About Electric Motors
When replacing a motor, use the information on your motor’s nameplate to guide your selection.
More
Brushless DC Motors
Since there are no brushes to add weight and friction, these motors can achieve a higher torque-to-weight ratio, faster speeds, and better efficiency than DC motors with brushes. All motors require a driver (sold separately) to operate.
Drivers control the speed and direction the motor spins. To program the driver, connect it to your computer with a mini USB cord (sold separately) and use the free downloadable software to enter your speed and acceleration parameters. No coding is necessary.
For technical drawings and 3-D models, click on a part number.
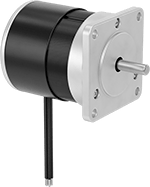
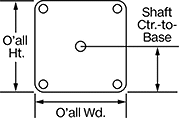
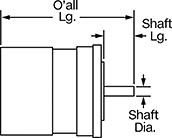
Overall | Shaft | Insulation | ||||||||||||
---|---|---|---|---|---|---|---|---|---|---|---|---|---|---|
Speed @ Continuous Operating Torque | Max. Speed, rpm | Starting Torque, in.-oz. | Full Load Current, A | Lg. | Wd. | Ht. | Shaft Type | Dia. | Lg. | Center to Base | Class | Max. Temp., °F | Each | |
30V DC | ||||||||||||||
NEMA 17 | ||||||||||||||
5,530 rpm @ 8.2 in.-oz. | 6,400 | 0.2 | 1.4 | 2 15/16" | 1 5/8" | 1 5/8" | Solid | 1/4" | 3/4" | 0.83" | A | 221° | 0000000 | 0000000 |
5,850 rpm @ 16 in.-oz. | 6,470 | 0.4 | 2.7 | 3 3/4" | 1 5/8" | 1 5/8" | Solid | 1/4" | 3/4" | 0.83" | A | 221° | 0000000 | 000000 |
6,210 rpm @ 21 in.-oz. | 6,730 | 0.6 | 3.8 | 4 1/2" | 1 5/8" | 1 5/8" | Solid | 1/4" | 3/4" | 0.83" | A | 221° | 0000000 | 000000 |
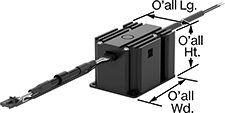
USB | Overall | ||||||||||
---|---|---|---|---|---|---|---|---|---|---|---|
For Full Load Current, A | Current, A | Input Voltage Range | Connection Gender | Connection Type | Standard | Wire Connection Type | Lg. | Wd. | Ht. | Each | |
1.4-4.9 | 7 | 12-60V DC | Female | Mini B | 2.0 | Wire Leads | 2.28" | 2.99" | 1.96" | 0000000 | 0000000 |
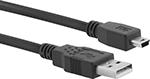
Connections | USB Standard | Color | Lg., ft. | Each | |
USB A Male Plug × USB Mini-B Male Plug | 2.0 | Black | 6 | 0000000 | 00000 |
Stepper Motors
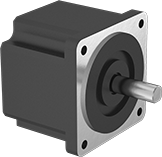
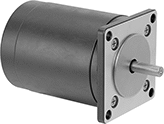
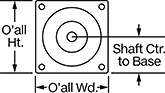
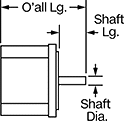
These stepper motors are good for precise, repetitive movements, such as those made by the head of a 3D printer. Similar to the hands of a clock, their shaft turns in small, equal increments. When the shaft stops, it holds its position even when a counteracting force is applied to the load. You can control the position of the load without having to configure encoders or sensors. All are bipolar hybrid stepper motors, so the current can flow in both directions. This helps them deliver higher torque, precision, and efficiency than unipolar stepper motors.
When relative positioning is critical, such as coordinating motion in a multi-axis system, choose a motor with two shafts and mount an encoder (not included) on one of them. The encoder monitors the position of the shaft and reports back to the controller.
Holding torque is the force needed to move the shaft out of position when it is stationary. When the shaft is in motion, torque generally decreases as speed increases. Use a torque-speed curve to confirm which motor will work for your application. Click on a part number and select “Product Detail” to view the curve for a motor.
Full step increment is the rotation of the shaft from one position to the next. A smaller full step increment means the rotor has more teeth, producing smoother and more precise motion. 1.8° is considered standard.
All motors require a controller and driver (not included).
For technical drawings and 3-D models, click on a part number.
O'all | Shaft | ||||||||||||||
---|---|---|---|---|---|---|---|---|---|---|---|---|---|---|---|
Max. Holding Torque, in.-oz. | Max. Speed, rpm | Max. Current per Phase, A | Full Step Increment | No. of Wire Leads | Lg. | Wd. | Ht. | Dia. | Lg. | Center to Base | Type | No. of Shafts | Temp. Range, °F | Each | |
Square Body | |||||||||||||||
NEMA 17 | |||||||||||||||
27 | 1,300 | 0.67 | 1.8° | 4 | 1.9" | 1.7" | 1.7" | 5mm | 24mm | 0.84" | Solid | 1 | 0° to 120° | 0000000 | 000000 |
39 | 1,000 | 0.62 | 1.8° | 4 | 2.1" | 1.7" | 1.7" | 5mm | 24mm | 0.84" | Solid | 1 | 0° to 120° | 0000000 | 00000 |
62.3 | 1,200 | 0.84 | 0.9° | 4 | 2.8" | 1.7" | 1.7" | 5mm | 22mm | 0.84" | D-Profile | 1 | 0° to 120° | 00000000 | 00000 |
64 | 825 | 0.7 | 1.8° | 4 | 2.3" | 1.7" | 1.7" | 5mm | 24mm | 0.84" | Solid | 1 | 0° to 120° | 0000000 | 00000 |
71 | 2,475 | 2 | 1.8° | 4 | 2.5" | 1.7" | 1.7" | 5mm | 24mm | 0.84" | Solid | 1 | 0° to 120° | 0000000 | 00000 |
84 | 820 | 1.05 | 1.8° | 4 | 2.6" | 1.7" | 1.7" | 5mm | 24mm | 0.84" | D-Profile | 1 | 0° to 120° | 0000000 | 00000 |
115 | 1,000 | 2 | 1.8° | 4 | 3.8" | 1.7" | 1.7" | 5mm | 22mm | 0.84" | D-Profile | 2 | 0° to 120° | 00000000 | 000000 |
