Air-Powered Grippers

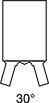
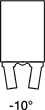
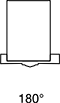

Combine these grippers with your gripping fingers to lift and move items in pick-and-place applications.
Angular grippers allow a more secure grip on irregularly shaped loads. Grippers with a spring jaw return have a single air port to close the jaws and grip items from the outside. An internal spring opens the jaws to release the grip. Grippers with a forced-air jaw return have two air ports: one to move the jaws open and another to move them closed. The jaws grip items from the outside as well as the inside.
Grippers with steel jaws are harder and stronger than aluminum. IP67-rated grippers are dust tight and can be submerged in up to 1 meter of water for 30 minutes.
Note: Choose a gripper with a holding force at least 10 times your item's weight.
Warning: Never use to lift people or items over people.

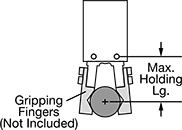
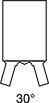
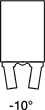
Angle | O'all | Port | ||||||||||||
---|---|---|---|---|---|---|---|---|---|---|---|---|---|---|
External Gripping Force | Max. Gripping Cap. | Max. | Min. | Max. Holding Lg., mm | Wt. | Lg., mm | Wd., mm | Dp., mm | Max. Pressure, psi | Thread Size | Thread Type | Manufacturer (Series/Model No.) | Each | |
Aluminum Housing | ||||||||||||||
0.9 lbs. @ 72.5 psi | 0.04 lbs. / 0.02 kg | 30° | -10° | 29 | 0.09 lbs./ 0.04 kg | 53 | 23 | 17 | 85 | M3 × 0.5 | Metric | SMC (MHC2 10) | 0000000 | 0000000 |
3.4 lbs. @ 72.5 psi | 0.17 lbs. / 0.07 kg | 30° | -10° | 39 | 0.21 lbs./ 0.1 kg | 62 | 30 | 24 | 85 | M5 × 0.8 | Metric | SMC (MHC2 16) | 0000000 | 000000 |
6.3 lbs. @ 72.5 psi | 0.31 lbs. / 0.14 kg | 30° | -10° | 59 | 0.41 lbs./ 0.19 kg | 79 | 42 | 28 | 85 | M5 × 0.8 | Metric | SMC (MHC2 20) | 0000000 | 000000 |
12.6 lbs. @ 72.5 psi | 0.63 lbs. / 0.28 kg | 30° | -10° | 80 | 0.7 lbs./ 0.32 kg | 93 | 52 | 34 | 85 | M5 × 0.8 | Metric | SMC (MHC2 25) | 0000000 | 000000 |

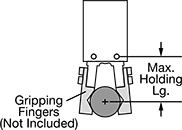
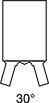
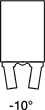
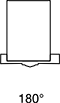

