About Gears
More
Speed Reducers for Position- and Speed-Control Motors
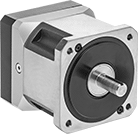
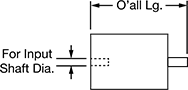
Pair these speed reducers with stepper and servo motors in position- and speed-control applications. Helical gears provide exact positioning and smoother travel than our other speed reducers. Attach to a motor to transmit motion parallel to the motor shaft while reducing speed and increasing torque. They meet IP65 for protection from washdowns.
Radial loads are loads that are perpendicular to the shaft. They’re commonly caused by components attached to shaft, such as pulleys and sprockets.
For technical drawings and 3-D models, click on a part number.
Max. Output | Max. Input | Output Shaft | Overall | |||||||||||
---|---|---|---|---|---|---|---|---|---|---|---|---|---|---|
Speed Ratio | Torque | Speed, rpm | Speed, rpm | hp | For Input Shaft Dia. | Dia. | Lg. | Lg. | Wd. | Ht. | Radial Load Capacity, lbs. | Environmental Rating | Each | |
For NEMA 23 Motor | ||||||||||||||
3:1 | 240 in.-lbs. @ 1,750 rpm | 2,000 | 6,000 | 2.89 | 1/4" | 0.38" | 1" | 4 1/2" | 2 1/2" | 2 1/2" | 348 | IP65 | 00000000 | 000000000 |
5:1 | 345 in.-lbs. @ 1,750 rpm | 1,200 | 6,000 | 3.24 | 1/4" | 0.38" | 1" | 4 1/2" | 2 1/2" | 2 1/2" | 348 | IP65 | 00000000 | 00000000 |
10:1 | 265 in.-lbs. @ 1,750 rpm | 600 | 6,000 | 1.45 | 1/4" | 0.38" | 1" | 4 1/2" | 2 1/2" | 2 1/2" | 348 | IP65 | 00000000 | 00000000 |
20:1 | 345 in.-lbs. @ 1,750 rpm | 300 | 6,000 | 1.08 | 1/4" | 0.38" | 1" | 5 3/4" | 2 1/2" | 2 1/2" | 348 | IP65 | 00000000 | 00000000 |
50:1 | 345 in.-lbs. @ 1,750 rpm | 120 | 6,000 | 0.46 | 1/4" | 0.38" | 1" | 5 3/4" | 2 1/2" | 2 1/2" | 348 | IP65 | 00000000 | 00000000 |
For NEMA 34 Motor | ||||||||||||||
3:1 | 743 in.-lbs. @ 1,750 rpm | 1,833 | 5,500 | 6.75 | 1/2" | 1/2" | 1.25" | 5 1/4" | 3 1/2" | 3 1/2" | 630 | IP65 | 00000000 | 00000000 |
5:1 | 867 in.-lbs. @ 1,750 rpm | 1,100 | 5,500 | 5.73 | 1/2" | 1/2" | 1.25" | 5 1/4" | 3 1/2" | 3 1/2" | 630 | IP65 | 00000000 | 00000000 |
10:1 | 797 in.-lbs. @ 1,750 rpm | 550 | 5,500 | 3.04 | 1/2" | 1/2" | 1.25" | 5 1/4" | 3 1/2" | 3 1/2" | 630 | IP65 | 00000000 | 00000000 |
20:1 | 867 in.-lbs. @ 1,750 rpm | 275 | 5,500 | 1.97 | 1/2" | 1/2" | 1.25" | 7" | 3 1/2" | 3 1/2" | 630 | IP65 | 00000000 | 00000000 |
50:1 | 867 in.-lbs. @ 1,750 rpm | 110 | 5,500 | 0.87 | 1/2" | 1/2" | 1.25" | 7" | 3 1/2" | 3 1/2" | 630 | IP65 | 00000000 | 00000000 |
High-Power Metal Gears
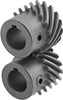
and Crossed Left-Hand
Gear (Sold Separately)
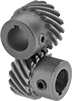
Right-Hand Teeth
(Sold Separately)
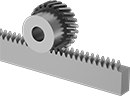

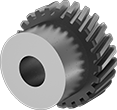
The helical teeth on these gears stay in contact for longer than straight teeth, which allows them to transmit higher loads at higher speeds than spur gears.