125 | 975 | 2 | 1.8° | 4 | 3.1" | 1.7" | 1.7" | 5mm | 24mm | 0.84" | D-Profile | 1 | 0° to 120° | 0000000 | 00000 |
130.2 | 950 | 2 | 1.8° | 4 | 3.3" | 1.7" | 1.7" | 5mm | 22mm | 0.84" | Solid | 1 | 0° to 120° | 00000000 | 000000 |
Round Body | |||||||||||||||
NEMA 17 | |||||||||||||||
2.8 | 1,600 | 0.5 | 0.9° | 4 | 1.1" | 1.7" | 1.7" | 5mm | 13.1mm | 0.84" | Solid | 1 | 0° to 120° | 00000000 | 00000 |
5.6 | 1,100 | 0.6 | 0.9° | 4 | 1.1" | 1.7" | 1.7" | 5mm | 13.1mm | 0.84" | Solid | 1 | 0° to 120° | 00000000 | 00000 |
7 | 1,900 | 0.6 | 0.9° | 4 | 1.2" | 1.7" | 1.7" | 5mm | 13.1mm | 0.84" | Solid | 1 | 0° to 120° | 00000000 | 000000 |
15.5 | 1,450 | 1.2 | 0.9° | 4 | 1.4" | 1.7" | 1.7" | 5mm | 13.1mm | 0.84" | Solid | 1 | 0° to 120° | 00000000 | 000000 |
22.6 | 1,600 | 0.8 | 0.9° | 4 | 1.7" | 1.7" | 1.7" | 5mm | 13.1mm | 0.84" | Solid | 1 | 0° to 120° | 00000000 | 000000 |
Stepper Motors with Integrated Motion Control
With a built-in controller and driver, these stepper motors come ready to program and operate. Connect them to a computer and use the free downloadable software to set them up. After that, the controller can store and run programs on its own. The controller communicates to the driver which directs the motor’s shaft to move in small, equal increments. When the shaft stops, it holds its position even when a counteracting force is applied to the load. All are bipolar hybrid stepper motors, which deliver greater torque, precision, and efficiency than other types of stepper motors.
When relative positioning is critical, such as coordinating motion in a multi-axis system, choose a motor with an encoder. The encoder monitors the position of the shaft and reports back to the controller.
Holding torque is the force needed to move the shaft out of position when it is stationary. When the shaft is in motion, torque generally decreases as speed increases. Use a torque-speed curve to confirm which motor will work for your application. Click on a part number and select “Product Detail” to view the curve for a motor.
You can adjust the step resolution down to 1/256 of a full step, which translates to 51,200 microsteps per revolution. Increasing the number of steps directs an even more precise position and reduces the step-step-step motion to mimic a smooth, continuous rotation. The higher the number of step resolution settings, the greater the flexibility you have for determining the size of the motor’s step.
For technical drawings and 3-D models, click on a part number.
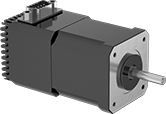
O'all | Shaft | |||||||||||||||
---|---|---|---|---|---|---|---|---|---|---|---|---|---|---|---|---|
Max. Holding Torque, in.-oz. | Max. Speed, rpm | Current per Phase, A | DC Voltage | Full Step Increment | Step Resolution | No. of Inputs/Outputs | Lg. | Wd. | Ht. | Dia. | Lg. | Center to Base | Type | Temp. Range, °F | Each | |
Motors/Controllers/Drivers | ||||||||||||||||
NEMA 17 | ||||||||||||||||
40.3 | 1,200 | 0.1-2 | 12-40 | 1.8° | 1; 1/2; 1/4; 1/8; 1/16; 1/32; 1/64; 1/128; 1/256 | 2 Digital Inputs/Outputs | 2.3" | 1.7" | 1.7" | 5mm | 22mm | 0.84" | Solid | 0° to 120° | 0000000 | 0000000 |
74.9 | 1,000 | 0.1-2 | 12-40 | 1.8° | 1; 1/2; 1/4; 1/8; 1/16; 1/32; 1/64; 1/128; 1/256 | 2 Digital Inputs/Outputs | 2.5" | 1.7" | 1.7" | 5mm | 22mm | 0.84" | Solid | 0° to 120° | 0000000 | 000000 |
85.4 | 820 | 0.1-2 | 12-40 | 1.8° | 1; 1/2; 1/4; 1/8; 1/16; 1/32; 1/64; 1/128; 1/256 | 2 Digital Inputs/Outputs | 2.8" | 1.7" | 1.7" | 5mm | 22mm | 0.84" | Solid | 0° to 120° | 0000000 | 000000 |
Motors/Controllers/Drivers/Encoders | ||||||||||||||||
NEMA 17 | ||||||||||||||||
31 | 3,000 | 0.1-2.2 | 12-48 | 1.8° | 1 to 1/256 | 1 Analog Input, 3 Digital Inputs, 1 Digital Output | 3.7" | 1.7" | 3" | 5mm | 22mm | 0.84" | D-Profile | 35° to 100° | 00000000 | 000000 |
54 | 3,000 | 0.1-2.2 | 12-48 | 1.8° | 1 to 1/256 | 1 Analog Input, 3 Digital Inputs, 1 Digital Output | 3.9" | 1.7" | 3" | 5mm | 22mm | 0.84" | D-Profile | 35° to 100° | 00000000 | 000000 |
68 | 3,000 | 0.1-2.2 | 12-48 | 1.8° | 1 to 1/256 | 1 Analog Input, 3 Digital Inputs, 1 Digital Output | 4.2" | 1.7" | 3" | 5mm | 22mm | 0.84" | D-Profile | 35° to 100° | 00000000 | 000000 |
Stepper Motors with Linear Actuation
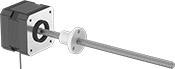
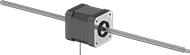
Instead of a shaft, these stepper motors have a lead screw that converts rotational motion to linear motion. Moving in increments smaller than the thickness of a sheet of paper, they're ideal for applications that require fine motion control, such as positioning electrical components on a circuit board. They move in equal steps and hold their position when stationary, so they do not require encoders, sensors, or other position feedback devices. The lead screw is built into the motor, so there are fewer points of failure than systems that use a shaft coupling to connect the lead screw. All are bipolar hybrid stepper motors, which deliver greater torque, precision, and efficiency than other types of stepper motors.