Angle | O'all | Port | ||||||||||||||
---|---|---|---|---|---|---|---|---|---|---|---|---|---|---|---|---|
External Gripping Force | Internal Gripping Force | Max. Gripping Cap. | Max. | Min. | Max. Holding Lg., mm | Wt. | Lg., mm | Wd., mm | Dp., mm | Max. Pressure, psi | Pipe Size | Thread Size | Thread Type | Manufacturer (Series/Model No.) | Each | |
Aluminum Housing | ||||||||||||||||
14.6 lbs. @ 72.5 psi | 14.6 lbs. @ 72.5 psi | 0.73 lbs./ 0.33 kg | 30° | -10° | 80 | 0.7 lbs./ 0.32 kg | 93 | 52 | 34 | 85 | __ | M5 × 0.8 | Metric | SMC (MHC2 25) | 0000000 | 0000000 |
2.5 lbs. @ 72.5 psi | 2.5 lbs. @ 72.5 psi | 0.12 lbs./ 0.05 kg | 30° | -10° | 29 | 0.09 lbs./ 0.04 kg | 53 | 23 | 17 | 85 | __ | M3 × 0.5 | Metric | SMC (MHC2 10) | 0000000 | 000000 |
7.6 lbs. @ 72.5 psi | 7.6 lbs. @ 72.5 psi | 0.38 lbs./ 0.17 kg | 30° | -10° | 39 | 0.21 lbs./ 0.1 kg | 62 | 30 | 24 | 85 | __ | M5 × 0.8 | Metric | SMC (MHC2 16) | 0000000 | 000000 |
9.5 lbs. @ 72.5 psi | 9.5 lbs. @ 72.5 psi | 0.47 lbs./ 0.21 kg | 30° | -10° | 59 | 0.4 lbs./ 0.18 kg | 79 | 42 | 28 | 85 | __ | M5 × 0.8 | Metric | SMC (MHC2 20) | 0000000 | 000000 |
Aluminum Housing—IP67-Rated | ||||||||||||||||
40 lbs. @ 85 psi | __ | 1.98 lbs./ 0.9 kg | 180° | 0° | 50 | 1.1 lbs./ 0.5 kg | 116 | 60 | 45 | 90 | __ | M5 × 0.8 | Metric | Schunk (DRG 200) | 0000000 | 00000000 |
64 lbs. @ 85 psi | __ | 3.3 lbs./ 1.5 kg | 180° | 0° | 60 | 1.69 lbs./ 0.77 kg | 133 | 70 | 52 | 90 | __ | M5 × 0.8 | Metric | Schunk (DRG 54) | 0000000 | 00000000 |
100 lbs. @ 85 psi | __ | 5.29 lbs./ 2.4 kg | 180° | 0° | 80 | 2.53 lbs./ 1.15 kg | 155 | 84 | 57 | 90 | __ | M5 × 0.8 | Metric | Schunk (DRG 64) | 0000000 | 00000000 |
135 lbs. @ 85 psi | __ | 7.05 lbs./ 3.2 kg | 180° | 0° | 100 | 4.4 lbs./ 2 kg | 183 | 100 | 72 | 90 | __ | M5 × 0.8 | Metric | Schunk (DRG 80) | 0000000 | 00000000 |
310 lbs. @ 85 psi | __ | 15.87 lbs./ 7.2 kg | 180° | 0° | 125 | 9.8 lbs./ 4.46 kg | 247 | 130 | 90 | 90 | 1/8 | __ | BSPP | Schunk (DRG 100) | 0000000 | 00000000 |
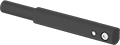
Add optional sensors to your gripper to signal when fingers are either open or closed (open and closed for sensors with two-position detection), and use that information to trigger other actions in your system. Since they’re magnetic, they detect the finger position using magnets placed on the piston.
Sensors with a plug connection work with the input/output on robot tool mounts with a power/signal block. Sensors with a hardwire connection have wire leads you either wire to a plug or hardwire to a power source.
NPN sensors communicate proximity with a negative signal, while PNP sensors send a positive signal.
Sensors with two-position detection send a signal when the fingers open and close, so you can trigger actions in your system based on both signals.
For Manufacturer (Series) | Signal Output Type | No. of Sensing Positions | Plug Type | No. of Wire Leads | Current, mA | Voltage | Switch Starting Position | Each | |
Magnetic with Plug Connection | |||||||||
---|---|---|---|---|---|---|---|---|---|
Schunk (DPG+, DPZ+, DRG, JGP, JGP-P, JGZ, KGG, MPG+, PGN+E) | NPN | 1 | 3-Pin M8 | __ | 50 | 24V DC | 1 Off (Normally Open) | 00000000 | 0000000 |
Schunk (DPG+, DPZ+, DRG, JGP, JGP-P, JGZ, KGG, MPG+, PGN+E) | PNP | 1 | 3-Pin M8 | __ | 50 | 24V DC | 1 Off (Normally Open) | 0000000 | 000000 |
Schunk (DPG+, DPZ+, DRG, JGP, JGP-P, JGZ, KGG, MPG+, PGN+E) | PNP | 2 | 4-Pin M8 | __ | 100 | 24V DC | 1 Off (Normally Open) and 1 On (Normally Closed) | 00000000 | 000000 |
Magnetic with Hardwire Connection | |||||||||
Schunk (DPG+, DPZ+, DRG, JGP, JGP-P, JGZ, KGG, MPG+, PGN+E) | NPN | 1 | __ | 3 | 50 | 24V DC | 1 Off (Normally Open) | 00000000 | 000000 |
Schunk (DPG+, DPZ+, DRG, JGP, JGP-P, JGZ, KGG, MPG+, PGN+E) | PNP | 1 | __ | 3 | 50 | 24V DC | 1 Off (Normally Open) | 00000000 | 000000 |
Schunk (DPG+, DPZ+, DRG, JGP, JGP-P, JGZ, KGG, MPG+, PGN+E) | PNP | 2 | __ | 4 | 100 | 24V DC | 1 Off (Normally Open) and 1 On (Normally Closed) | 00000000 | 000000 |
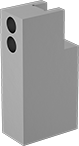
Finger blanks come ready to mount, so you can make custom fingers without starting from scratch. Just machine the blank’s gripping end to create fingers that will securely grip your specific parts.
When used in pairs, individual blanks have a symmetrical design that’s suitable for most applications.
Aluminum blanks are lightweight and resist rusting in wet environments. They’re softer than steel blanks, making them easier to machine and less likely to scratch your parts.
Steel blanks are stronger and more durable than aluminum blanks, so they’re less likely to break if they hit a nearby object. You can harden them for even more strength and durability.
For Gripper Jaw | Overall | |||||||
---|---|---|---|---|---|---|---|---|
For Manufacturer (Series/Model No.) | Wd., mm | Dp., mm | Lg., mm | Wd., mm | Dp., mm | Mounting Hardware Included | Each | |
Aluminum | ||||||||
