Carbide Square End Mills
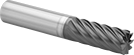
For longer tool life and a better finish in general purpose milling applications, these solid carbide end mills are harder, stronger, and more wear resistant than high-speed steel and cobalt steel end mills. Their extreme hardness means they are brittle, so a highly rigid setup, such as a CNC machine, is necessary to prevent the end mill from breaking. They have a square end for milling square slots, pockets, and edges.
End mills with fewer flutes provide better chip clearance for high-volume, high-speed plunge, slotting, and roughing cuts; end mills with more flutes provide a finer finish and operate with less vibration when run at high speeds.
Use coated end mills for demanding, high-speed jobs in hard material as well as for longer production runs. They’re more wear resistant than uncoated end mills. Titanium-aluminum-nitride (TiAlN) coated end mills dissipate heat better than other end mills, especially at high speeds. At high temperatures, the coating creates a layer of aluminum oxide that transfers heat to the chips, keeping the tool cool, even when used without lubrication.
Noncenter-cutting end mills are for operations where the peripheral teeth do most of the work, such as shoulder milling, contouring, and finishing. They cannot be used for plunge cuts.
For technical drawings and 3-D models, click on a part number.
Mill Dia. | Shank Dia. | Lg. of Cut | O'all Lg. | Flute Spacing | Helix Angle | For Use On | End Mill Type | Each | |
Titanium Aluminum Nitride (TiAlN) Coated | |||||||||
---|---|---|---|---|---|---|---|---|---|
9 Flute | |||||||||
1/2" | 1/2" | 1 1/4" | 3" | Equal | 35° | Hardened Steel, Iron, Nickel, Stainless Steel, Steel, Titanium, Tool Steel | Noncenter Cutting | 0000000 | 0000000 |
5/8" | 5/8" | 1 5/8" | 3 1/2" | Equal | 35° | Hardened Steel, Iron, Nickel, Stainless Steel, Steel, Titanium, Tool Steel | Noncenter Cutting | 0000000 | 000000 |
Fast-Cutting Carbide Square End Mills
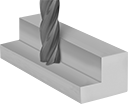
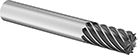
Variable spacing between the flutes reduces vibration, allowing these end mills to provide fast cuts, smooth finishes, and long tool life on hard materials. Made of solid carbide, these end mills are harder, stronger, and more wear resistant than high-speed steel and cobalt steel for the longest life and best finish on hard material. Their extreme hardness means they are brittle, so a highly rigid setup, such as a CNC machine, is necessary to prevent the end mill from breaking. They have a square end for milling square-bottomed slots, pockets, and edges.
A titanium-aluminum-nitride (TiAlN) or aluminum-titanium-nitride (AlTiN) coating allows them to dissipate heat better than other end mills, especially at high speeds. At high temperatures, the coating creates a layer of aluminum oxide that transfers heat to the chips, keeping the tool cool, even when used without lubrication. Aluminum-titanium-nitride (AlTiN) has a higher percentage of aluminum than titanium-aluminum-nitride (TiAlN).
End mills with fewer flutes provide better chip clearance for high-volume, high-speed plunge, slotting, and roughing cuts; end mills with more flutes provide a finer finish and operate with less vibration when run at high speeds.
Noncenter-cutting end mills are for operations where the peripheral teeth do most of the work, such as shoulder milling, contouring, and finishing. They cannot be used for plunge cuts.
For technical drawings and 3-D models, click on a part number.
Mill Dia. | Shank Dia. | Lg. of Cut | Overall Lg. | Flute Spacing | Helix Angle | For Use On | End Mill Type | Each | |
End Mills | |||||||||
---|---|---|---|---|---|---|---|---|---|
Aluminum Titanium Nitride (AlTiN) Coated—9 Flute | |||||||||
12mm | 12mm | 26mm | 83mm | Variable | 38° | Bronze, Hardened Steel, Iron, Nickel, Stainless Steel, Steel, Titanium, Tool Steel | Noncenter Cutting | 0000000 | 0000000 |
16mm | 16mm | 32mm | 92mm | Variable | 38° | Bronze, Hardened Steel, Iron, Nickel, Stainless Steel, Steel, Titanium, Tool Steel | Noncenter Cutting | 0000000 | 000000 |
Carbide Square End Mills for Honeycomb Panels
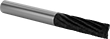
Cut into the sides and make slots in honeycomb panels without damaging any layers. Honeycomb panels are commonly used in aerospace and automotive applications because they’re strong yet lightweight, but these same qualities make them difficult to machine. Unlike normal end mills, these have a left-hand helix and push material downward as they cut, preventing layers of the composite material from separating. The serrated edges break the honeycomb into small pieces, minimizing uncut fibers that can occur in composite material. A diamond coating on these end mills allows them to machine abrasive material, such as carbon fiber, fiberglass, and graphite.
They have a square end for milling square-bottomed slots, pockets, and edges. All are center cutting, allowing plunge cuts into a surface. They are good for long production runs. They run twice as fast as other carbide end mills and last up to 30 times longer.
Made of solid carbide, these end mills are harder, stronger, and more wear resistant than high-speed steel and cobalt steel for the longest life and best finish on hard material. Their extreme hardness means they are brittle, so a highly rigid setup, such as a CNC machine, is necessary to prevent the end mill from breaking.
End mills with fewer flutes provide better chip clearance for high-volume, high-speed plunge, slotting, and roughing cuts; end mills with more flutes provide a finer finish and operate with less vibration when run at high speeds.
For technical drawings and 3-D models, click on a part number.
Mill Dia., mm | Shank Dia., mm | Lg. of Cut, mm | Overall Lg., mm | Flute Spacing | Helix Angle | For Use On | End Mill Type | Each | |
Diamond Coated | |||||||||
---|---|---|---|---|---|---|---|---|---|
9 Flute | |||||||||
12 | 12 | 36 | 110 | Equal | 15° | Carbon Fiber, Fiberglass, Graphite | Center Cutting | 0000000 | 0000000 |