External lead screw stepper motors work similar to a traditional linear motion system; attach the load to the flanged nut, which travels back and forth along the lead screw.
Pass-through lead screw stepper motors give you the most design versatility because there are two ways to move your load: on the motor body or on the ends of the lead screw. The motor moves when the lead screw is fixed or the lead screw moves when the motor body is fixed.
Travel distance per full step determines the control you have over the motor’s positioning. The smaller the measurement, the finer positioning control you have, but the more steps it will take to go the same distance.
Dynamic load capacity is the maximum load a motor can move. If you increase the speed, the dynamic load capacity decreases. Click on a part number and select "Product Detail" to view the load-speed chart and confirm the motor will work for your application.
All motors require a driver and controller (not included).
For technical drawings and 3-D models, click on a part number.
O'all | |||||||||||||||
---|---|---|---|---|---|---|---|---|---|---|---|---|---|---|---|
Travel Distance per Full Step | Travel Lg. | Dynamic Load Capacity, lbs. | Max. Speed, in./sec. | Max. Current per Phase | Full Step Increment | Polarity | No. of Wire Leads | Lg. | Wd. | Ht. | Lead Screw Lg. | Thread Size | Temp. Range, °F | Each | |
External Lead Screw | |||||||||||||||
NEMA 17 | |||||||||||||||
0.0003125" | 5.2" | 78 | 0.4 | 1.5A | 1.8° | Bipolar | 4 | 7.3" | 1.7" | 1.7" | 6" | 1/4"-16 | 35° to 130° | 0000000 | 0000000 |
0.0003125" | 11.2" | 78 | 0.4 | 1.5A | 1.8° | Bipolar | 4 | 13.3" | 1.7" | 1.7" | 12" | 1/4"-16 | 35° to 130° | 0000000 | 000000 |
0.000625" | 5.2" | 50 | 1.2 | 1.5A | 1.8° | Bipolar | 4 | 7.3" | 1.7" | 1.7" | 6" | 1/4"-16 | 35° to 130° | 0000000 | 000000 |
0.000625" | 5.2" | 75 | 1.1 | 2.6A | 1.8° | Bipolar | 4 | 7.9" | 1.7" | 1.7" | 6" | 1/4"-16 | 35° to 130° | 0000000 | 000000 |
0.000625" | 11.2" | 50 | 1.2 | 1.5A | 1.8° | Bipolar | 4 | 13.3" | 1.7" | 1.7" | 12" | 1/4"-16 | 35° to 130° | 0000000 | 000000 |
0.000625" | 11.2" | 75 | 1.1 | 2.6A | 1.8° | Bipolar | 4 | 13.9" | 1.7" | 1.7" | 12" | 1/4"-16 | 35° to 130° | 0000000 | 000000 |
0.00125" | 5.2" | 25 | 2 | 1.5A | 1.8° | Bipolar | 4 | 7.3" | 1.7" | 1.7" | 6" | 1/4"-16 | 35° to 130° | 0000000 | 000000 |
0.00125" | 5.2" | 60 | 2.1 | 2.6A | 1.8° | Bipolar | 4 | 7.9" | 1.7" | 1.7" | 6" | 1/4"-16 | 35° to 130° | 0000000 | 000000 |
0.00125" | 11.2" | 25 | 2 | 1.5A | 1.8° | Bipolar | 4 | 13.3" | 1.7" | 1.7" | 12" | 1/4"-16 | 35° to 130° | 0000000 | 000000 |
0.00125" | 11.2" | 60 | 2.1 | 2.6A | 1.8° | Bipolar | 4 | 13.9" | 1.7" | 1.7" | 12" | 1/4"-16 | 35° to 130° | 0000000 | 000000 |
0.0025" | 6.2" | 28 | 3.9 | 2.6A | 1.8° | Bipolar | 4 | 7.9" | 1.7" | 1.7" | 6" | 1/4"-16 | 35° to 130° | 0000000 | 000000 |
0.0025" | 11.2" | 28 | 3.9 | 2.6A | 1.8° | Bipolar | 4 | 13.9" | 1.7" | 1.7" | 12" | 1/4"-16 | 35° to 130° | 0000000 | 000000 |
Pass-Through Lead Screw | |||||||||||||||
NEMA 17 | |||||||||||||||
0.0003125" | 4.6" | 78 | 0.4 | 1.5A | 1.8° | Bipolar | 4 | 6.3" | 1.7" | 1.7" | 6" | 1/4"-16 | 35° to 130° | 0000000 | 000000 |
0.0003125" | 10.5" | 78 | 0.4 | 1.5A | 1.8° | Bipolar | 4 | 12.3" | 1.7" | 1.7" | 12" | 1/4"-16 | 35° to 130° | 0000000 | 000000 |
0.000625" | 4" | 118 | 0.9 | 2.6A | 1.8° | Bipolar | 4 | 6.3" | 1.7" | 1.7" | 6" | 1/4"-16 | 35° to 130° | 0000000 | 000000 |
0.000625" | 4.6" | 56 | 0.8 | 1.5A | 1.8° | Bipolar | 4 | 6.3" | 1.7" | 1.7" | 6" | 1/4"-16 | 35° to 130° | 0000000 | 000000 |
0.000625" | 10.1" | 75 | 1.1 | 2.6A | 1.8° | Bipolar | 4 | 12.3" | 1.7" | 1.7" | 12" | 1/4"-16 | 35° to 130° | 0000000 | 000000 |
0.000625" | 10.6" | 50 | 1.2 | 1.5A | 1.8° | Bipolar | 4 | 12.3" | 1.7" | 1.7" | 12" | 1/4"-16 | 35° to 130° | 0000000 | 000000 |
0.000625" | 16" | 118 | 0.9 | 2.6A | 1.8° | Bipolar | 4 | 18.3" | 1.7" | 1.7" | 18" | 1/4"-16 | 35° to 130° | 0000000 | 000000 |
0.000625" | 16.6" | 56 | 0.8 | 1.5A | 1.8° | Bipolar | 4 | 18.3" | 1.7" | 1.7" | 18" | 1/4"-16 | 35° to 130° | 0000000 | 000000 |
0.00125" | 4" | 61 | 1.9 | 2.6A | 1.8° | Bipolar | 4 | 6.3" | 1.7" | 1.7" | 6" | 1/4"-16 | 35° to 130° | 0000000 | 000000 |
0.00125" | 4.6" | 24 | 1.9 | 1.5A | 1.8° | Bipolar | 4 | 6.3" | 1.7" | 1.7" | 6" | 1/4"-16 | 35° to 130° | 0000000 | 000000 |
0.00125" | 10.1" | 60 | 2.1 | 2.6A | 1.8° | Bipolar | 4 | 12.3" | 1.7" | 1.7" | 12" | 1/4"-16 | 35° to 130° | 0000000 | 000000 |
0.00125" | 10.6" | 25 | 2 | 1.5A | 1.8° | Bipolar | 4 | 12.3" | 1.7" | 1.7" | 12" | 1/4"-16 | 35° to 130° | 0000000 | 000000 |
0.00125" | 16" | 61 | 1.9 | 2.6A | 1.8° | Bipolar | 4 | 18.3" | 1.7" | 1.7" | 18" | 1/4"-16 | 35° to 130° | 0000000 | 000000 |
0.00125" | 16.6" | 24 | 1.9 | 1.5A | 1.8° | Bipolar | 4 | 18.3" | 1.7" | 1.7" | 18" | 1/4"-16 | 35° to 130° | 0000000 | 000000 |
