Moisture-Resistant Plastic Pellets
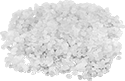
These pellets resist swelling when exposed to water, making them suitable for use in wet environments. Melt and mold them into desired shapes. Pellets are made from virgin resins and are compatible with various types of molding equipment such as injection molders and 3D printers.
Choose HDPE pellets for general-purpose applications such as protoyping.
HoPP and CoPP pellets are harder than HDPE pellets, so they won't scratch as easily. HoPP has greater tensile strength than CoPP. However, CoPP has better impact resistance. It resists impact even at low temperatures.
Container | ||||||||||||
---|---|---|---|---|---|---|---|---|---|---|---|---|
Type | Net Weight, lbs. | Molding Temperature, °F | Melting Temperature, °F | Melt Flow Rate | Shrinkage | Hardness | Impact Strength | Tensile Strength | Clarity | Specifications Met | Each | |
HDPE Plastic | ||||||||||||
White | ||||||||||||
Pail | 5 | 80° to 140° | 375° to 440° | 6 g/10 min | 1.2%-2% | Shore D62 (Medium) | 1 ft.-lbs./in. (Poor) | 4,100 psi (Poor) | Opaque | FDA Compliant 21 CFR 177.1520 | 0000000 | 0000000 |
Cardboard Box | 50 | 80° to 140° | 375° to 440° | 6 g/10 min | 1.2%-2% | Shore D62 (Medium) | 1 ft.-lbs./in. (Poor) | 4,100 psi (Poor) | Opaque | FDA Compliant 21 CFR 177.1520 | 0000000 | 000000 |
HoPP Plastic | ||||||||||||
White | ||||||||||||
Pail | 5 | 90° to 150° | 375° to 450° | 12 g/10 min | 1.3%-1.7% | Rockwell R112 (Hard) | 1 ft.-lbs./in. (Poor) | 5,600 psi (Good) | Semi-Clear | FDA Compliant 21 CFR 177.1520 | 0000000 | 00000 |
CoPP Plastic | ||||||||||||
White | ||||||||||||
Pail | 5 | 90° to 150° | 375° to 450° | 4 g/10 min | 1.3%-1.7% | Rockwell R105 (Hard) | No Break (Excellent) | 3,200 psi (Poor) | Opaque | FDA Compliant 21 CFR 177.1520 | 0000000 | 00000 |
Wear-Resistant Plastic Pellets
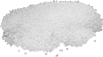
With a low coefficient of friction, these pellets won't wear away from abrasion that’s often caused by contact with moving parts. Melt and mold them into desired shapes. All of these pellets are made from virgin resins and are compatible with various types of molding equipment, such as injection molders or 3D printers. They handle high temperatures without losing their mechanical properties.
PEEK and PVDF pellets stand up to acids, alkalis, and oils. PEEK pellets are often used as a lightweight alternative for metal parts in chemical-processing applications. They will expand when exposed to moisture. PVDF pellets are more chemical resistant than PEEK pellets. They also withstand moisture better than PEEK pellets and won’t break down when exposed to UV rays.
Nylon pellets have good wear resistance, as well as chemical resistance against fuels and hydrocarbons. They will expand and contract when exposed to moisture and temperature changes.
Container | ||||||||||||
---|---|---|---|---|---|---|---|---|---|---|---|---|
Type | Net Weight, lbs. | Molding Temperature, °F | Melting Temperature, °F | Melt Flow Rate | Shrinkage | Hardness | Impact Strength | Tensile Strength | Coefficient of Friction | Clarity | Each | |
PEEK Plastic | ||||||||||||
Beige | ||||||||||||
Jar | 5 | 350° to 390° | 650° to 720° | 36 g/10 min | 1.4-1.6% | Rockwell M100 (Hard) | 0.9 ft.-lbs./in. (Poor) | 14,500 psi (Excellent) | 0.2-0.4 | Opaque | 0000000 | 0000000 |
PVDF Plastic | ||||||||||||
Off-White | ||||||||||||
Jar | 5 | 120° to 190° | 325° to 340° | 5 g/10 min | 2-3.5% | Durometer 75D (Medium) | 1.8-4 ft.-lbs./in. (Good) | 6,500 psi (Good) | 0.2 | Semi-Clear | 0000000 | 000000 |
Nylon Plastic | ||||||||||||
Off-White | ||||||||||||
Pail | 5 | 130° to 200° | 470° to 535° | Not Rated | 1.3-1.7% | Rockwell R115 (Hard) | 0.8 ft.-lbs./in (Poor) | 11,000 psi (Good) | 0.4 | Opaque | 0000000 | 000000 |
Impact-Resistant Plastic Pellets
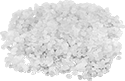
Absorbing impact without cracking or breaking, these plastic pellets are molded into parts that endure bumps, scrapes, and falls. Use them with injection molders, 3D printers, and other molding equipment.