For gears to mesh correctly, they must have the same pressure angle and pitch. All of these gears transmit motion in a straight line—make sure to get one left-hand and one right-hand gear. To change speed and torque in your assembly, pair two gears with different numbers of teeth.
Parallel helical components have a 21 1/2° helix angle so they only transmit motion in a straight line since the helix angle is so small. Made from alloy steel, these gears resist abrasion and are stronger than carbon steel gears. Their teeth are ground, so they're more precise than gears with rolled teeth. Pair them with a rack or a gear that has a different tooth direction.
Crossed helical gears, also known as screw gears, can be configured to transmit motion at a 90° angle. To transmit motion at a 90° angle, pair two gears with the same tooth direction. To avoid wearing down gears, which happens when you use the same material, we recommend mating gears with different materials. Made from carbon steel, these gears are strong, but not as strong as alloy steel gears.
Gears with hardened teeth have better wear resistance than gears with teeth that are not hardened.
For technical drawings and 3-D models, click on a part number.
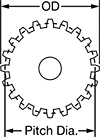
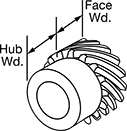
Hub | Keyway | ||||||||||||||
---|---|---|---|---|---|---|---|---|---|---|---|---|---|---|---|
Gear Pitch | Number of Teeth | Helix Angle | Gear Pitch Dia. | OD | Face Wd. | Overall Wd. | For Shaft Dia. | Teeth Heat Treatment | Dia. | Wd. | Wd. | Dp. | Set Screw Thread Size | Each | |
Left Hand | |||||||||||||||
Keyed Bore with Set Screw—1137 Carbon Steel | |||||||||||||||
16 | 16 | 45° | 1" | 1.09" | 1/2" | 1" | 1/2" | Hardened | 0.86" | 0.5" | 0.125" | 0.062" | 1/4"-20 | 0000000 | 000000 |
16 | 24 | 45° | 1 1/2" | 1.59" | 1/2" | 1" | 5/8" | Hardened | 1.37" | 0.5" | 0.187" | 0.094" | 1/4"-20 | 0000000 | 000000 |
16 | 32 | 45° | 2" | 2.09" | 1/2" | 1" | 5/8" | Hardened | 1.87" | 0.5" | 0.187" | 0.094" | 1/4"-20 | 0000000 | 000000 |
16 | 48 | 45° | 3" | 3.09" | 1/2" | 1" | 5/8" | Hardened | 2.5" | 0.5" | 0.187" | 0.094" | 1/4"-20 | 0000000 | 000000 |
12 | 18 | 45° | 1 1/2" | 1.62" | 3/4" | 1.25" | 5/8" | Hardened | 1.34" | 0.5" | 0.187" | 0.094" | 1/4"-20 | 0000000 | 000000 |
Right Hand | |||||||||||||||
Keyed Bore with Set Screw—1137 Carbon Steel | |||||||||||||||
16 | 16 | 45° | 1" | 1.09" | 1/2" | 1" | 1/2" | Hardened | 0.86" | 0.5" | 0.125" | 0.062" | 1/4"-20 | 0000000 | 00000 |
16 | 24 | 45° | 1 1/2" | 1.59" | 1/2" | 1" | 5/8" | Hardened | 1.37" | 0.5" | 0.187" | 0.094" | 1/4"-20 | 0000000 | 000000 |
16 | 32 | 45° | 2" | 2.09" | 1/2" | 1" | 5/8" | Hardened | 1.87" | 0.5" | 0.187" | 0.094" | 1/4"-20 | 0000000 | 000000 |