0.0025" | 4" | 28 | 3.9 | 2.6A | 1.8° | Bipolar | 4 | 6.3" | 1.7" | 1.7" | 6" | 1/4"-16 | 35° to 130° | 0000000 | 000000 |
0.0025" | 10" | 28 | 3.9 | 2.6A | 1.8° | Bipolar | 4 | 12.3" | 1.7" | 1.7" | 12" | 1/4"-16 | 35° to 130° | 0000000 | 000000 |
Wet-Location Stepper Motors
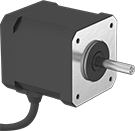
To precisely position loads in automated systems that are frequently rinsed, these stepper motors are IP65 rated to seal out water. Their shaft turns in small, equal increments, similar to the hands of a clock. When the shaft stops, it holds its position even when force is applied to the load. This means you don’t need to configure encoders or sensors to control the position of the load. All are hybrid bipolar stepper motors, so they have more torque, precision, and efficiency than other stepper motors.
Holding torque is the force needed to move the shaft out of position when it’s stationary. When the shaft is in motion, torque generally decreases as speed increases. Use a torque-speed curve to confirm which motor will work for your application. Click on a part number and select “Product Detail” to view the curve for a motor.
These stepper motors require a controller and a driver (not included).
For technical drawings and 3-D models, click on a part number.
Overall | Shaft | |||||||||||||||
---|---|---|---|---|---|---|---|---|---|---|---|---|---|---|---|---|
Max. Holding Torque, in.-oz. | Max. Speed, rpm | Max. Current per Phase, A | Full Step Increment | Polarity | No. of Wire Leads | Lg. | Wd. | Ht. | Dia. | Lg. | Center to Base | Type | Temp. Range, °F | Environmental Rating | Each | |
NEMA 17 | ||||||||||||||||
85.4 | 1,600 | 2.1 | 1.8° | Bipolar | 4 | 2.9" | 1.7" | 1.7" | 5mm | 22mm | 0.84" | Solid | 0° to 120° | IP65 | 0000000 | 0000000 |
125 | 975 | 2 | 1.8° | Bipolar | 4 | 3.6" | 1.7" | 1.7" | 5mm | 24mm | 0.84" | D-Profile | 0° to 120° | IP65 | 00000000 | 000000 |
Economy Stepper Motors
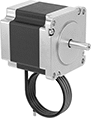
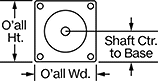
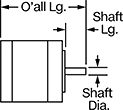
Often used in prototyping, these light duty stepper motors deliver precise, repeatable motion. Their shaft turns in small, equal increments, similar to the hands of a clock. When the shaft stops, it holds its position even when a counteracting force is applied to the load. You can control the position of the load without having to configure encoders or sensors. All are bipolar hybrid stepper motors, so the current can flow in both directions. This helps them deliver higher precision than unipolar stepper motors.
Holding torque is the force needed to move the shaft out of position when it is stationary. When the shaft is in motion, torque generally decreases as speed increases. Use a torque-speed curve to confirm which motor will work for your application. Click on a part number and select “Product Detail” to view the curve for a motor.
Full step increment is the rotation of the shaft from one position to the next. A smaller full step increment produces smoother and more precise motion. A smaller full step increment means the rotor has more teeth, producing smoother and more precise motion. 1.8° is considered standard.
All motors require a controller and driver (not included).
For technical drawings and 3-D models, click on a part number.
O'all | Shaft | ||||||||||||||
---|---|---|---|---|---|---|---|---|---|---|---|---|---|---|---|
Max. Holding Torque, in.-oz. | Max. Speed, rpm | Max. Current per Phase, A | Full Step Increment | Polarity | No. of Wire Leads | Lg. | Wd. | Ht. | Dia., mm | Lg., mm | Center to Base | Type | Temp. Range | Each | |
NEMA 17 | |||||||||||||||
32.5 | 260 | 0.33 | 1.8° | Bipolar | 4 | 2.3" | 1.7" | 1.7" | 5 | 24 | 0.83" | Solid | Not Rated | 0000000 | 000000 |
68 | 1,000 | 1.7 | 0.9° | Bipolar | 4 | 2.8" | 1.7" | 1.7" | 5 | 24 | 0.83" | Solid | Not Rated | 0000000 | 00000 |
Stepper Motors with Driver
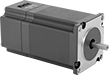
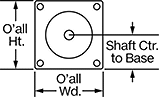
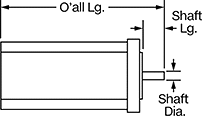
Reduce the size and complexity of your stepper motor setup—these motors have a driver built in, so you don’t need to run cable to a standalone driver. The driver delivers power to the motor based on signals from a PLC, pulse generator, or other controller. These motors are good for precise, repetitive movements, such as those made by the head of a 3D printer. Similar to the hands of a clock, their shaft turns in small, equal increments for smooth motion. When the shaft stops, it holds its position even when a counteracting force is applied to the load. You can control the position of the load without having to configure encoders or sensors. All are bipolar hybrid stepper motors, so the current can flow in both directions. This helps them deliver higher torque, precision, and efficiency than unipolar stepper motors.