HIPS pellets are easy to thermoform, so they’re good for signs, packaging, and other light duty applications.
ABS pellets are easy to thermoform, have good impact resistance at low temperatures, and have more chemical resistance than those made of HIPS or polycarbonate. They’re also more impact resistant than HIPS pellets. Use them to make storage cases, tote trays, equipment housings, and protective gear.
PVDF pellets are flexible, weather resistant, and have the most chemical resistance of all these materials. PVDF is also known as Kynar.
Polycarbonate pellets handle higher temperatures than any of these other materials, but they’re more difficult to thermoform. Clear in color and a lightweight alternative to glass, they’re often used to make windows, machine guards, and instrument covers.
Container | ||||||||||||
---|---|---|---|---|---|---|---|---|---|---|---|---|
Type | Net Weight, lbs. | Molding Temperature, °F | Melting Temperature, °F | Melt Flow Rate | Shrinkage | Hardness | Impact Strength | Tensile Strength | Clarity | Specifications Met | Each | |
HIPS Plastic | ||||||||||||
Off-White | ||||||||||||
Pail | 5 | 100° to 150° | 410° to 480° | 9 g/10 min | 0.3%-0.6% | Rockwell R105 (Hard) | 2 ft.-lbs./in. (Good) | 3,550 psi (Poor) | Opaque | FDA Compliant 21 CFR 177.1020 | 0000000 | 000000 |
Cardboard Box | 55 | 100° to 150° | 410° to 480° | 9 g/10 min | 0.3%-0.6% | Rockwell R105 (Hard) | 2 ft.-lbs./in. (Good) | 3,550 psi (Poor) | Opaque | FDA Compliant 21 CFR 177.1020 | 0000000 | 000000 |
ABS Plastic | ||||||||||||
Off-White | ||||||||||||
Pail | 5 | 145° to 185° | 400° to 460° | 35 g/10 min | 0.5%-0.8% | Rockwell R108 (Hard) | 5.5 ft.-lbs./in. (Excellent) | 6,500 psi (Good) | Opaque | FDA Compliant 21 CFR 177.1020 | 0000000 | 000000 |
Cardboard Box | 55 | 145° to 185° | 400° to 460° | 35 g/10 min | 0.5%-0.8% | Rockwell R108 (Hard) | 5.5 ft.-lbs./in. (Excellent) | 6,500 psi (Good) | Opaque | FDA Compliant 21 CFR 177.1020 | 0000000 | 000000 |
PVDF Plastic | ||||||||||||
Off-White | ||||||||||||
Jar | 5 | 125° to 190° | 270° to 280° | 8 g/10 min | 2%-3.5% | Durometer 57D (Medium Soft) | No Break (Excellent) | 2,000 psi (Poor) | Semi-Clear | FDA Compliant 21 CFR 177.1520 | 0000000 | 000000 |
Polycarbonate Plastic | ||||||||||||
Clear | ||||||||||||
Pail | 6 | 180° to 240° | 540° to 590° | 22 g/10 min | 0.5%-0.7% | Rockwell R120 (Hard) | 14 ft.-lbs./in. (Excellent) | 9,100 psi (Good) | Transparent | FDA Compliant 21 CFR 177.1580 | 0000000 | 000000 |
Cardboard Box | 50 | 180° to 240° | 540° to 590° | 22 g/10 min | 0.5%-0.7% | Rockwell R120 (Hard) | 14 ft.-lbs./in. (Excellent) | 9,100 psi (Good) | Transparent | FDA Compliant 21 CFR 177.1580 | 0000000 | 000000 |
Colorants for Plastic Pellets
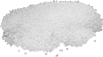











Add color when making plastic parts. Also called masterbatches, these colorants contain a base plastic that works with a variety of plastic types—from general purpose polypropylene to tough ABS. This means you don’t need to stock up on colorants for each type. Mix them in with your pellets before melting. To get a rich color for most plastic, you need only 1-2% of colorant in your batch, since they’re concentrated.