16 | 48 | 45° | 3" | 3.09" | 1/2" | 1" | 5/8" | Hardened | 2.5" | 0.5" | 0.187" | 0.094" | 1/4"-20 | 0000000 | 000000 |
12 | 18 | 45° | 1 1/2" | 1.62" | 3/4" | 1.25" | 5/8" | Hardened | 1.34" | 0.5" | 0.187" | 0.094" | 1/4"-20 | 0000000 | 000000 |
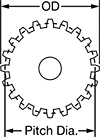
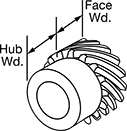
Hub | ||||||||||||
---|---|---|---|---|---|---|---|---|---|---|---|---|
Module | Number of Teeth | Helix Angle | Gear Pitch Dia., mm | OD, mm | Face Wd., mm | Overall Wd., mm | For Shaft Dia., mm | Teeth Heat Treatment | Dia., mm | Wd., mm | Each | |
Left Hand | ||||||||||||
Round Bore—4140 Alloy Steel | ||||||||||||
1 | 20 | 21 1/2° | 20 | 22 | 8 | 18 | 6 | Hardened | 17 | 10 | 00000000 | 000000 |
1 | 30 | 21 1/2° | 30 | 32 | 8 | 18 | 10 | Hardened | 25 | 10 | 00000000 | 000000 |
1 | 44 | 21 1/2° | 44 | 46 | 8 | 18 | 10 | Hardened | 30 | 10 | 00000000 | 000000 |
Right Hand | ||||||||||||
Round Bore—4140 Alloy Steel | ||||||||||||
1 | 20 | 21 1/2° | 20 | 22 | 8 | 18 | 6 | Hardened | 17 | 10 | 00000000 | 00000 |
1 | 30 | 21 1/2° | 30 | 32 | 8 | 18 | 10 | Hardened | 25 | 10 | 00000000 | 000000 |
1 | 44 | 21 1/2° | 44 | 46 | 8 | 18 | 10 | Hardened | 30 | 10 | 00000000 | 000000 |
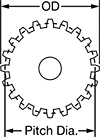
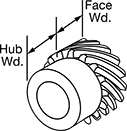
Hub | ||||||||||||
---|---|---|---|---|---|---|---|---|---|---|---|---|
Module | Number of Teeth | Helix Angle | Gear Pitch Dia., mm | OD, mm | Face Wd., mm | Overall Wd., mm | For Shaft Dia., mm | Teeth Heat Treatment | Dia., mm | Wd., mm | Each | |
Left Hand | ||||||||||||
Round Bore—Black-Oxide 1045 Carbon Steel | ||||||||||||
1 | 13 | 45° | 18 | 20.38 | 10 | 20 | 6 | Not Hardened | 15 | 10 | 00000000 | 000000 |
1 | 26 | 45° | 36 | 38.77 | 10 | 20 | 10 | Not Hardened | 30 | 10 | 00000000 | 00000 |
1 | 30 | 45° | 42 | 44.43 | 10 | 20 | 10 | Not Hardened | 35 | 10 | 00000000 | 00000 |
1.5 | 10 | 45° | 21 | 24.21 | 15 | 25 | 8 | Not Hardened | 16 | 10 | 00000000 | 00000 |
1.5 | 13 | 45° | 27 | 30.58 | 15 | 25 | 10 | Not Hardened | 23 | 10 | 00000000 | 00000 |
1.5 | 26 | 45° | 55 | 58.15 | 15 | 25 | 12 | Not Hardened | 40 | 10 | 00000000 | 00000 |
Right Hand | ||||||||||||
Round Bore—Black-Oxide 1045 Carbon Steel | ||||||||||||
1 | 13 | 45° | 18 | 20.38 | 10 | 20 | 6 | Not Hardened | 15 | 10 | 00000000 | 00000 |
1 | 26 | 45° | 36 | 38.77 | 10 | 20 | 10 | Not Hardened | 30 | 10 | 00000000 | 00000 |
1 | 30 | 45° | 42 | 44.43 | 10 | 20 | 10 | Not Hardened | 35 | 10 | 00000000 | 00000 |
1.5 | 10 | 45° | 21 | 24.21 | 15 | 25 | 8 | Not Hardened | 16 | 10 | 00000000 | 00000 |
1.5 | 13 | 45° | 27 | 30.58 | 15 | 25 | 10 | Not Hardened | 23 | 10 | 00000000 | 00000 |
1.5 | 26 | 45° | 55 | 58.15 | 15 | 25 | 12 | Not Hardened | 40 | 10 | 00000000 | 00000 |