Holding torque is the force needed to move the shaft out of position when it’s stationary. When the shaft is in motion, torque generally decreases as speed increases. Use a torque-speed curve to confirm which motor will work for your application. Click on a part number and select “Product Detail” to view the curve for a motor.
Full step increment is the rotation of the shaft from one position to the next. A smaller full step increment means the rotor has more teeth, producing smoother and more precise motion. 1.8° is considered standard.
Reduce the step resolution to break a full step into smaller steps for smoother motion. For example, setting a 1/256 step resolution on your driver divides one full step into 256 smaller steps.
For technical drawings and 3-D models, click on a part number.
O'all | Shaft | ||||||||||||||||
---|---|---|---|---|---|---|---|---|---|---|---|---|---|---|---|---|---|
Max. Holding Torque, in.-oz. | Max. Speed, rpm | Current per Phase, A | DC Voltage | Full Step Increment | Step Resolution | Polarity | No. of Wire Leads | Lg. | Wd. | Ht. | Dia. | Lg. | Center to Base | Type | Temp. Range, °F | Each | |
NEMA 17 | |||||||||||||||||
31 | 660 | 0.07-0.71 | 12-24 | 1.8° | 1; 1/2; 1/4; 1/8 | Bipolar | 7 | 3.2" | 1.7" | 1.7" | 5mm | 21.8mm | 0.85" | D-Profile | 0° to 120° | 00000000 | 0000000 |
50 | 720 | 0.08-0.85 | 12-24 | 1.8° | 1; 1/2; 1/4; 1/8 | Bipolar | 7 | 3.4" | 1.7" | 1.7" | 5mm | 21.8mm | 0.85" | D-Profile | 0° to 120° | 00000000 | 000000 |
62 | 720 | 0.08-0.85 | 12-24 | 1.8° | 1; 1/2; 1/4; 1/8 | Bipolar | 7 | 3.7" | 1.7" | 1.7" | 5mm | 21.8mm | 0.85" | D-Profile | 0° to 120° | 00000000 | 000000 |
Stepper Motors with Encoder
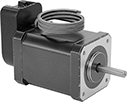
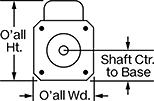
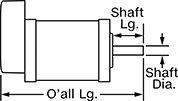
To improve positioning accuracy, these stepper motors have a built-in encoder that monitors the real-time speed and position of the shaft. It sends that data to a controller (not included), which adjusts or stops the shaft if it isn’t in the right place. This makes them useful when relative positioning is critical, such as when coordinating motion between two motors. Stepper motors are good for precise, repetitive movements. Similar to the hands of a clock, their shaft turns in small, equal increments for smooth motion. When the shaft stops, it holds its position even when a counteracting force is applied to the load. All are bipolar hybrid stepper motors, so the current can flow in both directions. This helps them deliver higher torque, precision, and efficiency than unipolar stepper motors.
Holding torque is the force needed to move the shaft out of position when it’s stationary. When the shaft is in motion, torque generally decreases as speed increases. Use a torque-speed curve to confirm which motor will work for your application. Click on a part number and select “Product Detail” to view the curve for a motor.
Full step increment is the rotation of the shaft from one position to the next. A smaller full step increment means the rotor has more teeth, producing smoother and more precise motion. 1.8° is considered standard.
All motors require a controller and driver (not included).
For technical drawings and 3-D models, click on a part number.
O'all | Shaft | ||||||||||||||||
---|---|---|---|---|---|---|---|---|---|---|---|---|---|---|---|---|---|
Max. Holding Torque, in.-oz. | Max. Speed, rpm | Max. Current per Phase, A | Full Step Increment | Encoder Positioning Type | No. of Counts per Revolution | No. of Wire Leads | Lg. | Wd. | Ht. | Dia. | Lg. | Center to Base | Type | No. of Shafts | Temp. Range, °F | Each | |
NEMA 17 | |||||||||||||||||
26.9 | 1,500 | 0.67 | 1.8° | Incremental | 1,000 | 4 | 2.6" | 2.3" | 1.7" | 5mm | 22mm | 0.84" | D-Profile | 2 | 0° to 120° | 00000000 | 0000000 |
39 | 900 | 0.62 | 1.8° | Incremental | 1,000 | 4 | 2.8" | 2.3" | 1.7" | 5mm | 22mm | 0.84" | Solid | 2 | 0° to 120° | 00000000 | 000000 |
64 | 750 | 0.7 | 1.8° | Incremental | 1,000 | 4 | 3" | 2.3" | 1.7" | 5mm | 22mm | 0.84" | Solid | 2 | 0° to 120° | 00000000 | 000000 |
70.8 | 3,000 | 2 | 1.8° | Incremental | 1,000 | 4 | 3.2" | 2.3" | 1.7" | 5mm | 22mm | 0.84" | D-Profile | 2 | 0° to 120° | 00000000 | 000000 |
83.5 | 825 | 1.05 | 1.8° | Incremental | 1,000 | 4 | 3.5" | 2.3" | 1.7" | 5mm | 22mm | 0.84" | D-Profile | 2 | 0° to 120° | 00000000 | 000000 |
124.6 | 1,400 | 2 | 1.8° | Incremental | 1,000 | 4 | 3.9" | 2.3" | 1.7" | 5mm | 22mm | 0.84" | D-Profile | 2 | 0° to 120° | 00000000 | 000000 |
130.2 | 950 | 2 | 1.8° | Incremental | 1,000 | 4 | 3.9" | 2.3" | 1.7" | 5mm | 22mm | 0.84" | Solid | 2 | 0° to 120° | 00000000 | 000000 |
Hollow-Shaft Stepper Motors
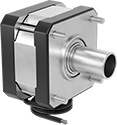
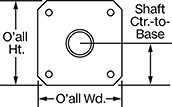
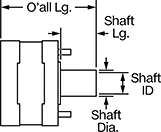
Route light beams, wire, or tubing through the hollow shaft of these stepper motors when space is tight. Often used in robotics and optical equipment, they're good for precise, repetitive movements. Similar to the hands of a clock, their shaft turns in small, equal increments for smooth motion. When the shaft stops, it holds its position even when a counteracting force is applied to the load. You can control the position of the load without having to configure encoders, sensors, or other position feedback devices. All are bipolar hybrid stepper motors, so the current can flow in both directions. This helps them deliver higher torque, precision, and efficiency than unipolar stepper motors.