SMC (MHC2 10) | 4 | 6.4 | 45 | 18 | 13 | Yes | 00000000 | 000000 |
SMC (MHC2 16) | 7 | 8 | 45 | 28 | 15 | Yes | 00000000 | 00000 |
SMC (MHC2 20) | 8 | 10 | 65 | 34 | 19 | Yes | 00000000 | 00000 |
SMC (MHC2 25) | 10 | 12 | 80 | 42 | 23 | Yes | 00000000 | 00000 |
Steel | ||||||||
SMC (MHC2 10) | 4 | 6.4 | 45 | 14 | 7 | Yes | 00000000 | 00000 |
SMC (MHC2 16) | 7 | 8 | 45 | 21 | 8 | Yes | 00000000 | 00000 |
SMC (MHC2 20) | 8 | 10 | 65 | 26 | 10 | Yes | 00000000 | 00000 |
SMC (MHC2 25) | 10 | 12 | 80 | 32 | 12 | Yes | 00000000 | 000000 |
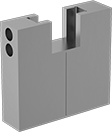
Finger blanks come ready to mount, so you can make custom fingers without starting from scratch. Just machine the blank’s gripping end to create fingers that will securely grip your specific parts.
Uncut pair blanks can be cut off center, making them good for applications where symmetrical fingers may hit nearby objects, such as when moving around machine spindles and parts trays during machine tending.
Aluminum blanks are lightweight and resist rusting in wet environments. They’re softer than steel blanks, making them easier to machine and less likely to scratch your parts.
Robot-Ready Electric Soft Grippers
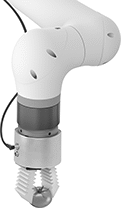
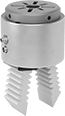
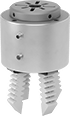
Mimicking a human hand, these grippers have soft, flexible silicone fingers that curl around items to pick them up. Unlike standard grippers with rigid fingers, these grippers can grasp fruit, bagged items, and other delicate objects without crushing them. They are powered and actuated entirely by your robot, so there's no need for an air supply or control valves. Connect them to terminals on your robot controller with the included 9 1/2 ft. electrical cord. A simple toggle on your controller’s digital outputs opens and closes the fingers. Mount them to most robot arms, like FANUC CRX and Universal Robots arms, thanks to their mounting slots that match a variety of ISO mounting patterns.
To program their range of motion and position, you’ll have access to a simple web-based interface from any smartphone or laptop. You don’t have to worry about hooking these up to your network. They generate their own wireless network like a hotspot, so you can connect your device to the setup interface to program them. If you are using these grippers with a Universal Robots arm, you can download a URCap plugin from the manufacturer's website for user-friendly control through your teach pendant software.
The fingers are made of FDA-compliant silicone for direct contact with food.
Grippers with fixed grip force apply the same amount of force every time. This helps them pick up most items successfully.
Grippers with adjustable grip force are the best choice to grip extremely sensitive items, such as baked goods or fragile glassware, because you can fine-tune the gripping force. These grippers also have part confirmation, which means they can send a signal to one of your robot controller's digital inputs to tell it whether a part has been successfully picked up. If the pickup fails, you can program your robot to try the pickup again.
2-finger grippers are good at picking up objects with uniform shapes, such as bottles and boxes.
4-finger grippers are a good choice if you plan to pick up irregularly shaped objects and need additional points of contact for a secure hold. They work well with fruits and vegetables, fabrics and flexible packaging.
Finger covers (sold separately) protect the gripper fingers from residue left from the material you're picking. These silicone covers slide over the fingers for picking and slide off for cleaning. They are FDA compliant for direct contact with food.
Stroke width describes the maximum total change in distance between fingers when the gripper actuates.
O'all | ||||||||||
---|---|---|---|---|---|---|---|---|---|---|
Finger Configuration | External Gripping Force, lbs. | Max. Gripping Cap. | Cycles per Sec. | Stroke Wd., mm | Max. Finger Spacing, mm | Mounting Hole Pattern Compatibility | Dia., mm | Lg., mm | Each | |
Aluminum Housing and Silicone Rubber Fingers | ||||||||||
2-Finger | 1.1 | 3.3 lbs. / 1.5 kg | 1 | 0-175 | 175 | ISO 31.5 ISO 40 ISO 50 ISO 63 | 105 | 172 | 00000000 | 000000000 |
4-Finger | 1.1 | 3.3 lbs. / 1.5 kg | 1 | 0-190 | 190 | ISO 31.5 ISO 40 ISO 50 ISO 63 | 119 | 187 | 00000000 | 00000000 |
O'all | ||||||||||
---|---|---|---|---|---|---|---|---|---|---|
Finger Configuration | External Gripping Force Range, lbs. | Max. Gripping Cap. | Cycles per Sec. | Stroke Wd., mm | Max. Finger Spacing, mm | Mounting Hole Pattern Compatibility | Dia., mm | Lg., mm | Each | |
Aluminum Housing and Silicone Rubber Fingers | ||||||||||
2-Finger | 0.23-1.1 | 3.3 lbs. / 1.5 kg | 1 | 0-175 | 175 | ISO 31.5 ISO 40 ISO 50 ISO 63 | 105 | 172 | 00000000 | 000000000 |
4-Finger | 0.23-1.1 | 3.3 lbs. / 1.5 kg | 1 | 0-190 | 190 | ISO 31.5 ISO 40 ISO 50 ISO 63 | 119 | 187 | 00000000 | 00000000 |