard (33-36 msi) | No | 0000000 | 0000000 | 000000 | 00 |
Epoxy—5:1 Mix Ratio (1 gal. metal can and 0.86 qt. metal can) | 0000000 | Each | 0000000 |