Holding torque is the force needed to move the shaft out of position when it is stationary. When the shaft is in motion, torque generally decreases as speed increases. Use a torque-speed curve to confirm which motor will work for your application. Click on a part number and select “Product Detail” to view the curve for a motor.
Full step increment is the rotation of the shaft from one position to the next. A smaller full step increment means the rotor has more teeth, producing smoother and more precise motion. 1.8° is considered standard.
All motors require a controller and driver (not included).
For technical drawings and 3-D models, click on a part number.
O'all | Shaft | |||||||||||||||
---|---|---|---|---|---|---|---|---|---|---|---|---|---|---|---|---|
Max. Holding Torque, in.-oz. | Max. Speed, rpm | Max. Current per Phase, A | Full Step Increment | No. of Wire Leads | Lg. | Wd. | Ht. | Dia. | Lg. | Center to Base | Type | ID | No. of Shafts | Temp. Range, °F | Each | |
NEMA 17 | ||||||||||||||||
16.9 | 1,475 | 1.2 | 0.9° | 4 | 1.9" | 1.7" | 1.7" | 1/2" | 3/4" | 0.84" | Hollow | 7/16" | 1 | 0° to 120° | 00000000 | 0000000 |
33.9 | 1,700 | 1.4 | 0.9° | 4 | 2.5" | 1.7" | 1.7" | 1/2" | 3/4" | 0.84" | Hollow | 7/16" | 1 | 0° to 120° | 00000000 | 000000 |
Clean Room Stepper Motors
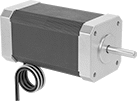
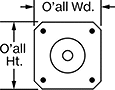
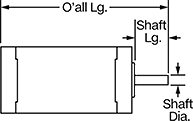
Deliver precise, repeatable motion in applications where contamination is a concern, such as semiconductor manufacturing. These motors meet the strictest clean room standards—all components are cleaned and assembled in a clean room and stored in vacuum sealed packaging. Made of treated aluminum, they minimize gas and particle emission in your clean room’s environment. They're often used in vacuum chambers, where low particle emission prevents the vacuum from degrading. Similar to the hands of a clock, the shaft on these stepper motors turns in small, equal increments for smooth motion. When the shaft stops, it holds its position even when a counteracting force is applied to the load. You can control the position of the load without having to configure encoders, sensors, or other position feedback devices. All are bipolar hybrid stepper motors, so the current can flow in both directions. This helps them deliver higher torque, precision, and efficiency than unipolar stepper motors.
Holding torque is the force needed to move the shaft out of position when it’s stationary. When the shaft is in motion, torque generally decreases as speed increases. Use a torque-speed curve to confirm which motor will work for your application. Click on a part number and select “Product Detail” to view the curve for a motor.
Full step increment is the rotation of the shaft from one position to the next. A smaller full step increment means the rotor has more teeth, producing smoother and more precise motion. 1.8° is considered standard.
All motors require a controller and driver (not included).
For technical drawings and 3-D models, click on a part number.
O'all | Shaft | |||||||||||||||
---|---|---|---|---|---|---|---|---|---|---|---|---|---|---|---|---|
Max. Holding Torque, in.-oz. | Max. Speed, rpm | Max. Current per Phase, A | Full Step Increment | No. of Wire Leads | Lg. | Wd. | Ht. | Dia., mm | Lg., mm | Type | No. of Shafts | Vacuum Rating, Torr | Temp. Range, °F | Environmental Rating | Each | |
NEMA 17 | ||||||||||||||||
85.4 | 850 | 1.05 | 1.8° | 4 | 2.9" | 1.7" | 1.7" | 5 | 22 | Solid | 1 | 1 × 10-7 | 0° to 120° | ISO Class 1 | 0000000 | 000000000 |
115.1 | 1,150 | 2 | 1.8° | 4 | 3.3" | 1.7" | 1.7" | 5 | 22 | Solid | 1 | 1 × 10-7 | 0° to 120° | ISO Class 1 | 0000000 | 00000000 |
High-Temperature Stepper Motors

The widest temperature range of any stepper motor we offer—these motors were designed with grease and magnets that are particularly good for temperatures up to 212° F. They also work well in low temperatures down to -40° F. Similar to the hands of a clock, their shaft turns in small, equal increments. When the shaft stops, it holds its position even when a counteracting force is applied to the load. You can control the position of the load without having to configure encoders, sensors, or other position feedback devices. All are bipolar hybrid stepper motors, so the current can flow in both directions. This helps them deliver higher torque, precision, and efficiency than unipolar stepper motors.
Holding torque is the force needed to move the shaft out of position when it’s stationary. When the shaft is in motion, torque generally decreases as speed increases. Use a torque-speed curve to confirm which motor will work for your application. Click on a part number and select “Product Detail” to view the curve for a motor.
Full step increment is the rotation of the shaft from one position to the next. A smaller full step increment means the rotor has more teeth, producing smoother and more precise motion. 1.8° is considered standard.
All motors require a controller and driver (not included).
For technical drawings and 3-D models, click on a part number.
Overall | Shaft | ||||||||||||||
---|---|---|---|---|---|---|---|---|---|---|---|---|---|---|---|
Max. Holding Torque, in.-oz. | Max. Speed, rpm | Max. Current per Phase, A | Full Step Increment | Polarity | No. of Wire Leads | Lg. | Wd. | Ht. | Dia. | Lg. | Center to Base | Type | Temp. Range, °F | Each | |
NEMA 17 | |||||||||||||||
85.4 | 820 | 1.05 | 1.8° | Bipolar | 4 | 2.8" | 1.7" | 1.7" | 5mm | 24mm | 0.84" | D-Profile | -40° to 212° | 0000000 | 0000000 |
115.1 | 975 | 2 | 1.8° | Bipolar | 4 | 3.285" | 1.7" | 1.7" | 5mm | 24mm | 0.84" | D-Profile | -40° to 212° | 0000000 | 000000 |
Stepper Servomotors with Integrated Drive
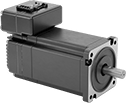
Simplify your servomotor setup—these servomotors have a built-in drive, removing the need for cable between the motor and drive. They create high torque at low speeds like traditional stepper motors but with greater torque performance and positioning reliability.