5 lbs. | |||
---|---|---|---|
Color | Maximum Temperature, °F | Each | |
For Use With ABS Plastic, Acetal Plastic, Nylon Plastic, PBT Plastic, Polycarbonate Plastic, Polyethylene Plastic, Polypropylene Plastic, Polystyrene Plastic, PVC Plastic | |||
Black | 570° | 0000000 | 0000000 |
Blue | 570° | 0000000 | 000000 |
Dark Gray | 570° | 0000000 | 000000 |
Gray | 570° | 0000000 | 000000 |
Light Blue | 570° | 0000000 | 000000 |
White | 570° | 0000000 | 000000 |
Yellow | 570° | 0000000 | 000000 |
For Use With ABS Plastic, Acetal Plastic, PBT Plastic, Polycarbonate Plastic, Polyethylene Plastic, Polypropylene Plastic, Polystyrene Plastic, PVC Plastic | |||
Green | 570° | 0000000 | 000000 |
For Use With ABS Plastic, Acetal Plastic, PBT Plastic, Polyethylene Plastic, Polypropylene Plastic, Polystyrene Plastic, PVC Plastic | |||
Dark Red | 570° | 0000000 | 000000 |
For Use With ABS Plastic, Nylon Plastic, PBT Plastic, Polystyrene Plastic, PVC Plastic | |||
Orange | 570° | 0000000 | 000000 |
For Use With Polyethylene Plastic, Polypropylene Plastic, Polystyrene Plastic, PVC Plastic | |||
Red | 570° | 0000000 | 000000 |
Foaming Agents for Plastic Molding Machines
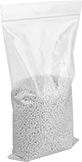
Commonly used in molding applications such as injection molding and extrusion, these foaming agents reduce weight, warpage, and sinks in finished parts. Mix them into resin as 0.5-1.5% of the total mixture—by decreasing the amount of resin needed to make a part, they help reduce costs. They also lower the melt viscosity of resin so that it can be processed at low temperatures, which reduces cooling times, cycle times, and the risk of heat degradation. These foaming agents are compatible with most plastic and rubber resins. All are FDA compliant for direct contact with food.
Agents with a 310° F or 325° F activation temperature are for use with low-melt-temperature resins such as polyolefins, polystyrenes, and thermoplastic elastomers. Agents with a 400° F activation temperature are for use with high-melt-temperature resins such as polycarbonates and polyamides.
Microfine agents produce smaller bubbles and a tighter cell structure than other foaming agents. They improve the appearance of your final product and keep its mechanical properties consistent throughout. They’re often used to create parts that have thin walls.
Fine agents produce more gas than microfine agents. Use them to ensure uniform foaming when molding bigger parts.
Activation Temperature, °F | Melting Temperature, °F | Gas Evolution | Color | Container Type | Specifications Met | Each | |
Microfine | |||||||
---|---|---|---|---|---|---|---|
325° | 250° | 30 cc/g and higher | White | Cardboard Box | FDA Compliant 21 CFR 174.5 | 0000000 | 0000000 |
325° | 250° | 65 cc/g and higher | White | Cardboard Box | FDA Compliant 21 CFR 174.5 | 0000000 | 000000 |
400° | 350° | 30 cc/g and higher | Off-White | Cardboard Box | FDA Compliant 21 CFR 174.5 | 0000000 | 000000 |
Fine | |||||||
310° | 310° | 95 cc/g and higher | White | Cardboard Box | FDA Compliant 21 CFR 174.5 | 0000000 | 000000 |