These servomotors accept step and direction, position, speed, torque, or sequencing commands. Use a computer to set up and calibrate the motor to your system. After initial setup, use a separate controller, such as a programmable logic controller (PLC), microcontroller, or indexer. You can also store target positions with speeds and accelerations in the drive and then trigger each sequence with minimal input from a controller. The encoder relays distance, direction, and speed back to the servomotor. Based on this feedback, the servomotor dynamically adapts its movements to increase system efficiency.
Holding torque is the force needed to move the shaft out of position when it is stationary. Torque generally decreases as speed increases. Use a torque-speed curve to confirm which motor will work for your application. Click on a part number and select "Product Detail" to view the curve for a motor.
For technical drawings and 3-D models, click on a part number.
O'all | Shaft | No. of Inputs/Outputs | |||||||||||||||
---|---|---|---|---|---|---|---|---|---|---|---|---|---|---|---|---|---|
Max. Holding Torque, in.-oz. | Max. Speed, rpm | Voltage | Current, A | Step Resolution | Lg. | Wd. | Ht. | Dia. | Lg. | Center to Base | Communication Protocol | Digital Inputs | Analog Inputs | Digital Outputs | Environmental Rating | Each | |
NEMA 17 | |||||||||||||||||
40 | 3,000 | 12-48V DC | 1.3 | 1 to 1/256 | 3.5" | 1.7" | 3" | 6mm | 18mm | 0.83" | Modbus RTU | 8 | 1 | 4 | IP20 | 0000000 | 0000000 |
59 | 3,000 | 12-48V DC | 1.4 | 1 to 1/256 | 3.7" | 1.7" | 3" | 6mm | 18mm | 0.83" | Modbus RTU | 8 | 1 | 4 | IP20 | 0000000 | 000000 |
73 | 3,000 | 12-48V DC | 1.3 | 1 to 1/256 | 4.1" | 1.7" | 3" | 6mm | 18mm | 0.83" | Modbus RTU | 8 | 1 | 4 | IP20 | 0000000 | 000000 |
Stepper Servomotors
Combine the high torque at low speeds that traditional stepper motors are known for with the greater torque performance and positioning reliability of a servomotor. They create rotary motion based on signals from a drive (sold separately). As these servomotors move, their encoder relays the shaft’s distance, direction, and speed back to the drive. The drive increases your system’s efficiency by taking the electrical signal from the encoder and dynamically adapting the motor’s movements, also accounting for inconsistent loads and unexpected forces.
Drives have several control modes that power the motor—sequencing, position, speed, or torque. You can program target positions with speeds and accelerations in the drive to trigger sequences with minimal input from a controller. You can also use a computer, programmable logic controller (PLC), microcontroller, or indexer to set motion parameters, tune the motor to your mechanical system, and stream multiple commands to the driver to carry out complex motion sequences.
For technical drawings and 3-D models, click on a part number.
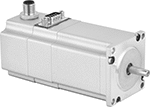
Holding torque is the force needed to move the shaft out of position when it is stationary. Torque generally decreases as speed increases. Use a torque-speed curve to confirm which motor will work for your application. Click on a part number and select "Product Detail" to view the curve for a motor.
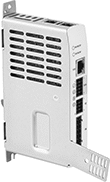
O'all | No. of Inputs/Outputs | |||||||||
---|---|---|---|---|---|---|---|---|---|---|
Max. Current per Phase, A | Communication Protocol | Operating Voltage | Lg. | Wd. | Ht. | Inputs | Outputs | Environmental Rating | Each | |
For 48V DC Motor Voltage | ||||||||||
20 | EtherCAT, Ethernet/IP, Modbus TCP/IP, Profinet, TCP/IP | 24-48V DC | 5.2" | 1.1" | 6.7" | 2 | 2 | IP20 | 00000000 | 0000000 |
Multi-Axis Stepper Motor Actuators
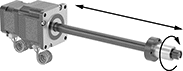
Precisely drive both linear and rotary motion from one compact system. Often found in pick-and-place equipment, these actuators have two stepper motors. Each stepper motor drives one type of motion, and you can control them separately. When stopped, they hold their position even when a counteracting force is applied to the load.
Actuators with an encoder are useful in applications where relative positioning is critical, such as coordinating motion between multiple actuators. The encoder monitors the position of the actuator and reports back to a controller (not included), which adjusts or stops the shaft if it isn’t in the right place.
To confirm which actuator will work for your application, click on a part number and select "Product Detail" to view the torque-speed curve and dynamic load-speed chart. Holding torque is the force needed to move the actuator out of position when it’s stationary. When the actuator is rotating, torque generally decreases as speed increases. Dynamic load capacity is the maximum load an actuator can move linearly. If you increase the speed, the dynamic load capacity decreases.
Travel distance per full step determines the control you have over the actuator's linear positioning. The smaller the measurement, the finer positioning control you have, but the more steps it will take to go the same distance.
Full step increment refers to how much the actuator rotates when it takes a full step. A smaller full step increment means the rotor has more teeth, producing smoother and more precise motion. 1.8° is considered standard.
All actuators require a controller and two motor drivers (not included).
For technical drawings and 3-D models, click on a part number.
Rotary | Linear | O'all | ||||||||||||
---|---|---|---|---|---|---|---|---|---|---|---|---|---|---|
Max. Holding Torque, in.-oz. | Travel Distance per Full Step | Travel Lg. | Rotational Load Cap., in.-oz. | Max. Speed, rpm | Max. Current per Phase, A | Dynamic Load Cap., lbs. | Max. Speed, in./sec. | Max. Current per Phase, A | Full Step Increment | Lg. | Wd. | Ht. | Each | |
Actuators | ||||||||||||||
118 | 0.00125" | 6" | 48 | 900 | 2 | 5 | 2 | 1.5 | 1.8° | 11 1/2" | 2.7" | 2.2" | 0000000 | 000000000 |
Actuators with Encoder | ||||||||||||||
118 | 0.00125" | 6" | 48 | 900 | 2 | 5 | 2 | 1.5 | 1.8° | 11 1/2" | 2.7" | 2.2" | 0000000 | 00000000 |
Compact Stepper Motor Actuators
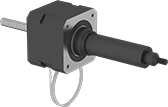
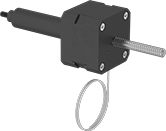
A lead screw that converts rotational motion to linear motion sits inside the motor body for a compact footprint. Add a driver and controller to these actuators to repeatedly position loads with speed and precision. Moving in small, equal steps, these actuators are good for jobs requiring fine motion control, such as positioning electrical components on a circuit board. Their load stays in position even when a counteracting force is applied, so you don’t need encoders, sensors, or other position feedback devices.
All have bipolar hybrid stepper motors, which deliver greater torque, precision, and efficiency than other types of stepper motors. The splined shaft keeps the rod from rotating as it extends and retracts.
Travel distance per full step determines the control you have over the actuator's positioning. The smaller the measurement, the finer positioning control you have, but the more steps it will take to go the same distance.
Dynamic load capacity is the maximum load an actuator can move. If you increase the speed, the dynamic load capacity decreases. Click on a part number and select "Product Detail" to view the load-speed chart and confirm the actuator will work for your application.
For technical drawings and 3-D models, click on a part number.
Dynamic Load Capacity, lbs. | ||||||||||||
---|---|---|---|---|---|---|---|---|---|---|---|---|
Travel Distance per Full Step | Stroke Lg. | Pull | Push | Max. Speed, in./sec. | Max. Current per Phase, A | Full Step Increment | Polarity | No. of Wire Leads | Extension Rod Type | Retracted Lg. | Each | |
NEMA 17 | ||||||||||||
0.00015625" | 2" | 50 | 50 | 0.4 | 1.5 | 1.8° | Bipolar | 4 | Nonrotating | 6" | 0000000 | 0000000 |
0.000625" | 2" | 50 | 50 | 1.25 | 1.5 | 1.8° | Bipolar | 4 | Nonrotating | 6" | 0000000 | 000000 |
0.000625" | 2" | 75 | 75 | 1 | 2.6 | 1.8° | Bipolar | 4 | Nonrotating | 6 3/8" | 0000000 | 000000 |
0.00125" | 2" | 60 | 60 | 2.25 | 2.6 | 1.8° | Bipolar | 4 | Nonrotating | 6 3/8" | 0000000 | 000000 |
Electric Positioning Slides
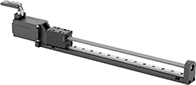
A built-in stepper motor moves the load on these slides smoothly and precisely at high speeds, similar to an inkjet printer head. They’re often used in automated assemblies and other jobs requiring accurate, repeatable motion. The motor moves in small, equal steps and holds its position when stationary, so you don’t need encoders, sensors, or other position feedback devices. With a repeatability thinner than a single sheet of paper, the carriage hits the same spot every time. The slippery coating on the drive screw acts as a permanent dry lubricant, so you won’t need to add lubricant.
All slides require a controller and driver (not included).
Anti-backlash slides minimize play, or how much space there is between the carriage and the drive screw. This keeps the carriage steady for precise positioning.
Dynamic load capacity is the maximum load slides can move. If you increase the speed, the dynamic load capacity decreases. Use a load-speed chart to confirm which slides will work for your application. Click on a part number and select "Product Detail" to view the chart.
Travel distance per full step determines the control you have over the slide's positioning. The smaller the measurement, the finer positioning control you have.
For technical drawings and 3-D models, click on a part number.
Dynamic Load Cap., lbs. | O'all | Carriage | ||||||||||||||
---|---|---|---|---|---|---|---|---|---|---|---|---|---|---|---|---|
Horizontal | Vertical | Max. Speed, in./sec. | Travel Distance per Full Step | Repeatability | Max. Current per Phase, A | Full Step Increment | No. of Wire Leads | Lg. | Wd. | Ht. | Lg. | Wd. | Bearing Type | Features | Each | |
6" Stroke Lg. | ||||||||||||||||
135 | 60 | 2 | 0.00125" | ±0.00125" | 1.3 | 1.8° | 4 | 11.4" | 1.7" | 1.7" | 2" | 1.1" | Ball | __ | 0000000 | 0000000 |
135 | 75 | 0.4 | 0.00025" | ±0.00025" | 1.3 | 1.8° | 4 | 11.4" | 1.7" | 1.7" | 2" | 1.1" | Ball | __ | 0000000 | 000000 |
12" Stroke Lg. | ||||||||||||||||
15 | 6 | 8 | 0.005" | ±0.001" | 0.7 | 1.8° | 4 | 15.1" | 1.7" | 1.7" | 0.9" | 1.1" | Ball | Anti Backlash | 0000000 | 000000 |
15 | 12 | 4 | 0.0025" | ±0.001" | 0.7 | 1.8° | 4 | 15.1" | 1.7" | 1.7" | 0.9" | 1.1" | Ball | Anti Backlash | 0000000 | 000000 |
135 | 60 | 2 | 0.00125" | ±0.00125" | 1.3 | 1.8° | 4 | 17.4" | 1.7" | 1.7" | 2" | 1.1" | Ball | __ | 0000000 | 00000000 |
135 | 75 | 0.4 | 0.00025" | ±0.00025" | 1.3 | 1.8° | 4 | 17.4" | 1.7" | 1.7" | 2" | 1.1" | Ball | __ | 0000000 | 00000000 |
24" Stroke Lg. | ||||||||||||||||
15 | 6 | 8 | 0.005" | ±0.001" | 0.7 | 1.8° | 4 | 27.1" | 1.7" | 1.7" | 0.9" | 1.1" | Ball | Anti Backlash | 0000000 | 00000000 |
15 | 12 | 4 | 0.0025" | ±0.001" | 0.7 | 1.8° | 4 | 27.1" | 1.7" | 1.7" | 0.9" | 1.1" | Ball | Anti Backlash | 0000000 | 00000000 |